Today’s interview is with George Slenski, a senior electrical and electronic materials consultant. The term “subject matter expert” is thrown about casually these days. However, every now and then one encounters a person who can make the claim of deep and thorough knowledge of an area of study. George certainly fits the bill of an expert.
George Slenski started off as a humble electronics technician and then completed his bachelor’s degree in electrical engineering. After a few more years of sweating and pulling wires, he completed his master’s degree in materials engineering. Combine this with twenty-five years working at the Air Force Research Lab (AFRL) and you get a person who can combine practical hands-on knowledge with theory.
Today’s interview began with George commenting on incident investigation and then he moved to the strange concept called red plague corrosion. Nothing to do with the Center for Disease Control and Prevention, this is a description of what can happen with silver plated copper conductors.
During the discussion, George talks about Corrosion Preventing Compounds (CPCs), unintended consequences, and even carbon nanotubes.
It is a quick eighteen minute episode.
You can also read the transcript below:
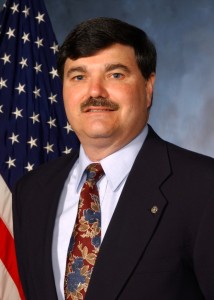
John Gilroy: Welcome to the Lectromec podcast with John Gilroy. Lectromec provides you the turnkey solution for aerospace wiring assessment, testing, and certification. The purpose of this podcast is to keep you informed of trends in the rapidly changing aerospace industry.
Today’s guest is George Slenski. He is the President of Slenski Consulting, an independent consulting for electrical and electronic materials. George has got a perfect background for this podcast. Oh my goodness, he’s got a Bachelor’s Degree in Electrical Engineering. A Master’s Degree in Material’s Engineering. He spent twenty five years a at little place called The Air Force Research Lab. Wow George, you’re perfect for this podcast, aren’t you?
George Slenski: I hope so.
John Gilroy: I think so with that background, wow! Could you maybe fill some of the blanks for our listeners of how you accumulated all this expertise in aerospace?
George Slenski: Sure. Just real quick, I did grow up in Florida. My first position actually was an Electronics Technician. That’s where I really learned about wiring and connectors and all the problems they can cause. I went on to get a degree in Electrical Engineering from the University of Florida. I met my wife who was in the ROTC in the Air Force. Her first job was at the Wright-Patterson Air Force Base in Ohio, just outside of Dayton. Birthplace of the aviation.
I was able to get a position with the Air Force Research Lab. Where I started working at was in our Electronic Failure Analysis Lab. What we did there was whenever we had a high failure rate piece of electronics on an aircraft, or there was a crash of an aircraft, and it was electrical in nature, we did the actual investigations that determine cause of failure.
John Gilroy: Wow!
George Slenski: That’s where I learned a lot about wiring. We did all types of Avionics and wiring board problems and IC’s. We kept coming back to wiring problems that was causing a lot of our failures.
John Gilroy: I don’t think it would be an exaggeration to say that you’re a subject matter expert on aerospace electrical and electronic materials. Just want to let the listeners know that we’ve got someone here that’s been there, done that, got the tee-shirt, maybe a closet full of tee shirts. Let’s start with some of your experience in accident and failure investigations.
George Slenski: Sure. There’s quite a few I could talk about. I know we want to focus on wiring, so what I thought I’d talk about is one I worked on several years actually after I retired from the Air Force, and now I do consulting. This was a crash of a fairly modern fighter, where basically the pilot was coming in for landing, developed a problem with stability of the aircraft, and lost all of his electrical systems.
He ended up ejecting from the aircraft. Aircraft impacting the ground actually near the landing strip. From the analysis, and there wasn’t much left of this aircraft, we actually determined we had an arcing of a 270 volt DC power cable to a hydraulic line. When the 270 touched the line, it burst the hydraulic line there.
John Gilroy: Oh boy.
George Slenski: Ignited the fluid, which basically propagated the failure and caused rapid loss of all the electrical systems on the aircraft.
John Gilroy: Wow!
