Key Takeaways
- The verification and validation process is general enough to conform the various needs of the industry and interesting new design concepts, even the new high voltage wiring systems.
- The verification stage is the evaluation process where a product is assessed on whether it meets its specific goals or requirements during the developmental process.
- The validation stage of a product ensures that the product fulfills the needs and expectations that the developers intended it to meet at its completion.
Introduction
Amidst the manufacturing process, a structured system of quality assurance is of utmost importance; the implementation of a standardized evaluation system is key to ensuring that whatever is being made is up to par for its use case. In the world of technology and manufacturing, the evaluative journey of a product from start to finish is broken into multiple segments.
Verification
The verification stage in the development process is where a product is assessed on whether it meets its specific goals or requirements. Results of quantitative engineering examinations are appraised to ensure correctness and consistency with respect to the intended guidelines; in essence, it encompasses a series of checks along the product’s journey to ensure that progress is made and up to standard (internally or externally defined requirement).
In an aerospace setting, this would be the “ground testing” phase of the project; the active testing components such as communications, vibration testing, structural fatigue, thermal testing, and general pre-launch checks are used to verify the status such that all technical components perform well and the identified design risks are minimized.
Looking at this from the perspective of the Electrical Wiring Interconnection System (EWIS), this means developing project artifacts such as the installation guidelines, generating data to support system separation (EMI and arc damage), and component testing. This information guides the engineers and designers on the EWIS development often with the result of generating common build/install methods across an aircraft.
Validation
The validation stage of a product is the later step of the process, being the evaluating near completion of certain phases of what aspects have been developed correctly to various guidelines. This segment of the product’s genesis is that of ensuring it fulfills the needs and expectations that the developers intended it to meet at its completion. Validation testing is conducted under realistic conditions on the finished product to determine its efficacy and suitability upon deployment. For aircraft, this phase would include the in-flight testing such as thruster testing, weapons testing, controls, and general deployment of aircraft mechanisms.
FAA Guidance
These are not new concepts; they have been part of system design for decades. Standards like ISO 9000 have the V&V (Verification and Validation) concept built-in. For aerospace, the FAA has provided guidance to OEMs on how V&V should be included as part of product development; this is included in “The FAA and Industry Guide to Product Certification.”
The guide for aerospace development was established to:
- “a. Lay out the information in such a way that an Applicant can understand the basic expectations and best practices for achieving a successful product approval process.
- b. Provide experienced Applicants with guidance on how to move along the path toward a more systematic and mature process for product certification or approval.
- c. Provide all stakeholders, including FAA staff, with the knowledge of how to maximize the potential of the existing processes in conducting efficient certification processes while maintaining the systems’ health through risk based oversight through the use of the tools in this Guide.”
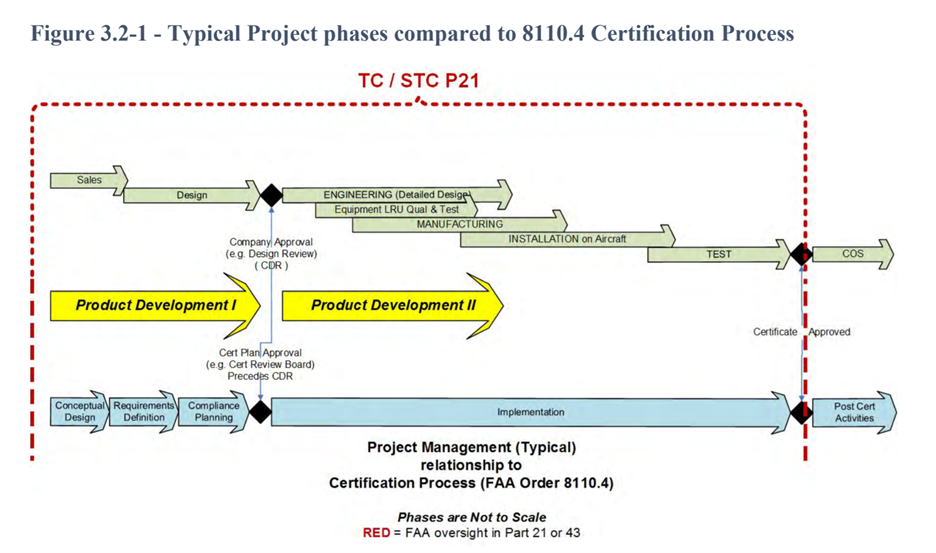
The FAA recognizes that there are significant variations in different stages of the product’s compliance maturity level based on its presently evaluated processes and capabilities. FAA oversight, therefore, varies in how they conduct their oversight responsibilities based on the stage of development the product is in.
Application to EWIS
When applied t0 EWIS, the V&V concepts are the same as they are for an entire vehicle. An EWIS centric example of where verification and validation is seen in the test case of physical separation of wiring from system components as related to CFR 25.1707. Here, it is outlined which tests are needed (the verification stage), specifically identifying the physical and electrical configurations to be used in the aircraft. This is done to ensure that data exists on wire configuration to determine the separation distance or to identify the tests that are necessary to fill the data gaps. The validation stage is present in the inclusion of design review and on-aircraft inspection.
Conclusion
The development of new and novel technology will be vital to follow a structured quality control process. The verification and validation process is general enough to thr conform the various needs of the industry and interesting new design concepts, even the new high voltage wiring systems.