Key Takeaways
- Installed EWIS should be able to be be inspected, tested, repaired, and, if necessary, replaced with a minimum of aircraft disassembly and without causing undue disturbance to the EWIS installation or to surrounding aircraft systems.
- Wiring and other EWIS components are vulnerable to potential damage during inspection and maintenance.
- Industry guidance exists to ensure both safety and accessibility for EWIS inpection and maintenance.
Wiring, like many other parts on an aircraft, should be blocked from access for much of its service life. It is only during maintenance, inspection, or repair that are panels removed, equipment uninstalled, and access ports opened to reveal the wiring. Even with all equipment and panels removed, certain locations of each aircraft can be difficult to access/inspect. To that end, this article reviews the regulatory requirements, industry standards, and practical factors that play into the accessibility of an aircraft’s EWIS.
Regulation
Perhaps the most logical starting point is to look at the regulations. The FAA regulation for EWIS Accessibility, § 25.1719, states:
“Access must be provided to allow inspection and replacement of any EWIS component as necessary for continued airworthiness.”
The wording of the EASA version of this regulation is almost identical:
“Means must be provided to allow for inspection of EWIS and the replacement of its components as necessary for continued airworthiness.”
Intent
The regulation’s intent is to ensure that the installed EWIS can be inspected, tested, repaired, and, if necessary, replaced with a minimum of aircraft disassembly and without causing undue disturbance to the EWIS installation or to surrounding aircraft systems. A common outcome of wiring maintenance is unintended damage due to contamination (introduction of FOD (Foreign Object Debris) into connectors, fluid contamination, the introduction of swarf and other FOD into wire bundles where it can cause wire/cable damage), chafing, and other types of damage.
Among the goals of these regulations is the aim to impact the EWIS design phase such that designers minimize the amount of aircraft disassembly required to perform tasks that require EWIS access. For example, the wiring inside conduit may incur damage from chafing against the sides of the conduit. If failure of wiring inside a conduit can lead to an unsafe condition, a means should be provided for inspection and, if necessary, replacement of those wires. Inspection may be by testing (such as insulation resistance, DVW (Dielectric Voltage Withstand), TDR (Time Domain Reflectometry), etc.) or other acceptable inspection techniques and should be included in the maintenance requirements with ICAs (Instructions for Continued Airworthiness).
It is important here to recognize the language of the regulation in that “access must be provided to allow for inspection and replacement…”. Ideally, replacement will not require days of equipment removal, but that determination is up to the designer (tools like the EWIS RAT (Risk Assessment Tool) can be used to determine the failure probability of a wire harness, system’s EWIS, etc.). Naturally, if a wire harness is in such an installation condition, the design should be robust to minimize the chances of degradation and damage (connectors rated for a high number of demate/mate cycles, additional physical protection on harnesses, robust clamps, etc.).
Levels of Inspection
From accessibility for inspection, the requirements for visual inspection are a good place to start; the guidance that was provided to support EZAP (Enhanced Zonal Analysis Procedure) helps to fill this gap. The GVI, or General visual inspection, is defined in AC 25-27A:
“A GVI is defined as a visual examination of an interior or exterior area, installation, or assembly to detect obvious damage, failure, or irregularity. This level of inspection is made from within touching distance of the inspected object unless otherwise specified. It is made under normally available lighting conditions such as daylight, hangar lighting, flashlight, or droplight and may require removal or opening of access panels or doors.
It may be necessary to use a mirror to improve visual access to all exposed surfaces in the inspection area. Stands, ladders, or platforms may be required to gain proximity to the area being checked.
It is expected that the area to be inspected is clean enough to minimize the possibility that accumulated dirt, grease, or other contaminants might hide unsatisfactory conditions that would otherwise be obvious.”
And a Detailed Visual Inspection (DET)
“DET is an intensive examination of a specific item, installation, or assembly to detect damage, failure, or irregularity. Available lighting is normally supplemented with a direct source of good lighting at an intensity considered appropriate. Inspection aids, such as mirrors, magnifying lenses, or other means, may be necessary. Surface cleaning and elaborate access procedures may be required. A DET can be more than just a visual inspection. It may include tactile assessment to check a component or assembly for tightness and security. Such an inspection may be needed to ensure the continued integrity of installations such as bonding jumpers, terminal connectors, etc.
A DET would be required when the developer of the EZAP determines that a GVI is inadequate to reliably detect anomalies or degradation of EWIS components.”
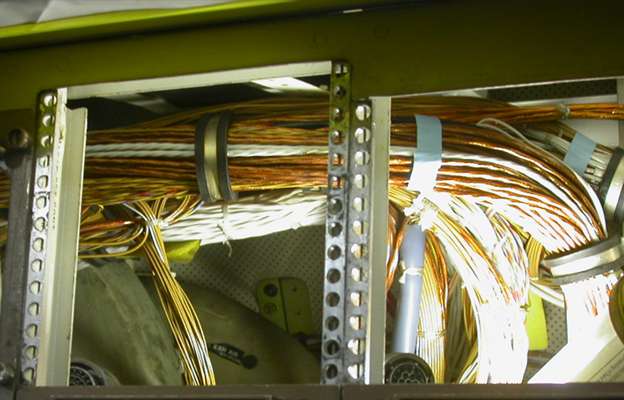
Wherever possible, designers should seek to make it possible for the aircraft EWIS to be inspected visually at the DET level, but practical limitations will inhibit this…and that can be acceptable. One item not discussed in the inspection levels is the system criticality which is a driver of inspection type used. Wiring for more critical systems will tend to require DET inspections. That said, if an area of an aircraft is less accessible, and it is at all possible, routing wiring with lower system criticality through these areas is recommended.
Alternatives to Visual Inspection
If visual inspection cannot be accomplished, then assessments must be done to determine the likely failure modes and if alternative condition assessment techniques will be sufficient. For example, the primary and redundant wiring to a system are installation locations precluding visual inspection. The following factors should be considered for these installations:
- What is the probability of failure of these circuits, and what is the probability of failure within the uninspectable areas?
- What are the physical failure consequences of each circuit?
- What are the functional failure consequences of each circuit?
- Is there the possibility of a single failure causing the loss of both circuits?
- Is a latent fault possible in the uninspectable areas?
- What changes to the system/installation would be necessary to support the non-visual inspection techniques (e.g., will it be necessary to have easy access to demate the connectors at both ends of the circuit and enough physical space to connect the connectors to automatic wire testing systems)?
Considering each of these questions should help to guide the frequency and type of inspection. The non-visual inspection types
Conclusion
Physical access to all parts of an aircraft’s wiring system is a non-trivial task that is necessary for compliance with regulations and requires attention to detail. While many of the issues may be identifiable within aircraft models, the final determination of what is inspectable cannot be made until an inspector is physically able to enter an aircraft and shine a flashlight on the wire bundles. There are specific requirements for general visual inspection (GVIs) and Detailed Visual Inspection (DETs), and they should be considered when reviewing a design.
To find out more about how Lectromec can help support your aircraft’s design and certification, contact us at any time.