Wire selection for a particular application can be a time consuming process. Selection of the right wire for the particular application to maintain device reliability and prevent a potential catastrophic failure (in the case of signal quality degradation or electrical arcing for power wires) can be difficult.In the aerospace industry, this is rather simple: there are accepted wire test standards and four to six different types of basic wires that are commonly used in insulation. What about other industries? The following guide is designed to help in the wire selection and evaluation process, which can be of particular use if there is not enough data to make a determination as to which wire specification should be selected (as there often is not).
Determine a list of needs
You may be starting a new project or the current wire being used does not meet your needs. In either case, start determining the operation and storage conditions. You can start by creating a list of questions to determine performance characteristics:
- Mechanical strain: How much flexing will occur during operation?
- Thermal Cycling: Is the operation/storage temperature cyclical?
- Fluid Exposure: What fluids will the wire be exposed to during operation?
- Voltage: What is the operation voltage?
- Endurance: What is the minimum longevity?
- Other Stressors: Are there other environmental or operational characteristics such as exposure to direct sunlight, cleaning, chaffing, etc that your wire is exposed to?
After a list of questions has been created, prioritize it. This will help direct subsequent testing and the final wire selection.
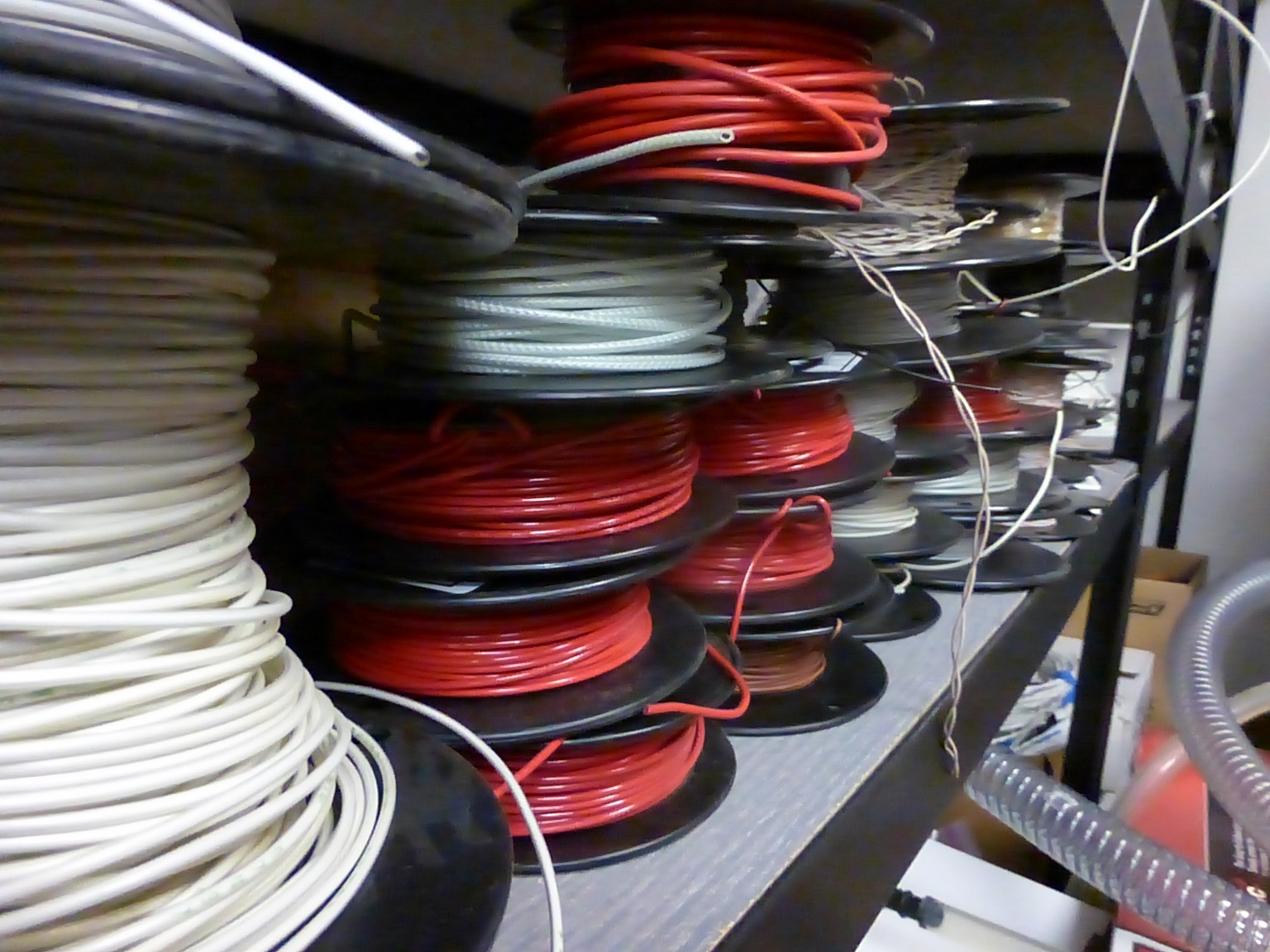
Do the research
Contact wire distributors, look for insulation information from chemical producers, and/or seek out experts in the field. There are a lot of products on the market, so start by looking for products specifically designed for your field.
Pare Down the Selection
Published materials are often sparse on details of wire performance on specific characteristics (thermal stability, cold bending, etc.). That’s because, generally these tests are not performed for non-aerospace applications. If you are working with a lab, they should have some experience with at least some of the materials. Find out if they have recommendations.
Test Selection
After the wires have been selected, the next step is to determine what tests should be performed. As there are hundreds of wire test standards, it can be very time consuming to determine which test should be performed (and to which specification they should be performed to). If you are not familiar with wire testing, this step should be performed in coordination with someone familiar with wire systems and/or wire testing.
As for the testing itself, the selection criteria should include:
- Measureable results: Many tests have pass/fail criteria, and sometimes they are necessary (e.g. plating adhesion). However, if you are looking to compare wire constructions, it is important to select tests that are not simply pass/fail tests.
- Assess performance in the determined environmental conditions
- Go beyond the test specs: The test specs often assess one property of the material.
- Longevity: If there is a desired use interval, the longevity tests will look to assess the wire performance over the course of repeated exposure cycles.
Test Performance
Depending on the type and quantity of testing, the test analysis can take as little as three weeks. However, if testing includes multiple samples taken through life cycles, the testing phase will take longer.
Also, depending on the selection criteria and tests performed, consider a dynamic test plan. If there are critical criteria that must be met (e.g. must maintain insulation integrity at a given temperature), set these as the first tests performed. Those samples that pass are then used in the other determined tests. This technique can help eliminate some wire candidates.
If you are interested in wire selection, you may want to read Lectromec’s 7-Step Process for Aircraft Wire Size and Circuit Protection Selection article.
Review and Selection
It is likely that there are wires that will perform poorly in all categories. Use the original prioritized list for performance characteristics (see above) to aid in the selection process.
However, if no samples perform adequately, there are three options:
- Redefine the desired performance characteristics (e.g. consider whether operation temperature can be reduced)
- Examine additional harness protection schemes (e.g. better chafe protection can be achieved through harness sleeve products)
- Look for alternative wire insulations