The 2022 Interagency S&T Technical Meeting was held during the week of December 7th last year. Held at a wonderful and historic beach house at Kennedy space center, the meeting brought together some of the leaders in electrical systems for the next generation of air vehicles. Topics covered included batteries, alternative fuel systems, and Lectromec’s favorite: EWIS (Electrical Wiring Interconnect Systems).
First, a little bit of History
The location for last year’s S&T meeting was The Astronaut Beach House. When Kennedy space center was in development, NASA procured a neighborhood at the North end of the facility property. The homes from this property were all destroyed except for one, and there is no specific reason why this one house survived. As the years went on, astronauts would go here for a pre-launch celebration, and this can be identified with the cabinet filled with signed champagne and wine bottles on the property. Since that time, the beach house has become a meeting room and a bit of a historical landmark.
Now, a bit of history about the S&T meeting. The S&T meeting has its origins in the early 2000s when there was a lot of research across the US and the world into aircraft wiring systems. This research covered risk assessment, arc damage, life extension, wiring system assessments, improved protection devices, etc. It was realized that with all the government groups leading similar activities and finding similar outcomes from research, it would be beneficial to collaborate and coordinate the research dollars.
The divergence of the topics covered began around 2010 as the FAA’s research funding in the field began to dry up. The meeting soon took on other research areas in close proximity to the aircraft wiring systems including power controls, power distribution, and advanced circuit protection technologies. As those components advance, and as the industry moves towards greater electrification of air vehicles, the interests and the focus of the meeting continue to broaden to include energy storage devices and the associated technologies (batteries, fuel cells, etc.). The fact is: the developments of the systems and the knowledge base associated with them were necessary in order to better integrate and develop the next generation of aircraft wiring.
The following is a brief summation of some of the topics discussed at the meeting.
Topology of Upcoming Electrified Vehicles
With the use of electrical energy for propulsion applications, the definition of the aircraft electrical system, propulsion, and energy storage becomes a little bit more interesting than it was in the past. Historically, the fuel system has been separated from the electrical system. However, in modern systems, with the batteries and fuel cells supporting propulsion, is that now categorized as part of the electrical system, or is it still part of a separate energy storage system that would be analogous to the fuel system? This of course then leads to questions about the analogies between fuel lines and high voltage wiring and if that should be considered part of the energy storage system or still part of the aircraft EWIS.
This debate becomes more interesting when we look at hybrid electric vehicles. For these systems, traditional liquid hydrocarbon-based internal combustion engines are still used to drive the aircraft engine’s propulsion. Parallel to this is the internal combustion engine which is connected to a generator through a power distribution system (which may or may not include energy storage) that is connected to an electric motor and then connected to the same propulsion system as the internal combustion engine.
With this system, where does the boundary of the aircraft engine stop? From an FAA perspective, only three things are applicable for certification: aircraft, engines, and propellers. What part or parts of this hybrid system should be considered a part of the aircraft engine? Some guidance for this already exists and industry standards such as the ASTM.
This is an important distinction because it is not just semantics but rather a direct impact on what a producer can have certified by the FAA. Those with experience in the development of electric propulsion for aircraft have said that controlling the power input is just as important as controlling the design of the motor itself. The reason for this is that if the energy storage system is a battery or fuel cell, there are different properties and different responses to loading that can impact how the engine and flight control system respond.
