The prevention of electrical fires is a common goal for most aircraft systems. Advisory Circular (AC) 25-16, “Electrical fault and Fire Prevention and Protection”, released in 1991, can be considered one of the precursors to the Electrical Wiring Interconnection System (EWIS) regulations. Although the document is now 25 years old as of last month, AC 25-16 provides a wide variety of recommended practices that are commonplace in the EWIS design and installation. Here we review some of the key points addressed in AC 25-16 and considerations with modern EWIS design with respect to electrical fault and fire prevention and protection.
Flammability
When FAA released Amendment 25-32 in May 1972, this added new requirements for aircraft EWIS flammability. Up until that time, aircraft wiring was not deemed as a necessary component for flammability testing. This was the regulation that required flammability testing for wire components. In effect, this was the regulation that ended the inclusion of PVC insulated wires, an insulation with a propensity to sustain fire, in aircraft.
In particular, the flammability requirement of wiring is clearly captured in the FAA EWIS regulation 25.1713-part C stating, “Insulation on electrical wire and electrical cable, and materials used to provide additional protection for the wire and cable, installed in any area of the airplane, must be self-extinguishing when tested in accordance with the applicable portions of Appendix F, part I, of 14 CFR part 25”
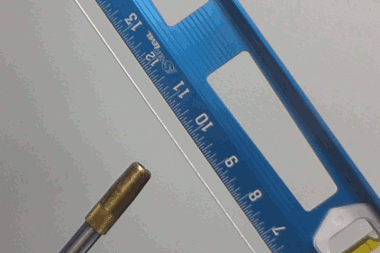
Hot Stamping
Among the practices that were recommended against in AC 25-16 include the practice of hot stamping. Hot stamping often caused damage to wire insulation and frequently found as a culprit in wire fires and electrical shorting. Although this practice is strongly discouraged, there is guidance available for those that choose to use this method of wire identification. Thankfully alternatives to hot stamping, such as UV marking, have proven their ease of use, maintaining the insulation integrity, and mark durability to common aircraft environmental and mechanical stresses.
Circuit Protection
The requirements on circuit protective devices became codified in FAA regulation 25.1717 on "Circuit Protection Devices". This regulation states, "Electrical wires and cables must be designed and installed so they are compatible with the circuit protection devices required by §25.1357, so that a fire or smoke hazard cannot be created under temporary or continuous fault conditions." The basic idea is the circuit protection should match the electrical load of the circuit, the wire gauge, and the ability to handle over-current conditions. This recommendation from AC 25-16 is partially included under the EWIS risk assessment requirements of FAA regulation 25.1709. As specified in the AC 25.1701, "The following factors must be considered when determining the separation distance [between wire harnesses and/or equipment]: … The maximum temperature generated by adjacent wire/wire bundles during normal and fault conditions."
Although standards like the AS50881 do provide ampacity guidance on handling steady state conditions for wire harnesses, transient or over-current conditions are not addressed. From a risk assessment perspective (such as showing compliance with 25.1709), one must consider the case where a properly electrical current derated wire harness in a high-temperature zone. Consider a scenario where the design pushed the limits of the wire temperature rating. In the application of this scenario, there is a 10C margin between maximum wire harness operational temperature and the maximum temperature rating of the components. Now, what would be the impact if two of the wires short together? There would be additional heat generated on both wires, which, because they are already near their maximum temperature rating, will easily exceed that temperature. The question is of course, what is the potential damage to the system? To ensure the safe design, factors like this must be considered.
Aged Recommendations
Although AC 25-16 is a good supporting reference document, some of the information included in the AC is out of date as would be expected with a 25-year-old document. An example of this is Paragraph D.4 which advises that, "wires having significantly different insulation hardness, or abrasion characteristics, should be routed in separate bundles" was found to not be necessary. The FAA-funded research in 2004 found that there was no appreciable difference in wire longevity if it were routed in a wire harness with the same or different wires.
Section d.5 of the AC focuses on the impact of insulation damage caused by "liquid spillage". Thankfully, most wires now must undergo fluid resistance testing before they can be considered for air vehicle installation. Although these fluid exposure tests identify different fluids, they typically include fuel, oils, hydraulic fluids, and cleaners (link to test).
This is an important factor to keep in mind when reviewing FAA recommendations. Many of the FAA advisory documents are written, forgotten, and rarely updated. It is therefore important to seek out modern recommendations for design, installation, and maintenance for not just EWIS, but any system that is covered by an AC.
Summary
AC 25-16 does provide a snapshot of how the FAA and the industry were beginning to consider the importance of EWIS, but does not tell the whole story about EWIS. The recommendations that are included in the AC show the understanding of wiring at the time and how much further the industry has come since the publication of the document. Flammability, circuit protection, and wire identification all have changed since 1991 and are continuing to evolve today. The concern with these advisory circulars is that, although they addressed some deficits in wire system design, it is important to work with those who understand the requirements and demands of modern EWIS design and certification.