Those familiar with aircraft wire system design know the limited available space in which wiring is usually routed. Often in tight quarters with other wire harnesses, redundant systems, and hydraulic lines, it can be very difficult and intimidating to identify safe separation distances in design and for retrofits. Adding to the complexity, a wire harness may have a different separation requirement from different component types.
With these considerations, a common question Lectromec receives when supporting Electrical Wiring Interconnection System (EWIS) Type Certification (TC) projects is, “What measures can be taken if a deviation occurs from the separation distance design?” Obviously, the problem is more often highlighted when the available space in the zone does not match what the testing or analysis has identified to be safe. This is the reason that the arc damage analysis testing designed by Lectromec covers multiple components and multiple paths. This article reviews Lectromec’s design evaluation process and how it can be used to improve EWIS design with the goal to increase the safety and reliability of an aircraft’s EWIS.
Assessment Process
The path to identifying if a separation distance design violation occurs can be summarized in the following workflow chart. First, we start with gathering the EWIS separation distances between the EWIS and other systems. This, for example, should look at the separation between the fuel system and the EWIS.
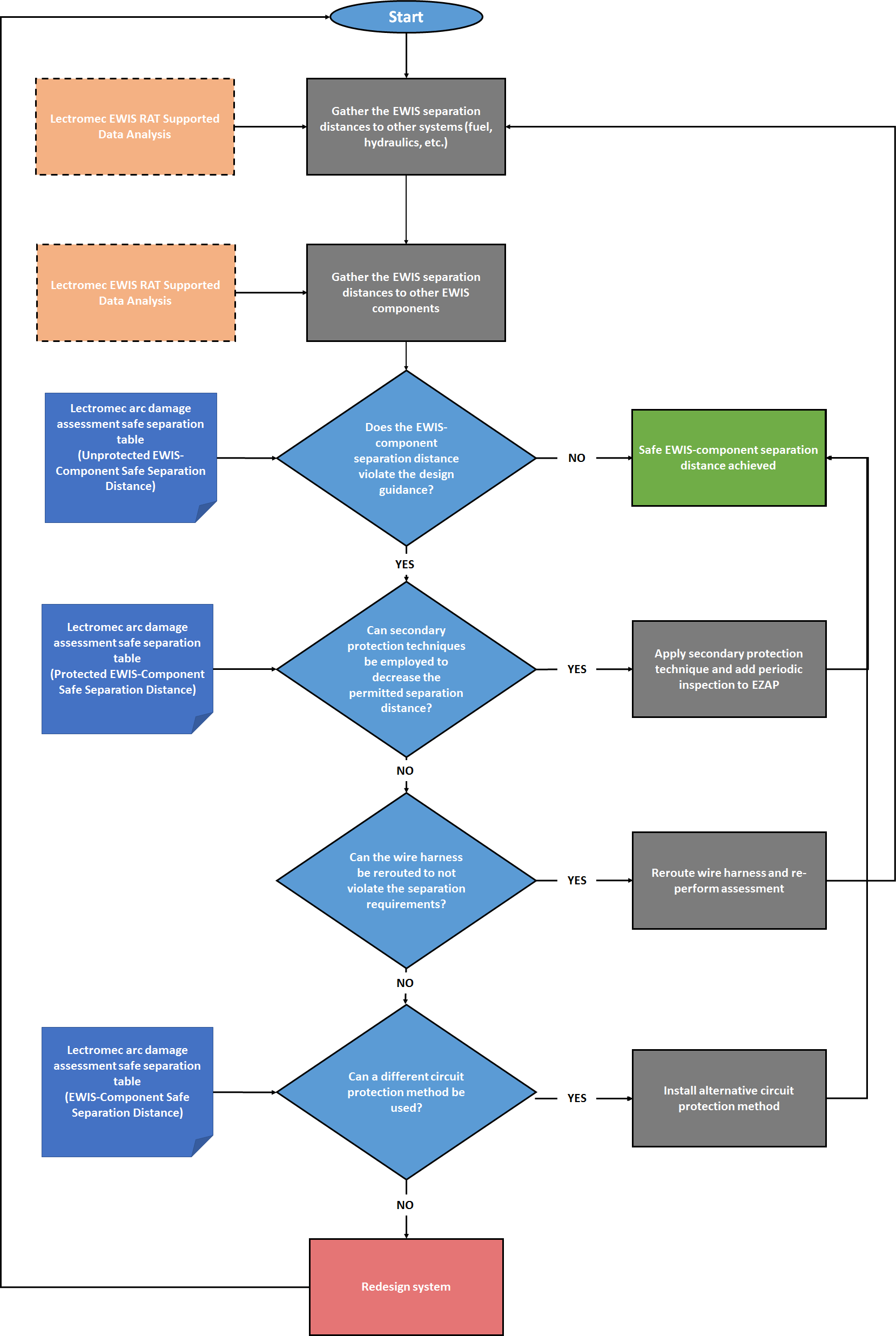
Next, the information on EWIS separation distance to other EWIS components (such as other wire harnesses) is gathered. Without more information on safe separation distances, it is a good rule of thumb to start the assessment of components within 6 inches.
The following four questions should be evaluated for every wire bundle section on the aircraft (a bundle section is a section of a wire harness in which no wires enter or leave, such as at breakouts).
Question #1: Does the EWIS-component separation distance violate the design guidance?
With your internal design guidance or with the arc damage separation distance that Lectromec’s testing and analysis will have created for your organization, a look-up table is generated and can rapidly identify reliably safe separation distances for various harness configurations. If the EWIS-component separation distance is not less than the safe separation distance, then the current design/installation configuration is acceptable. If not, proceed to question #2
Question #2: Can secondary protection techniques be employed to decrease the permitted separation distance?
Secondary harness protection materials (such as those conforming to SAE standard AS60491), may be a viable option for reducing separation distances. In some scenarios, secondary harness protection has been shown to reduce the necessary separation distance between an arcing wire harness and other components (this is not the case for all secondary harness protections). For this consideration, if a secondary harness protection material is added to the design, then there also becomes a need for a periodic inspection to be added to the Enhanced Zonal Analysis Procedures EZAP. If under further review it appears that the application of secondary protection material is not a viable option or is not preferred (given space and weight costs), then proceed to question #3.
Question #3: Can the wire harness be rerouted to not violate the separation requirements?
There are some areas within the aircraft that this is a more viable option than others, such as in a cargo area. High-density areas of the aircraft, such as the electrical equipment (EE) bay, may make rerouting of the harness more difficult. This question also covers the possible option where some wires from the harness are rerouted to reduce the total available electrical energy in the case of an arcing event. If the harness or some wire can be rerouted, then the design should be updated and the assessment re-performed to ensure no other design requirements are violated. If this cannot be done, then proceed to question #4.
Question #4: Can a different circuit protection method be used?
Perhaps part of the reason the separation distance requirement is so large is due to the type of circuit protection used. The use of technologies, such as Arc Fault Circuit Breakers (AFCBs) or solid state power controllers, can reduce the available energy in an arcing event. The integration of some of the circuit protection technologies is easier than others, and this should be part of the decision for implementation.
No viable options
If none of the options are viable, then this would suggest a circuit or system redesign is necessary.
Summary
The design of an acceptable configuration of an aircraft’s EWIS is not as simple as it once was. New performance and reliability requirements have pushed a need for more thorough EWIS analysis and with it, a need for greater validation of system configurations. There are systematic means of addressing the EWIS separation requirements, but to do this well, a good understanding of EWIS failure consequences is needed. To find out more about EWIS failure consequences or how Lectromec can assist with your EWIS type certification, contact Lectromec.