George Slenski: Our job was to figure out why this happened. Fortunately we had a lot of information from some previous incidents and we were able to reconstruct. Basically the wire harness was not properly installed. Moved just though the high G’s that a fighter would experience, and actually touched the hydraulic line, chaffed though the insulation, and lead to the failure.
John Gilroy: My son and I have seen many action movies. We always see the pilots ejecting. What I never knew is a hundred and fifty million dollars that was being … then all of a sudden, “Now wait a minute here. That’s a hundred and fifty million dollars of my money and George’s money?” I don’t like hearing that.
George Slenski: Yes. The new aircraft are highly complex. These aircraft need the electrical systems to fly. They are unstable aerodynamically, so they can perform the maneuvers they do. They’re flown by computer. A huge amount of cost goes into these aircraft now. The electrical system is definitely one of the safety critical systems on the aircraft. Loss of power, the aircraft cannot fly. Fortunately, they could eject.
John Gilroy: The market metrics for the podcast indicate we have a lot of listeners overseas. We just tossed out a term earlier called “EWIS”, which of course stands for “Electrical Wiring Interconnection System.” We’re talking about EWIS here and problems especially with million dollar fighters.
There is a term that a radio guy like me likes to throw out and it’s a fun term. It’s called the “Red Plague.” What’s this Red Plague got anything to do with wiring and aerospace?
George Slenski: Red Plague’s a great example of a materials failure. Again, a lot of our wiring you need high conductivity, so what happens is most of our wiring is copper based. They actually put plating on the surface, in this case silver. Actually from a materials standpoint, that’s a very poor plating system because when you put silver on top of the copper, if you scratch the surface and expose the cooper, the copper is actually corroded. What it forms is copper oxide, which is red.
What happens is, it interacts with the silver and moisture. What we do is we take this highly conductive plating system and if we get some damage and some other things occur in there it will rapidly corrode, and you’ll lose your conductivity. In fact, you will corrode the wire away completely.
John Gilroy: Wow! It sounds like you have to have a background in chemistry as well to understand some of these concepts.
George Slenski: Yeah, absolutely. That’s why I ended up getting a Materials Degree. Because a lot of our problems are chemical in nature. Because we’re taking lots of different materials interacting, and they do tend to cause corrosion problems, and we have other fatigue issues. Actually materials and chemistry is an important part of understanding how your wiring performs.
John Gilroy: In recent years there have been some new wire standards released to reduce the likelihood of situations like the Red Plague. A lot of research done at AFRL and the University of Dayton. Could you expand on that a little bit please?
George Slenski: Sure. One of the committees we have to deal with wiring is the SAE Wiring Committees. In that committee, OEM’s come together, and government, and vendors, and we all talk about wiring problems. This whole Red Plague issue is causing lots of issues with various aircraft. The Air Force launched a research program to understand what’s the cause of Red Plague? It’s one of these problems that comes back every five to ten years. People deal with it, it goes away. We actually work with the University of Dayton which is near Wright-Patterson, there in Dayton Ohio. They actually were able to pretty much effectively come up with a cause of Red Plague and come up with some mitigation strategies.
Once we got that down, we then developed some new specification standards where we can actually mitigate or stop the Red Plague process from causing issues in the future.
John Gilroy: Let’s not forget they’re the University of Dayton Flyers, aren’t they?
George Slenski: That’s correct…..yeah, a great basketball team.
John Gilroy: Right near the Air Force base there. You’ve been Chairman of a committee called the, “SAE 8A Wire Systems Insulation Committee”, for several years now. I guess this is a good place to discuss some of these topics?
George Slenski: Sure. AS50881 is our standard we use for designing and installing aircraft wiring in all types of systems. That specification, and it’s been around actually since the ’60’s, it’s a body of knowledge that we use that if you follow these procedures and the standard, you will have effectively installed a safe wiring, and will actually be certified from a military standpoint, and also on a commercial side, they use that for air worthiness compliance.
It’s a document we use in the military. It’s actual contractual. We’re always changing, updating this document all the time. A great example, just a few years ago the Navy side was having issues. A lot of times we use plastic tie wraps to hold the wires together. Those tie wraps were breaking, or sometimes they were too tight and they were gauging wires, and they were causing problems. We actually put a prohibition against using plastic tie wraps and went back to using lace board, which is a fiber material. A lot of people in the industry were not happy about that, but the military really felt they needed this change. Whenever we make changes, we actually impact the entire aerospace community.
