Principles of Aircraft Wiring System Safety
System safety supports risk management with the ultimate goal of optimizing safety on aircraft systems. Risk management is a vital aspect of system development that takes effect during the design phase; however it also remains important during the implementation and sustainment phases of an aircraft lifecycle. Optimizing safety is implemented through risk identification as well as implementing proper designs and/or procedures to mitigate risk.
According to FAA’s System Safety Handbook, system safety is a “balanced program [that attempts] to optimize safety, performance, and cost.” This is a challenging balance to achieve when designing any system because too much emphasis on one factor can lead to sacrificing another vital factor, which can then cause an unbalance. However system safety is interdependent with performance and cost through defining acceptable risk tolerances that can satisfy cost and performance requirements. The graph below illustrates the tradeoff between system safety and cost, schedule and performance. As the safety effort increases, the cost on optimizing safety should also increase while the probability of a hazardous event decreases.
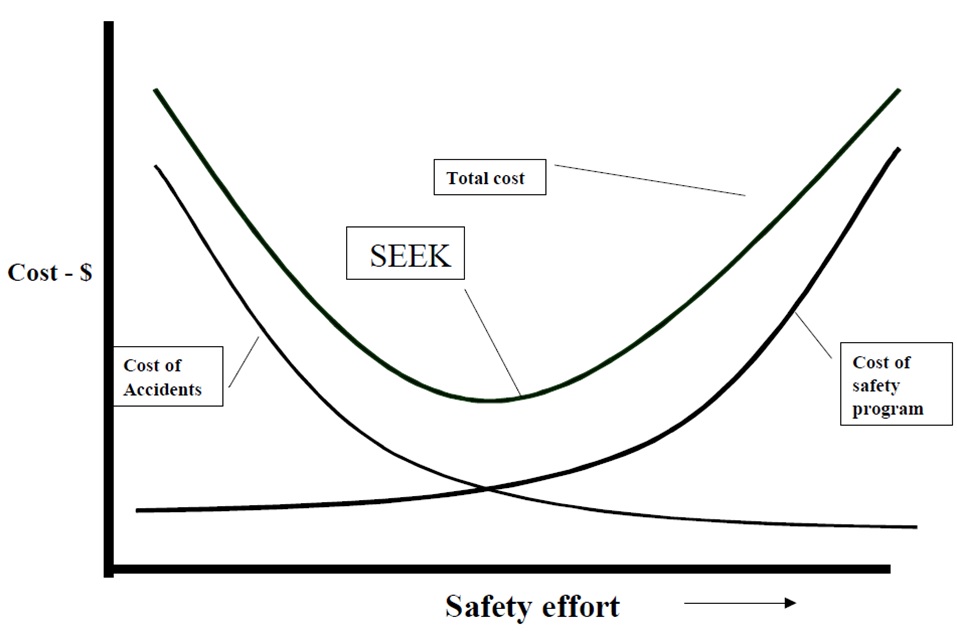
When applying the principle illustrated in the graph to EWIS, the following factors impact systems safety: weight, volume, and cost. For instance, interference can occur when a system signal wire is routed in a harness near another component that produces Electromagnetic Interference (EMI). The following options can be considered for optimizing safety and decreasing the likelihood of system interference.
- Redesign harness routing: This can be a possible solution to reduce EMI interference. However it may lead to susceptibility to EMI generated by other components.
- Increase shielding of wire/cable: This would either add weight and volume (using a double shield cable option) or cost (using advanced shielding option like a Carbon Nanotube shield). This will also increase the installation complexity.
- Apply shielding to the harness: This will add weight, volume, and cost, and may make repair of the system harness difficult while in service.
- Component redesign: Redesign the EMI producing component to make it produce less EMI.This would likely cause a delay for implementation.
- Modify the system to be more fault tolerant: Modify the hardware/software of the system to handle lower data fidelity. Similar to #4, this would likely cause a delay for implementation.
From a system safety perspective, each of the five options will achieve the desired airworthiness result, and therefore it is necessary to evaluate other factors. Each viable option would have their merit depending on what part of the lifecycle the issue was discovered. If the issue was discovered early in the design, then component redesign (#4) may be a viable option as the generated EMI will likely impact other systems and could lead to the lowest weight and most cost effective way to address the issue. If the issue was discovered while the aircraft was in-service, then wrapping the harness with shielded harness sleeving (#3), might be the most cost effective way to address the issue until the next D-check when the system wire can be replaced (#2).
RISK CLASSIFICATIONS: ACCORDING TO THE FAA
Risk is characterized by the severity of the hazard and likelihood of occurrence (this is similar to MIL-STD-882).
According to the FAA, severity can be categorized four ways
- Catastrophic (results in multiple fatalities and total system failure)
- Critical (results in serious injuries to multiple people and partial system failure that significantly reduces the safety of the aircraft)
- Marginal (results in discomfort to multiple occupants on an aircraft and minor systems damage)
- Negligible (Has no effect on safety)
Likelihood or probability is categorized into five categories
- Frequent (highly likely to occur)
- Probable (will occur several times)
- Occasional (will occur once or twice)
- Remote (unlikely to occur)
- Improbable (highly unlikely to occur)
A comparative safety assessment is a common method that can be performed to quantify the identified risks in a particular system. This tool allows identified risks to be categorized through their severity and likelihood of occurrence in order to prioritize and allocate money to prevent hazardous events. Tools like the Lectromec’s EWIS RAT can help with defining the risk to an aircraft’s EWIS.