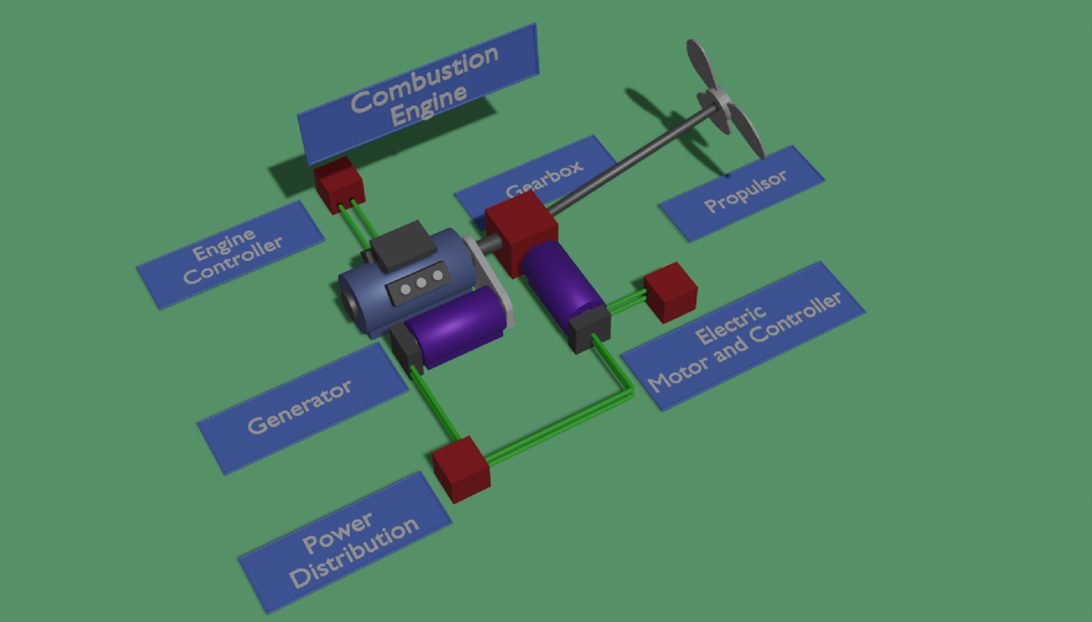
Energy Storage to Support the Electrification of Aircraft
Batteries are the energy storage solution of choice for most current electrical aircraft designs. While the energy storage within the systems is good and has allowed for the development of short-distance electrified aircraft, energy storage limitations mean that other fuel systems and energy storage technologies need to be implemented in order to address the objective of wide-body aircraft being electrified.
A presentation by EASA (European Union Aviation Safety Agency) showed some of the technologies and fuel systems being considered for the next generation of electric aircraft. Upcoming technologies for aerospace systems include fuel cells and hydrogen-powered aircraft. Each of these has its benefits and drawbacks and a number of technical challenges with implementation. With hydrogen, the material state of hydrogen impacts design; in particular, liquid hydrogen requires cryogenic temperatures meaning that the refrigeration system is not a flight-/safety-critical system. Fuel cells require complex systems for fuel storage and energy generation, and have to filter the incoming air to reduce fuel cell contamination.
Electrostatic Discharge on Connectors
An area of EWIS that has caught the attention of NASA is the resistivity of connectors and mitigation of electrostatic discharges. There are documented cases from rocket launches showing a buildup of surface charge on connectors eventually leading to electrical discharge and impacting the contained systems. In the case presented to the S&T group, the connectors were located on the skin of a rocket, and the static electricity buildup discharged into the circuits of the ethernet system resulting in glitches. In one case, the electrostatic discharge resulted in the inadvertent firing of an electro explosive.
From the assessment, NASA found that the resolution to this issue was either:
- Movement of the connector from the location
- Change of connector material to avoid static build-up
This is another example of knowing the installation environment of the equipment. If the system is potentially subject to lightning, triboelectric charging, and/or radiation flux consisting of energetic charged particles and sunlight, then additional work should be done on the selection and testing of EWIS components.
High Voltage Degradation.
The team from DuPont shared work being done on high-voltage polymers and the performance gains with their new materials. A couple of pieces of information that will be useful to those working with high-voltage equipment and high-voltage systems:
- The temperature impact on PDIV and PDEV is not independent of material type. Some materials are less prone to PDIV and PDEV degradation at higher temperatures.
- Research performed by DuPont examined the performance and life impact of frequency on material longevity under partial discharge conditions. When the researchers examined the longevity between a sample exposed to 20 kHz and one exposed to 60 Hertz, the 333 times increase in frequency meant a 436 times reduction in time to failure.
Some of the presented research shows new variations of the Kapton materials allow for higher density Litz wire constructions with the insulation taking up the less cross-sectional area of the Litz wire.
In the Next Month
Lectromec also presented at last year’s S&T meeting. This presentation, “Do we need HV EWIS specific regulations?” will be published on Lectromec’s website early in 2023. To be notified when this is available, sign up for the Lectromec newsletter.