John Gilroy: I think the aerospace community should know that you use the term, “We”, describing some of your activities. You work with organizations like NASA, the Air Force, and the Navy, so you’ve really got a good experience, good handle on these situations, don’t you?
George Slenski: Yeah. I used to work for the Air Force as a civilian when I retired. Then once I retired and formed a Consulting company, I also work now with NAVAIR, the Navy Aviation branch at Pax River. I still work for the Air Force, and I also work for NASA, where I did a lot of work on the shuttle when it was operational. Now I help out NASA when they have wiring issues or electrical materials issues in their space craft, and also on some of the ground systems.
Did You Know? Lectromec’s EWIS component test lab is an ISO 17025:2005 certified facility. Lectromec has a wide range of wire and cable testing services.
It’s been a great career. I just love working on space projects with NASA. Again, we always seem to come back to wiring and connectors, and they cause a lot of our problems.
John Gilroy: That’s interesting to know. This is a topic that I think listeners may be interested in. One of the recent recommendations is not to spray CPCs or Corrosion Preventing Compounds in connectors around wiring. Why is that?
George Slenski: CPCs or Corrosion Preventative Compounds as you mentioned, are used to actually suppress corrosion. By putting an oil material on the surfaces of a structure, you can actually slow down corrosion. The problem is when that gets on our wiring components, it causes degradation to some of the wiring materials. One of the problems is the PS’s are flammable, so we spend a great deal of money trying to create this inflammable wire that if there’s arcing, or it’s on fire, it won’t propagate, but if you spray CPCs in the wiring, and then you introduce a flame, it will actually propagate down the wire and destroy a large amount of the wiring. We’re actually saying we don’t want people to spray the CPCs on the wiring, or if you do, you have to remove it.
That was a prohibition again we included in the 50881 document. Again, it’s somewhat controversial. Some people don’t see it as an issue, others see it as a big problem. That’s one that when we come together as a body where we make the decisions, we have a lot of discussion. We get the wording down properly, and then we introduce these changes.
Overall I think it’s going to give us a more reliable aircraft, and also better performing wiring. These are things that we learn about over time, so again, it’s this body of knowledge that’s out there. It really helps designers and those who are working on aircraft really create high reliability systems.
John Gilroy: Yesterday was Father’s Day. I spent some time with my son Kevie and I was telling him about unintended consequences. Sometimes you have the best intention and bad things happen. I think this might be the situation with the CPCs. They didn’t intentionally spray them on there figuring there would be problems in the future. They’re trying to—of course—reduce corrosion, hmm?
George Slenski: That’s correct. You’ve got the corrosion people who want to spray everything, and you’ve got the wiring people that say, “We don’t want you to spray our wiring components.” These two communities have to come together. They have to understand each other’s issues, and then come to some type of compromise or solution, and that’s where we are right now.
John Gilroy: One challenge I think in the era of aircraft, is that high voltage energy power distribution systems seem to be on the rise here. Does that impact your work at all?
George Slenski: That’s definitely been an issue recently. We’re increasing the voltage in aircraft. We’re using much more power, more current going through the wires because of all this avionics that we’re introducing. It’s the all-electric aircraft concept.
Many years ago we had to have pulleys that moved around flight control services. Then we went to hydraulic systems. Now we use electric actuators that actually move all the control surfaces in an aircraft. That means you have to have lots of current, lots of wiring on these aircraft available.
In order to reduce the weight, they like to increase the voltage, which reduced your current because it’s basically it’s really power. Voltage times current gives you power, so I increase my voltage I can actually reduce my current, and I get the same amount of power going through the wire. Which means now I’m using a smaller diameter wire to get the same amount of power going down a lengthen of wire.
Because of this though, there’s a lot of energy now in these wires. If something does chafe or arcs, it can propagate very quickly and cause a lot of damage to the aircraft structure and take out many electrical systems. We just have to really understand arcing and propagation failures on these new high energy, high voltage power systems we’re introducing into the aircraft.
