There are more than 17 parts to the FAA’s Electrical Wiring Interconnection System (EWIS) regulations enumerated in the 25.1700 series. To show compliance with each of these regulations require a thorough subject area understanding. More so, as the EWIS evolves in design, it becomes clear that achieving EWIS certification requires a lot of data. If an OEM is unprepared, this data gathering can take years longer than anticipated and delay certification schedules. This article provides an overview of technologies and services that Lectromec offers to achieve EWIS certification.
Components
As part of FAA regulation 25.1701, all of the parts of the EWIS must be qualified to the environment in which they operate and must be appropriate for the intended function. EWIS components designed to an accepted aerospace part standard (e.g. AS22759 wires, AS39029 contacts, A23190 clamps, etc.), are typically verified with a defined set of qualification tests. Lectromec’s ISO certified EWIS testing lab has many of the thermal, environmental, mechanical, electrical, and chemical test capabilities called for in these component standards. Our lab can provide the component evaluation that you may need for R&D, part qualification, third party assessment, or comparative testing.
Aerospace Vehicle Wiring Installation
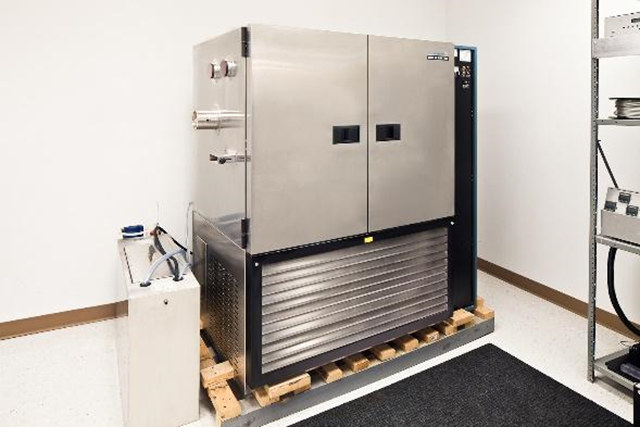
Lectromec recently published an article on the type of testing necessary for system level assessment. The article provides an overview of the testing necessary for AS50881 (which is a wiring system and installation standard) compliance. The AS50881 is often seen as a military aircraft wiring installation document, but this is one of the standards that is specifically called out in the FAA AC 25.1701-1. As with any aircraft design, there will be deviations for commercial aircraft. The important factor is that each deviation is marked, understood, and documented as to why this deviation occurred. In doing so, compliance with many of the requirements of FAA 25.1703 can be shown.
Functional Performance
When wiring system faults occur, the likelihood of potential functional impacts on the aircraft must be below certain thresholds. While many of the standard risk assessment methods can be applied here, particular knowledge and tools for assessing the EWIS can provide a much more in-depth analysis. Lectromec’s EWIS RAT is a technology that helps to identify and provide recommendations on how to resolve potential function performance issues. The EWIS RAT, which can be integrated with existing design tools, can evaluate the EWIS and provide the analysis to determine EWIS risk. The EWS RAT generates detailed and summary reports necessary to understands an aircraft’s EWIS. With a focus toward certification, the EWIS RAT is of particular use in showing compliance with 25.1709.
Physical Damage
This is an area in which Lectromec has performed testing and research for the last three decades. To show compliance with 25.1707 and 25.1709, it is necessary so show that the damage created by arcing failure will not negatively impact the airworthiness of the aircraft. This does mean that wiring failure can occur and lead to an electrical arcing failure event, in fact, it must be expected. When the arc occurs, the nearby components and systems must be considered and evaluated to ensure that the arc damage impacts is limited. From a lab testing perspective, Lectromec is the world leader in arc damage assessment. To find out more about physical failure damage and considerations for certification, Lectromec has a seven-part series on this:
- Part I: Damage assessment for 25.1707
- Part II : EMI compliance in 25.1707
- Part III: Heavy Current Cables in 25.1707
- Part IV: Grounding and Power Separation
- Part V: Component Separation Guidance
- Part VI: Control Cable Separation
- Part VII: Heated Equipment Separation
Flammability
The flammability of electrical components must be assessed (FAA regulation 25.1713). Currently, there are several test methods for the assessment of component flammability (see this article on current aerospace flammability test standards and here for Lectromec flammability test capabilities). These methods for flammability assessment will typically include direct flame exposure with some variation, such as preconditioning with a radiant heat panel. Whatever the initiation method, the material/component must quickly extinguish the flame after the flame has been removed.
But resistance to ignition is more than just testing a component when exposed to fire. For the electrical components, smoke and fire are possible with circuit overheating. Circuit protection devices are the preferred means for protecting circuits from overheating (FAA regulation 25.1717). Lectromec’s lab can perform the testing necessary to show operational performance, and this can be used as seed data for more in-depth predictive modeling of wire harness ampacity.
Continued Airworthiness
EWIS components will degrade over time and the degradation will be accelerated with use, mechanical stresses, thermal cycling, and environmental exposure. Proving how the operation conditions impact the long term reliability of EWIS is necessary for aircraft certification. How this is done will vary from platform to platform, but identifying EWIS component reliability and maintenance inspection intervals are central to this certification requirement.
In combination with the EWIS RAT and Lectromec electrical component degradation models, it is possible to provide quality life-limit predictions and recommended maintenance intervals. This information can be used to show compliance with FAA 25.1729 and the EZAP requirements.
Summary
Lectromec has the tools, technology, credentials (ISO lab and On-staff EWIS DER), and knowledge to get your design through EWIS certification. To find out more about any of these options or to discuss which options fit best for your needs, follow the links provided or contact Lectromec.