Sometimes the design guidance that is a couple of decades old is still valid. The following flowchart is from the NASA Technical Memorandum 102179 – 1991.
The chart provides a flow for the design considerations for circuit protection, starting with determining the current need and ending with the implementation of the system. The 7 steps listed below discuss the flowchart in further detail.
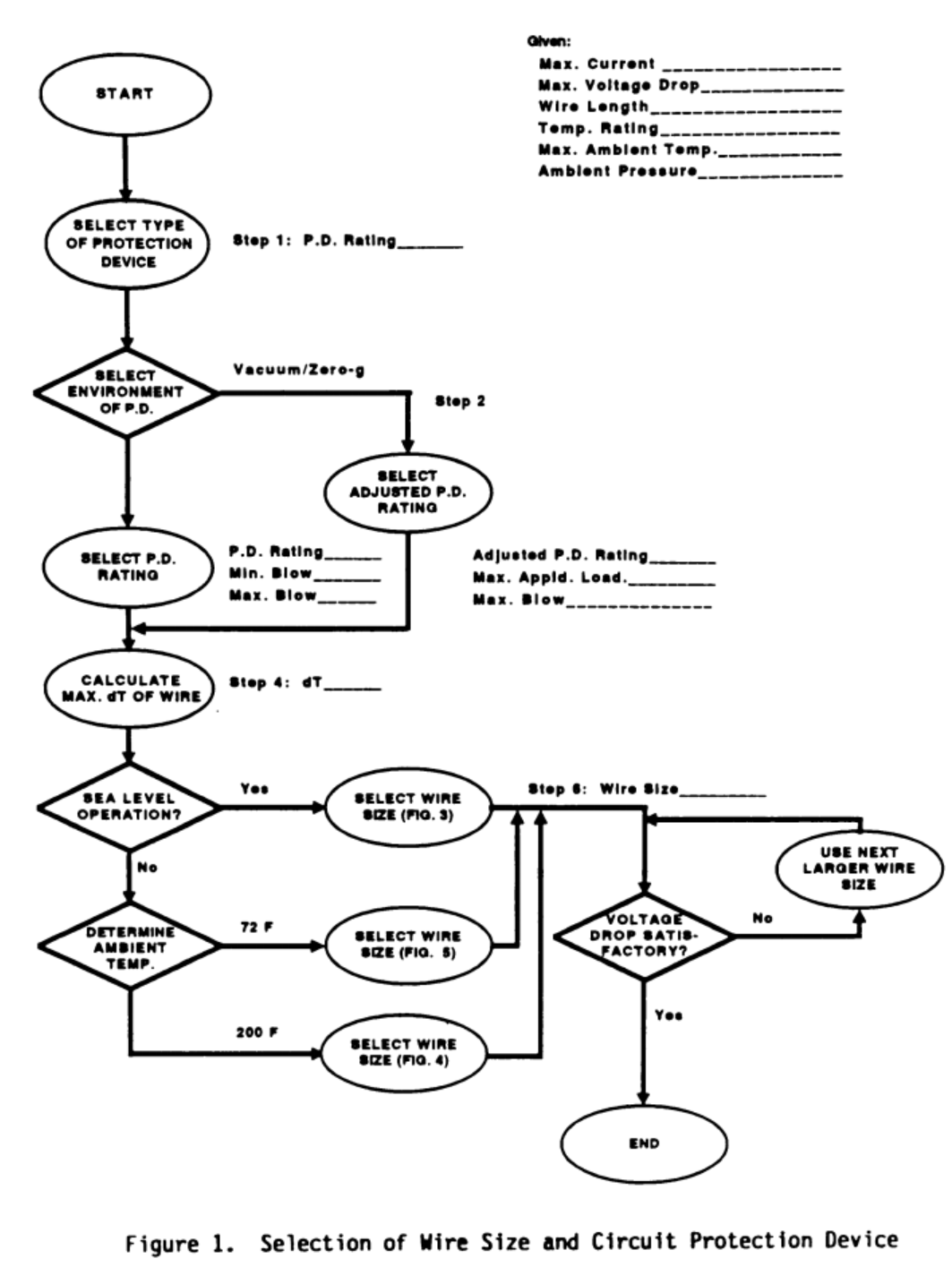
Step 1: Select type of protection device
This is when one of the following types of protection devices is being chosen: thermal circuit protection, fuse, arc fault protective device, or distributed power control unit. Each has its pros and cons (e.g. fuses have a faster trip time but are only good for a one time use), so it is necessary to understand the particular system’s needs before making a selection.
Step 2: Identify the operational environment
For the space application for which the flowchart was designed, the operational environment also included the consideration of vacuum and zero-g as it could impact the separation distance necessary to break a circuit. For those with a more terrestrial application, operational environment is still an important consideration. If the equipment operates in an uncontrolled environment or is a software controlled system, then its exposure to Electromagnetic Interference (EMI) or elevated temperatures should be considered.
Step 2a: Select the device rating
Without any modifying factors, determine the necessary current for the application. The information from FAA AC 43.13 is presented in the article Implications of Circuit Breakers and Wire Size for Wire Systems. Note that this rating information is based on maximum size circuit protection for a given wire gauge. This will provide a starting point for the wire/circuit protection size selection.
