To continue the series of articles on NEMA27500 cables discussing their use on aircraft (part 1 and 2), this article focuses on the several tests that are necessary for cable verification and certification.
There is some level of performance verification for each part of an aircraft cable. Most cable assessment tests focus on the performance of additional cable components (jacket and shielding) and not on the basic wires that make up the cable. The reason for this is that the basic component wires are separately certified as individual wires. But when focusing on testing a completed cable construction, there are six ways that a specimen can be tested and/or stressed: electrical, thermal, chemical, mechanical, workability, and/or environmental. Here we review some of these cable assessment tests, what they are, and what they aim to evaluate.
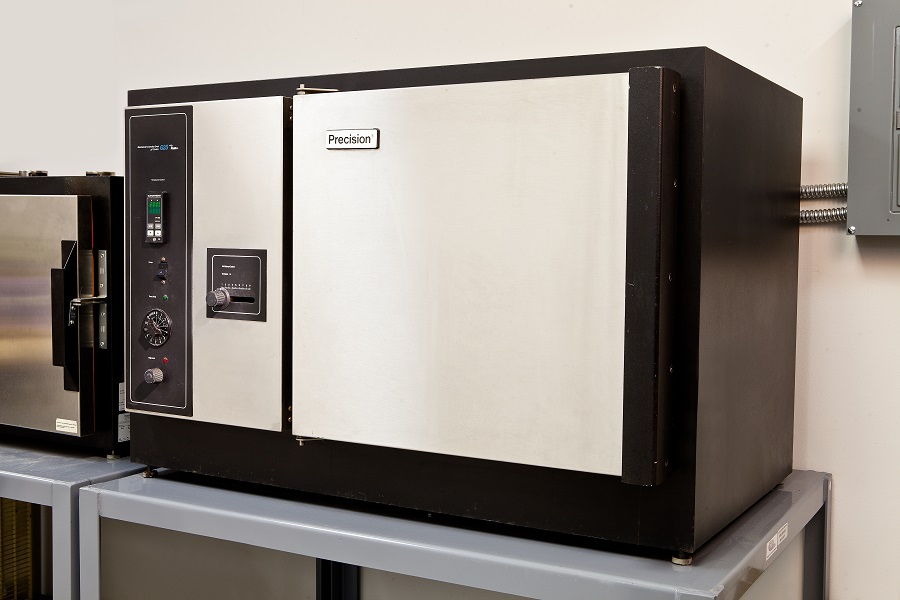
Electrical Stressing
One of the primary means for assessing any wire/cable is a dielectric test. For cables, the jacket is the primary component that is assessed with the dielectric voltage withstand test. The key when this test is performed is where and how the test is performed. If the specimen is a shielded cable, then the test is performed with the voltage applied to the shield and ground in a water bath. If the cable is not shielded, then the basic wire ends are stripped, the conductors twisted together, and connected to the voltage.
The dielectric test checks the cable in two ways: first, it checks the jacket integrity (if fluid ingress is possible); second, the test identifies jacket defects such as gaps or thin/weak parts of the jacket. This test is done both as part of cable qualification and assembly line product inspection.
Thermal Stressing
Like what is done for the individual wires, thermal stressing of the completed cable is important. Because aircraft operate in a variety of environments, the thermal stressing of cables considers both the elevated temperature exposure (such as performed with thermal shock) and low temperatures (such as cold bend). The goal with these tests is to identify:
- Adhesion of the cable to itself at elevated temperatures (such as blocking)
- Performance degradation (such as thermal shock)
- Potential stressing issues that might cause jacketing cracks (particularly with cold bend testing)
Some of these tests can be completed in a few hours, while other thermal stressing tests may take days/weeks to complete.
Chemical Evaluations
Outgassing is just as important at the cable level as it is individual wires, perhaps more so. When low fluorine outgassing is examined at the wire level, the consideration is particularly directed toward the silver platted conductors. As discussed in the first article in this series, shielding may be plated with nickel, tin, or silver. Those shields that are plated with silver are susceptible to red plague.
Flammability testing is also performed on the completed cable as part of a chemical evaluation. To think about this at the system level, the flammability of a cable may be considered three times. The first time with the individual wire components (each of these must pass their own flammability check). The second flammability check is done when the completed product must be tested in accordance with the NEMA standard at the cable level. Lastly (#3 flammability check), the completed harness may need to be tested to the FAA (or appropriate certifying body) flammability test requirements. The hope (obviously) is that the final product will have been checked so many times that the likelihood of an aerospace grade wire/cable being flammable is minimal.
Workability
Tests like solderability and stripability examine the final products’ usability. With the solderability evaluation, this examines the ability of the shielding to be soldered. This solderability of the shield is important when solder sleeves are used at connectors to maintain EMI protection. If a cable shield has poor solderability and cannot bond with the solder sleeve, this can create EMI protection issues for the shielded circuit.
Just as the ability to easily and reliably remove wire insulation is important, so it is with the jacket. To be deemed acceptable, the jacket must be able to be removed with less force than identified in the specification. Jackets with stripability forces greater than the specification can place additional burden to harness fabricators and maintainers. In particular, high strip strength can result in damage being caused to the cable because a user is more likely to damage other parts of the cable.
Smooth Surface Verification
Just like the seamless construction of the AS22759/180 – 192 family of wires, cables may also have seamless jacket construction. For those unfamiliar with this, the construction of these cables typically will have a Polyimide-PTFE jacket, and the cable jacket is designed such that there is no physically detectable seam on the jacket. To verify the seamless construction, the specimen is cleanly cross sectioned and examined under magnification to measure the jacket smoothness.
Conclusion
The rigorous testing of aerospace cables is not something that came about lightly. A great deal of trial and error was involved in defining their performance of these cables, and what areas were worth assessing at the initial and re- qualifications of these components. Since there is a broad range of cables and performance characteristics of each of these cables, please feel to contact Lectromec if you have a need for assessment, testing, or recommendations.