Lectromec has written multiple articles on fuel system safety as it relates to SFAR88, AC 25.981, and AC 25.1701. In this article, we continue the discussion by reviewing some of the recommendations that came out of the NTSB report on TWA 800 and subsequently influenced AC 25.981. Some of these recommendations may not apply to those in the industry, but the design techniques should be reviewed and considered. This applies to any component in contact or in close proximity with the fuel system should be designed to prevent fuel tank ignition. Here we consider four elements within these documents.
Abrasion
A recommendation included within the Advisory Circular 25.981 is to protect the wires/cables from abrasion. The recommendation calls attention to fuel pump wiring stating a review to ensure that no wire contact the pump rotating group and result in, “energizing the rotor and causing arcing at the impeller/adapter interfaces”. In general, this has always been true for wiring. The design goal should be to maintain clearance and separation from any moving parts. Contact with moving parts can rapidly degrade the integrity of the wire insulation or any sort of secondary harness protection. Regardless of the secondary wire harness protection thickness and/or quality, they cannot protect indefinitely against abrasion. As was mentioned in the previous article but bears repeating, any parts that are protected with secondary chafe material should be reviewed on a regular basis and be included as part of any EZAP procedures.
Wiring Inside Fuel Tanks
The routing of wiring inside the fuel tanks has always been a difficult design choice. The obvious concern are potential consequences of wire insulation degradation and the release of electrical energy into the fuel tank. The common practice for wiring inside the fuel tanks has been to select PTFE-based wire insulations, although research has shown that other wire insulation types perform fairly well with extended exposure. Any wiring inside the fuel tanks should be clamped and protected in such a way that the chances for abrasion (and in the case of PTFE, cold flow) should be minimized. Further, as with other items of the wiring systems that are attached to or come in contact with the fuel system, fuel tank wiring should be part of regular maintenance inspections. As called out in AC25.981, the concern is that, chafing/wearing of Teflon sleeve and wire insulation can create scenarios, “allowing arcing through metallic conduits into fuel tanks”
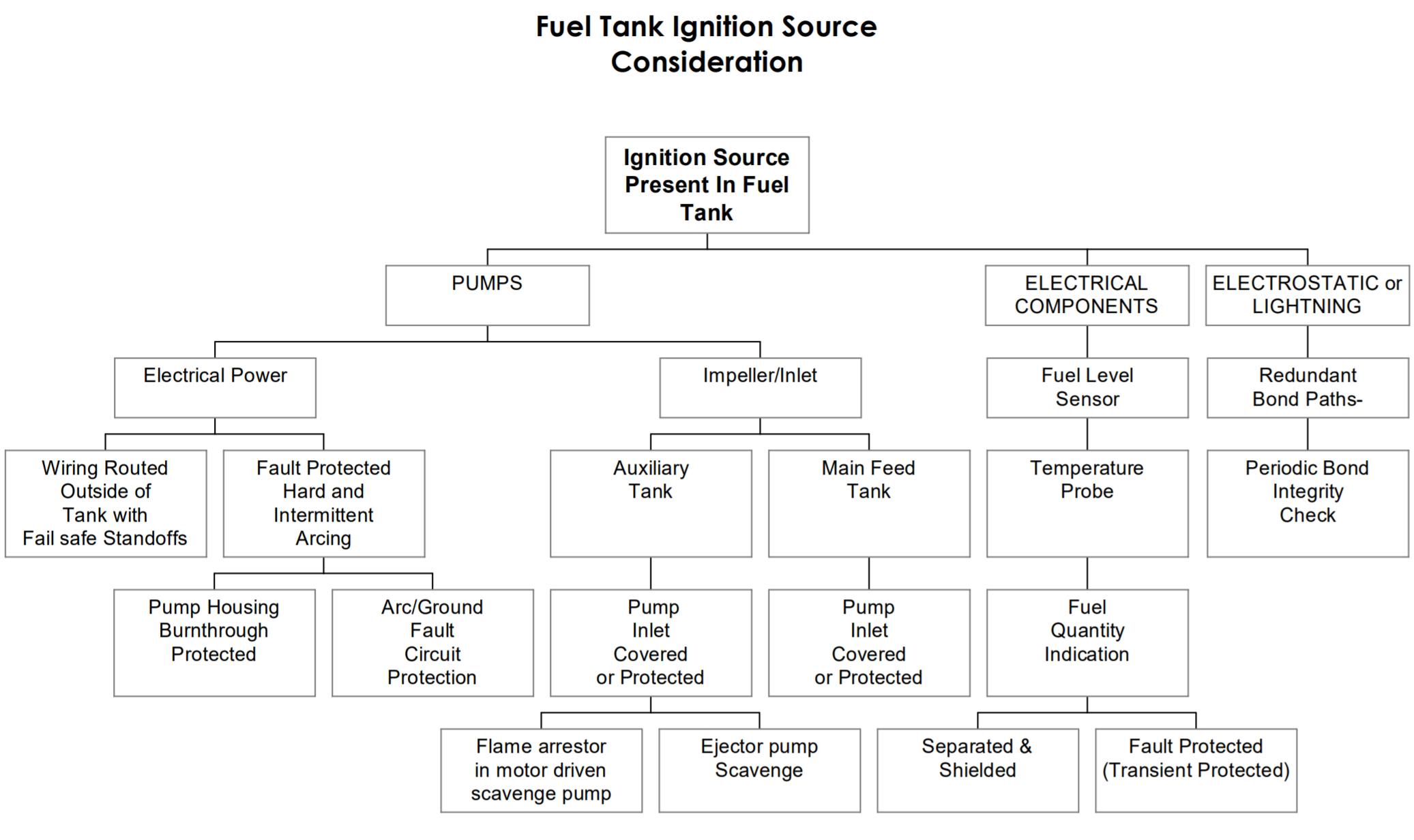
Standard Wiring Practices
AC25.981 also identifies that, “FQIS wiring that does not adhere to aircraft manufacturer’s standard wiring practices (i.e., wires bent back along themselves with bend radius less than defined in the aircraft manufacturer’s standard wiring practices, multiple splices lying next to one another, etc.).” Wiring inside fuel tanks or part of the fuel quantity indicator system is a critical aircraft component and must be treated accordingly. While a variety of design techniques and patterns can be used throughout the aircraft, strict attention to detail in manufacturing must be in place for the fuel system.
Safe Margin
The TWA 800 report states, “Section 25.981 currently requires that “a safe margin” exist between the temperature at any place inside a fuel tank where fuel ignition is possible and the lowest expected auto ignition temperature of the fuel in the fuel tank.” For some of the new aircraft designs, this becomes more difficult. It has been established that some new aircraft platforms use the fuel tank as a heatsink for the aircraft electrical equipment. Where traditionally there is an assumed temperature for the fuel that is close to the ambient temperature, new designs deviate from this. As such, the result is a reduction in the maximum total energy that can be discharged into the fuel tank. Previous articles by Lectromec have identified some of the challenges and safety factors that must be considered when wiring is routed near fuel tanks.
Protecting your Aircraft
Protection of your aircraft wiring system is obviously a common theme for Lectromec articles. But the importance of the design, maintenance, and regular inspection of wiring that is part of and/or near the fuel system cannot be stressed enough. Engineers and maintainers have done an excellent job in mitigating the risks posed by the combination of fuel and electrical power. We hope that this trend will continue and that the hard lessons learned about protection of the fuel system will not be lost. For support with you wire assessment needs, contact Lectromec.