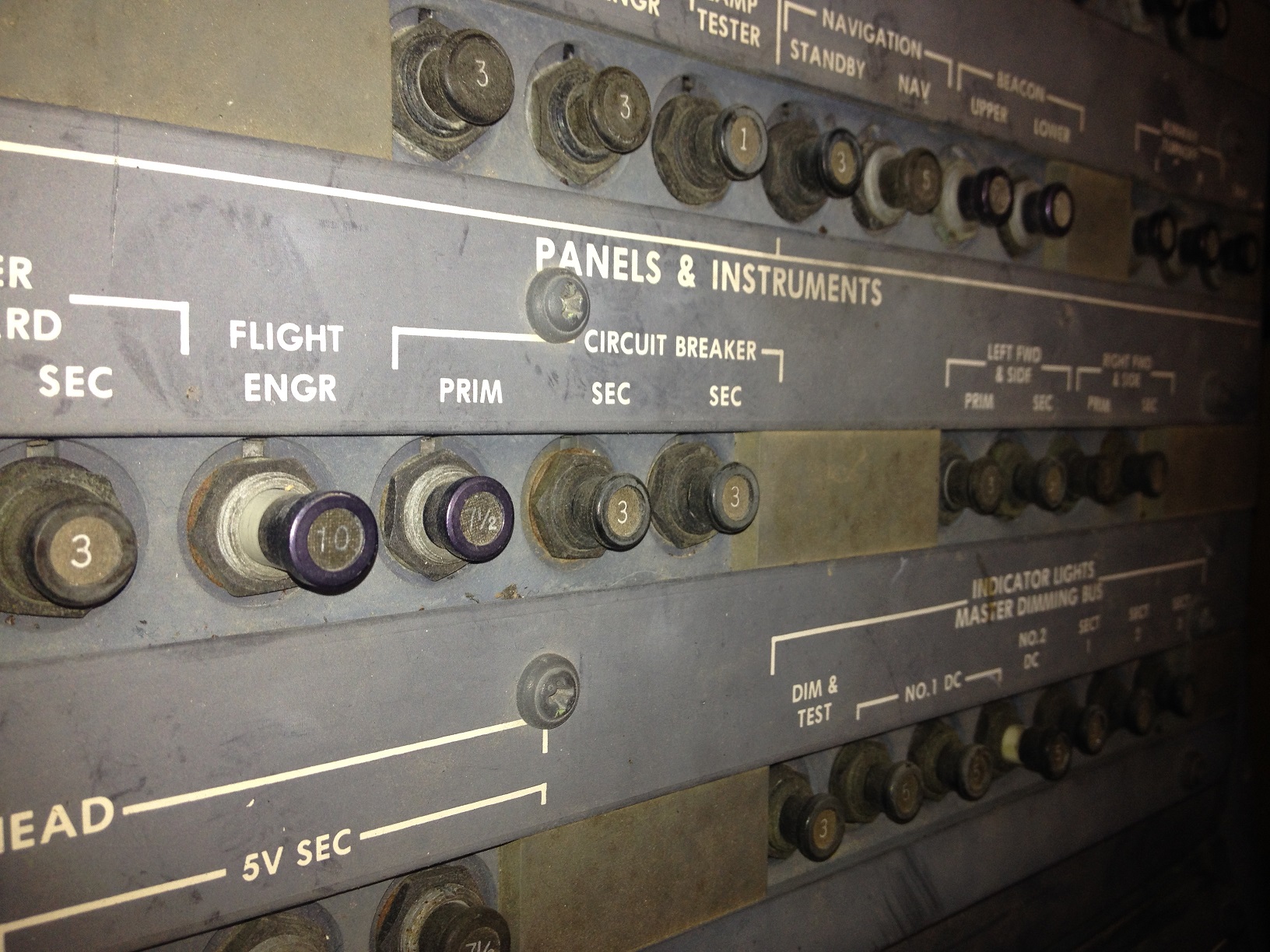
Step 2b: Select adjusted device rating
This adjusted device rating is based on the environmental considerations identified in Step #2. As discussed in the Lectromec Derating Tool Tutorial for EWIS article, the operational altitude impacts the given wire/harness current carrying capabilities.
Step 3: Determine device rating to use
Based on the selections made in 2a and 2b, determine which choice required the broadest operational environmental conditions; this may be a combination of both.
Step 4: Calculate the maximum difference/change in temperature (dT) for the wire
This is slightly mislabeled – it should say the maximum/minimum temperature of the wire/cable. The limiting factor may be the insulation or the conductor. Either way, it is important to know the operational range for the system. This step should also include the assessment of wire support equipment such as splices and connectors.
Step 5: Operational environment/Determine ambient temperature
This step could be combined with step 4, but it includes the evaluation of the zone’s ambient operational temperature. This zonal examination should also cover the nearby systems, equipment, and plumbing to determine if there are heat sources that may impact the wire temperature. The result from this step should be used to determine the current derating (as discussed in AS50881 and in the Lectromec Derating Tool Tutorial for EWIS article).
Step 6: Voltage drop assessment
The separation from the power bus to the powered device impacts the voltage seen by the end equipment. Smaller gauge wires (e.g. 24), have a resistance of 2.5 Ohms/100 ft.
In this step, it is recommended to determine the routed separation distance in the system and determine the voltage drop. Recommendations for determining these can be found in AS50881.
Step 7: Wire gauge increase
Based on the assessment results, it may be necessary to increase the wire gauge to achieve the necessary voltage drop and current carrying requirements of the system. If a new wire gauge/circuit protection pairing is selected, then return to Step #2 and repeat the exercise.
This process may seem overly complicated, but it is necessary to address the proper sizing of both the wire and the corresponding circuit breaker. Undersized wires may act as a heat source and/or reduce the attached device functionality. An oversized circuit protection may not protect the wire interconnection system and many not respond in fault conditions.