The days of ‘fit and forget’ EWIS are at least a decade behind, the aircraft industry’s understanding of the implications of wiring as a system continues to evolve. New aircraft have gone through EWIS evaluations to ensure that the EWIS complies to regulations – not an easy task. Obviously, as the OEM design choices remain in the field, the original knowledge that developed the routing, installation, and protection disappears, but what about aftermarket modification of the aircraft EWIS? Is it possible to take a new aircraft (or one that has been in service for 15 years) that has been originally certified to EWIS regulations and mark it compliant (i.e. keep a safe EWIS)?
Regulatory Guidance
Consider a new aircraft design: there is a lot of information that is necessary for the development of a safe EWIS (see this article on the areas that must covered as part of EWIS certification). However, when performing aftermarket modifications, is it possible to gather this information and not impact airworthiness?
As a starting point for those not familiar with EWIS requirements on new aircraft the following articles can be helpful to get started:
As a basis for answering this, we can go to the FAA guidance on the topic. Advisor Circular (AC) 25-1701
For those that are not intimately familiar with AC 25.1701, there is guidance on how to handle certification compliance with the regulations for both new aircraft designs and aircraft modifications. In terms of the EWIS assessment portion (25.1709) the modification of EWIS requires different handling. The guidance that is specifically laid out in the AC states:
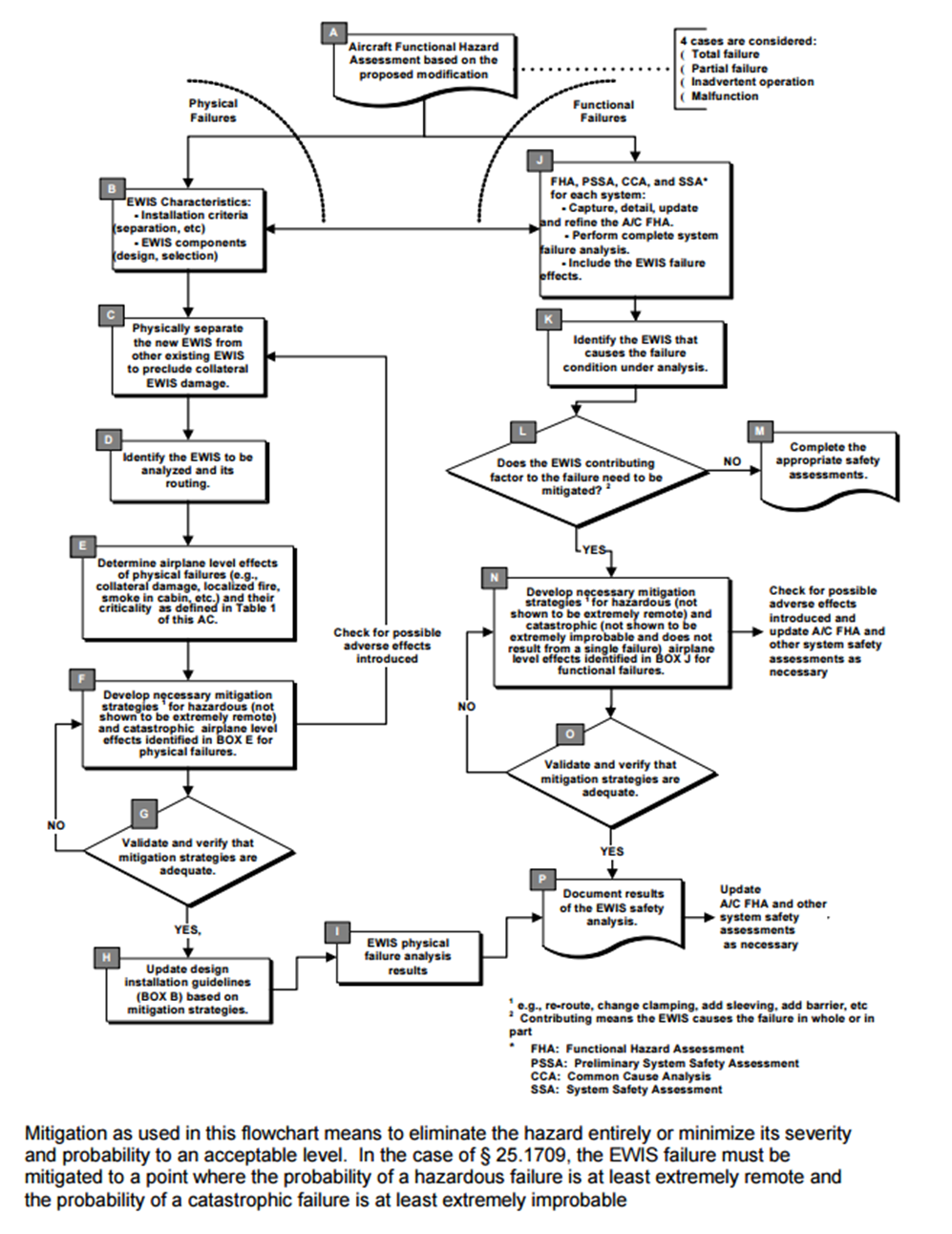
“Applicants for post-Type Certification modifications should use the analysis depicted in Flowchart 2 when the applicant cannot identify the systems or systems functions contained in existing aircraft EWIS that may be utilized as part of the modification. An applicant should not add EWIS to an existing EWIS if the systems or systems functions contained in the existing EWIS are unknown. To do so could introduce unacceptable hazards. For example, IFE power wires could inadvertently be routed with aircraft autoland EWIS.”
What does that mean for a modifier who needs to run wires in the aircraft? Either figure out everything in the wire harness (e.g. contained systems, failure tolerances, designed separation distances) into which the wires are to be added, or run the wire harness separately.
Trying to run the wiring separately can be a challenge when routing through lighting holes in structures where space is limited. Making the determination as to which course of action to take becomes a balance between the creation of additional feedthrough holes (which may weaken the structure) or joining the harnesses for the feedthrough then breakout afterwards. Depending on the systems involved and the potential risk of the additional wire, this may be acceptable for short lengths. Only configuration review and analysis can determine if this is acceptable.
A recent article from Lectromec covered some of the advancing technologies for EWIS design which include distributed power. These distributed power systems do provide ease for upgrades and modification to aircraft systems, but they do pose a whole new complexity for certification. In effect, using the distributed networks violate the AC’s guidance in that the new wiring is routed with existing systems. How this will be handled is not trivial and will require in-depth consideration and analysis.
Verify Changes, Verify Reliability
The modification of the EWIS should include a review from the maintenance perspective. Each aircraft should have an Enhanced Zonal Assessment Program (EZAP) as specified in AC 25-27A. The EZAP is designed such that there is a systematic approach to the aircraft wiring system review (something that the FAA felt was lacking in many maintenance programs). A full article on this has already been written and is available here. The basics of the EZAP are this:
- Define the zone boundaries
- List what is in the zone
- Determine the risk of fire, mechanical damage, or environmental factors that can impact EWIS reliability
- Determine the EWIS complexity in the zone
- Use the combination of factors in the last two to set regular inspection intervals As changes are made to the EWIS, the EZAP should be updated to account for new risk introduced to the system.
Achieve a Safe EWIS
A safe EWIS can be achieved, but it is not an easy task for a modifier. Some of the up and coming electrical system designs will make it easier for installation but may place additional challenges on the maintainer for certification. However, these changes and implemented, they must be created in such a way that they are able to be inspected and maintainable. If you have any questions about how to support your components, design, certification or sustainment of your fleet, contact Lectromec.