John Gilroy: At Lectromec here, we like to bring in engineering interns. We had an intern here a while back, and she wrote a blog post on carbon nanotubes. I guess you’re in college, you’re interested in the brand new things. Some people say this could be a solution down the road for some of these problems.
George Slenski: Yeah. It’s a really interesting technology. The carbon nanotube, the concept there, it’s a single atom of carbon that forms a tube. Because the dimensions are so small, you almost get zero resistance going through these tubes, and they’re very strong. In fact, when you bring these tubes together, then you can actually create a fiber. You can actually create a fiber that’s the size of a wire that’s actually stronger than steel.
The conductivity has not reached the level that we want because you have all these small nanotubes which are interactive with each other and it creates contact resistance. One of the things we’re trying to do, is optimize the nanotubes and bring the manufacturing costs down because they’re about the tenth of the weight of copper, and they’re also very flexible.
One of our big problems in aircraft is breakage of wire. If you have this textile product you can bend easily, you’ve now eliminated another reliability problem you have with wire.
John Gilroy: That’s amazing. In the basic physics courses I took years ago, I never conceived of zero resistance. It seems like my teacher would have thrown me out the window if I’d said something like that. We’re getting there, huh?
George Slenski: It’s a slow process, a lot of research. It’s going to take time. We’ll never get down to zero resistance just because of the losses and the materials. When you scale them up it’s a macro size. Ideally we’re going to get close to copper, and then we will increase flexibility, but it’s really weight. On aircraft, everything’s all about reducing your volume and reducing your weight.
John Gilroy: Anything that can help achieve that, that would be great. Where do you see the industry heading in the next five to ten years?
George Slenski: I think this whole concept that we’re trying to integrate the electrical systems more. We’re trying to basically find ways to increase the reliability of systems because wiring in the past was always a “Install it, forget about it.” It’s one of the last things you put on an aircraft. It’s really becoming now a critical system on the aircraft. We have to find new ways, new materials that have increased reliability.
Also a lot of our problems are from maintenance. When they go into aircraft maintenance activities, they open avionics phase, they end up damaging the wiring. One of the things we’re trying to do, this is really cool about nanotubes, we could actually embed the tubes in the structure of composite aircraft.
Basically the wiring would be protected in the composite structure. It would actually go down the length of the structure itself. If we have enough of these nanotubes in there, we could actually reconfigure the system depending on the mission.
John Gilroy: For an undergraduate studying Engineering, that would be a pretty exciting concept I would think.
George Slenski: Yeah. These are the five, ten years, twenty year concepts we’re looking at right now. It’s amazing when you get enough people working on it and you have the focus on some area like this, you can really advance the technologies.
If you open up any research magazines you’ll see nanotubes talked about. It’s the technology, a lot of money is invested in this right now. It may be five to ten years, hopefully. Actually, we’re already flying nanotube wiring on some space craft already.
John Gilroy: Wow!
George Slenski: The cost is still very expensive, so we haven’t got to the aircraft level. I think within five to ten years, you will see quite a bit of nanotube materials on aircraft for wiring and distribution of the signals, and hopefully someday, power.
John Gilroy: Wow, that’s great! We spent about eighteen minutes talking about aerospace. I’ve got to ask you an up close and personal question that touched on aerospace a little bit.
George tell me, in the last twelve months how many miles have you flown? There’s a question for you.
George Slenski: Well, let’s see. I would have to think about the number of mileage. I think it’s probably around twenty thousand miles. Not very much, really.
John Gilroy: That’s a lot from my perspective. Wow, that’s a …
George Slenski: All of us at some point in time, fly on aircraft. We always expect them to work and get us places on time. You’re right, the fact we work on the technology. We rely on the technology also.
John Gilroy: Yeah, it’s like, “I own the company. I’m a client too.” “Hey, I’m sitting on this airplane, and I’m making sure it’s safe.” Well great. Thank you very much for your time this morning, George.
George Slenski: All right, I appreciate it.
John Gilroy: Thank you for listening to the Lectromec Podcast. If you would like to learn more about aerospace wiring, please visit our website at lectromec.com. We have free white papers, 144 blogs, and much more.