There are a number of considerations when designing the installation of EWIS on aircraft wire systems. They include part selection, system integration, routing, safety and separation, regulation considerations, operational environments, maintenance, and obsolesces planning. In other words, a lot to consider. Back in 2004, Lectromec released, Ten commandments of Wire Maintenance. Below, Lectromec lists, the 7 tenets of wire system installation:
1. Above all else, prevent chaffing
This is one of the largest drivers for EWIS maintenance. The methods for preventing chaffing include proper separation distance from other components (particularly corners and edges) and use of primary and secondary harness support to prevent a single point failure from causing problems. Identifying and reducing chaffing locations is a good starting point for maximizing EWIS reliability.
2. Harnesses are not handholds nor should they be used as support for personal equipment
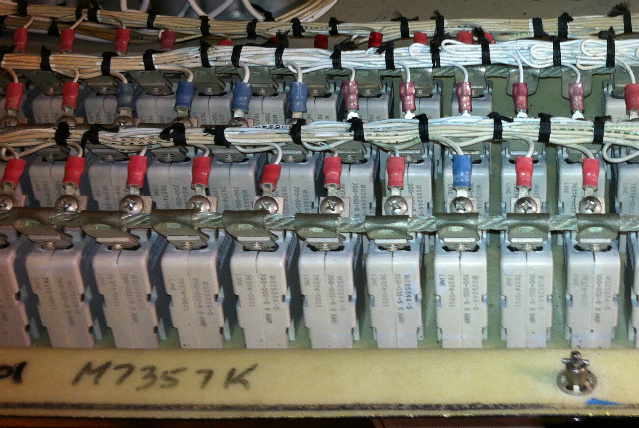
If a harness is in an area where maintenance is common, the harness should be covered and/or protected from human hands and equipment. Use of harnesses as grips and handholds, places strain on the harness and causes any number of problems including:
- Breaking the conductor
- Pulling the pin from the connector
- Misalignment of clamps
- Moving harnesses from identified critical clamp marker locations
3. Beyond handholds, keep harnesses away from humans
During normal operations, wiring should be routed and protected in such a way as to minimize the chance of accidental damage. This may mean that harnesses need to be routed in rigid conduits in some areas where other physical separation techniques are not available. There are obvious drawbacks to the use of conduits (e.g. difficult for maintenance to examine, concerns about chaffing at the ends, etc.), but they can provide the needed protection from personnel.
4. Moving parts are not your friend
Moving parts can pinch, crush, chafe, and cut wires. The moveable parts to consider include doors, landing gears, flight control surfaces, and mechanical cables. If the harnesses are routed nearby, it is necessary to maintain positive physical separation via standoffs or clamps. If the harnesses are attached to the moving component, it is necessary to include slack in the system and to design the flex points such that the harnesses are not pinched. Also, for all the parts of the mechanical movement range, consideration should be given to the minimum harness radius.
5. Hide from fluids
Electricity and fluids do not mix. Potential problems from exposure to fluids include:
- Degradation of insulation
- Shorting/arcing between damaged wires or wire to ground
- Shorting/arcing at connectors
- Contamination of connectors
It is important that the EWIS is protected along its length from exposure to fluids. These sources of fluids may come from leaking fuel or hydraulic lines, plumbing, or spillage from passengers/crew. If routed above these sources, the potential for exposure is limited. Where it is necessary to be routed below a potential fluid leak location, drip shields or umbrellas can be used to protect the wiring. Molded harnesses should be considered in areas that are regularly exposed to fluid and cannot be protected through other means. Additionally, addressing problems caused by fluids should include harness drip loops before connectors. This helps to prevent the ingress of fluids into the connector (see Lectromec’s In aerospace wire systems, how much slack should I give a wire? article for more information).
6. Hide from random physical damage
In areas of the aircraft where physical damage from debris is possible, such as in wheel wells, there needs to be a physical barrier for the EWIS components. The rocks and ice thrown into the wheel wells can damage unprotected EWIS.
7. Treat fiber optic cables carefully
When designing the installation of fiber optics cables, they should be routed in such a way as to prevent any loads (including stretching) on the cable or the terminations. Further, additional care should be taken to prevent flexing or crushing of the cable during the fabrication and installation process. This may require modification to procedures for shipping, storage, identification, and finally the installation/securing of the components in the aircraft. It should also be noted that additional support and routing considerations must be made for fiber optic cables. Ideally, fiber optic cables should be installed and routed such that movement is not necessary during the installation or removal of LRUs (Line Replaceable Units).
Again, this is to minimize stresses to the fiber optic cable and extend the component service life. An additional note from Dennis Jettun on Fiber Optics: “There have been occasions on the F-16 Optics FBO test program where cycling of the heat (hot-cold) caused the optics to age much faster in the sense of brittleness. This becomes a big issue with maintenance, not necessarily to the cable, but to equipment that may be nearby that requires loosening of a cable/bundle clamp to get to the component. If enough hot/cold cycles are seen by a fiber optic, it is most likely to crack if trying to be moved.” In other words, if you know you will never move the cable, then it is possible there will be no issues. However, if you must move a harness with a fiber optic cable, it is important to be prepared.
In summary
EWIS installation comes down to the following basic principles: keep it dry, keep it protected, and keep treating it nicely. Following each of these will minimize rollout problems for the aircraft and maximize service life.