All components wear out over time, but the rate at which they degrade will vary depending on the quality of the product, how is it handled, and the environmental conditions in which the component is installed. To consider all the potential ways that an EWIS can fail, it can be overwhelming. As a brief list let us consider the following:
Connectors | Wire |
Shell corrosion | Broken conductor |
Contact wear | Excessive mechanical flexing |
Contact corrosion | Fluid exposure |
Contact retention failure | Poor routing |
Dielectric breakdown | Overcurrent |
Fluid ingress | Tight bend weakening insulation |
Bend pin | Crushed by equipment |
Worn contacts | Abrasion during operation |
Contact- Wire Interface | Cut |
Corrosion | Poor shield termination |
Poor crimp/soldering | Noise on line |
Not sufficient contact area | Crosstalk |
Poor stripping of the wire | Generated EMI |
Improper sizing of wire with contact | |
Unmatched impedance | |
Unmatched metal type |
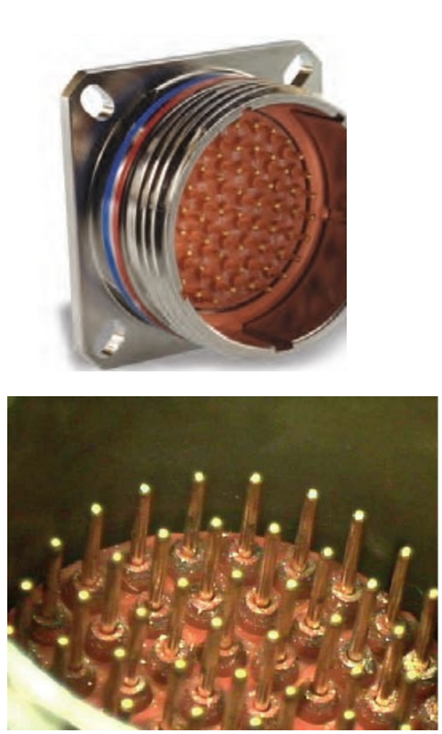
So how do you identify these and make sure you do not send off an aircraft with problems? The following runs through several of these potential failure modes, what they look like, and what can be done to address them
Contact Wear
Connector contacts are the terminations of pins and sockets for wires that are inserted into connectors. These contacts, which may be soldered or crimped, can have a variety of substrate materials plated with one of a couple of materials. When the contacts are mated, the pins and sockets rub against each other and progressively, wear down the plating. As more of the plating is worn down, the contact quality may be reduced, corrosion becomes more likely, and circuit performance is diminished.
Depending on the type of contacts that are used, they may be tested and have verified performance up to 500 mating/demating cycles before the contacts begin to wear. What does wear look like? Physically, the wear on contacts will dull the plating materials or exposure of the substrate. Depending on the environment, this may be exacerbated by environmental factors and cause corrosion.
There are a couple of ways that one might find this in an application. First, visual observation during maintenance actions. Without a doubt, this will be harder for higher density connectors (those with a greater number of contacts) and very difficult to observe on sockets. This means that all or most of the visual evidence will come from the visual examination of the pins.
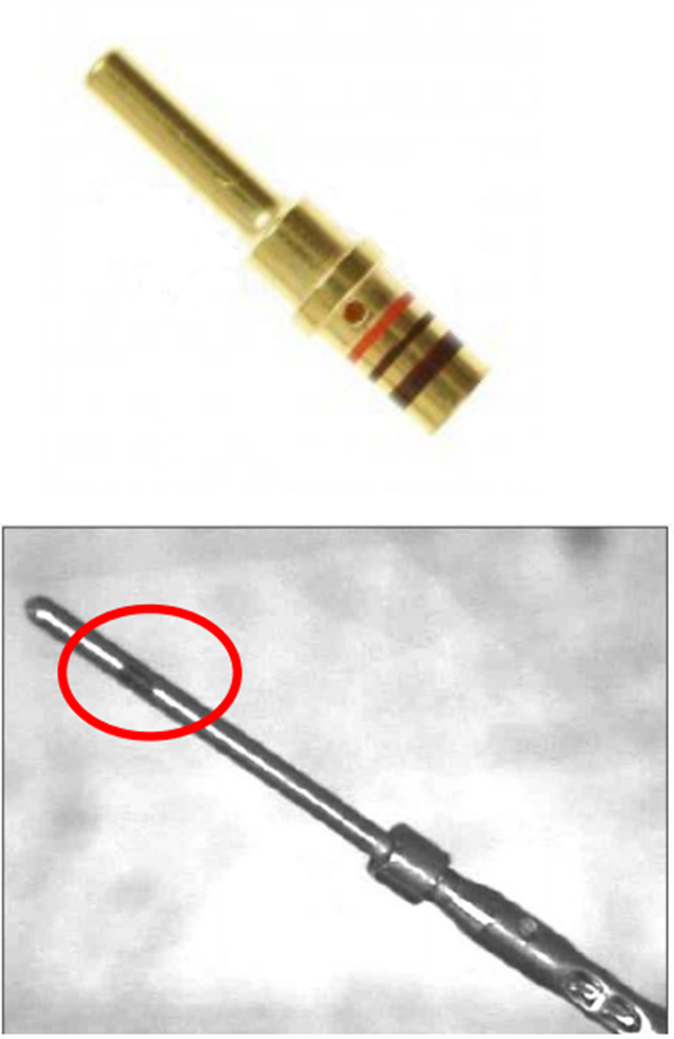
Note: The application of Corrosion Preventative Compounds (CPCs) into connectors is not recommended. While this may provide a short-term benefit, ultimately this will add contaminants into the connector and reduce circuit performance.
The other means of detecting contact wear is with higher than expected voltage drop or resistance in a circuit. Only after there is significant corrosion or wear is this detectable with a handheld multimeter. Systems like Time Domain Reflectometry (TDR), can help to identify the mismatched impedance. Further, testing the circuit with higher current loads (still within the wire and contact rating) can be used to identify corrosion in the circuit
Connector Corrosion
Connector corrosion can be amongst the easiest degradation methods to detect in an EWIS. The early stages of corrosion may not be obvious, but once it has taken hold it can rapidly expand on the connector. There are several means by which corrosion can initiate on a connector; physical damage, poor plating, contact with fluids that damage or erode the plating are among several possibilities.
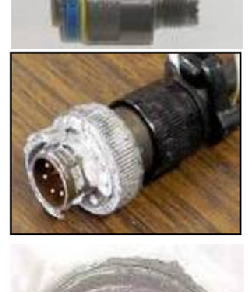
A question that is sometimes asked is if the surface of the connector is corroded but the mechanical strength is not compromised and the circuits are still fully functional, is it necessary to change the connector? The answer is dependent on the extent of corrosion. Connectors are designed to be disconnected, and if the corrosion extends to a point where demating may be impacted, then the connector should be replaced. Replacement is often the most effective solution as alternatives like cleaning and protecting will often not solve the underlying issue with the exposed connector substrate. Furthermore, if this is a repeat issue, then it may be necessary to approach the issue with a mitigation approach or design change mindset.
Upcoming Article
Future articles will address several other means of EWIS component failure. Having an issue with your EWIS? Lectromec’s testing, certification, and/or inspection services are ready to help.