Welcome to the Lectromec podcast with John Gilroy. The podcast that helps you improve your understanding of aircraft electrical systems. Every month we interview experts in the public and private sector to help you increase your knowledge of the design and maintenance of aerospace wire systems.
Today’s guest is Chris Teal, the Marketing Director from Eclypse International. Eclypse has been in business since 1988 and is based in Riverside, California. They are responsible for making electrical distribution analyzers for aircraft electrical systems. Essentially, Eclypse provides products that take the tedium out of testing electrical aircraft systems by using automation.
Chris has years of experience in the United States Navy, Hughes Aircraft Company, and Eclypse. Chris is no sit-behind-a-desk marketing executive. His idea of field support is not to pick up a phone, but to pick up a suitcase. His sophisticated knowledge of complex electrical systems has helped put Eclypse International products as standards in the United States Department of Defense.
During the interview he details much of his experience and even talks about projecting life for systems. It is a quick fifteen minute interview.
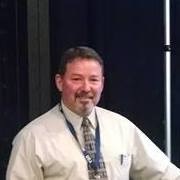
Today’s guest is Chris Teal, marketing director at Eclypse international. How are you today Chris?
Chris Teal: Great John, how are you?
John Gilroy: I know you’re a busy man, you’re getting pushed and pulled in 8 directions. Then you blocked out maybe 20 minutes for us this afternoon to talk about your company and some of the services you provide. I would like to start off with finding out more about you. Tell me about your background and how you wound up working for eclipse international please.
Chris Teal: I’m a former US navy, er, senior enlisted non-commissioned officer. I was responsible for working programs together with our NATO allies in the form of communications links and in combat systems, how we fight wars together. After that I worked for Hughes aircraft company as a systems support engineer supporting the way our ships are overhauled through the various shipyards around the world. From that I ended up getting into the carrier side, LHA side, the helicopter Navy whereas I transformed jobs from Hughes aircraft over to Eclypse back in 1996, the focus is mostly on aircraft. So I have a pretty wide range of everything from submarine ships and now aircraft.
John Gilroy: The nicest part is that you got hands on, it’s not just in a book somewhere you actually been there, done it and sweated and …
Chris Teal: I have scars on my knuckles.
John Gilroy: I know that from working on cars. Yeah, I know how hard it can get, it can get crazy. You know um, before this conversation we had a telephone call and you talked about Lectromec and Eclypse international. Maybe you could get the, the listeners maybe a quick little thumbnail sketch of how you worked in the past?
Chris Teal: Well, back in, er, if you remember the TWA hubbard aircraft accident, we got involved in what was called the ATSRAC. A-T-S-R-A-C. Air Transport Safety Rule making Committee. Back in 1996, after 1996 we used to actually start going full force on that with all the OEMs going, Airbus, some representative from the airlines. That’s where I first met Armen Bruning from Lectromec and his team. We all met out in the rain, looking at aircraft that were recently retired trying to figure out the modes of, the effects of how aircraft wire fails and hopefully to do predictive analysis of, you know, get it changed out before it fails. So that’s where I met your team and we proceeded on that from early ’99 till 2002, 2003 and that program concluded with it’s safety report and you can read that all online if you look up the acronym ATSRAC.
John Gilroy: Uhum, yeah.
Chris Teal: That’s how we met.
John Gilroy: So you’re company’s website is e-c-l-y-p-s-e . org and I’m at there right now. You’ve got trains, you’ve got aircraft, rail systems, automobiles, ship board systems, the whole wide range of areas you’re involved in.
Chris Teal: That’s correct.
John Gilroy: I want to focus maybe on the aircraft side or the EWIS side as the people in the business talk about all the time. You know, when I do research on companies before I do these podcasts, I go to the website and look around and I go to LinkedIn and it’s pretty good. When I went to your Facebook and I said, ‘Winner, winner chicken dinner!’ This is an interesting page you’ve here I mean, you’ve got videos, you’ve got all kinds information talking about your latest NASA patented technology. Wow you’ve put some work into the Facebook page, huh?
Chris Teal: I actually … Believe it or not, I have to keep in communications not only with my family when I’m on travel, but my coworkers and we network through that Facebook page more frequently than we do our website and our customers. Our customers aren’t on an internal server like our website and our company employees so, since I am the marketing director I have to talk with hundreds of people that I go out and meet and stay in contact with annually so …
John Gilroy: You know what Chris? it’s not a picture of you, it’s a picture of your customers. That’s what I like about it. it’s like hey, this … your customer signs your paycheck, you’ve got your customers right there and you’ve got your equipment right there so that’s really good. In-fact you open it up today and you find our latest NASA patented technology for lightweight handheld too useful. A lot of practical tips here. I got up pretty early this morning and I fired up my computer and I went to Google and I typed in these interesting words, I typed in “aircraft automated electrical test and troubleshooting” and I got 18 million, 700 thousand results. So, there must be someone in the world who’s interested in what your company does, aren’t there?
Chris Teal: It seems to be doing very well right now as everything gets more electric, right?
John Gilroy: Yeah, yeah. So what we have here is, we see an industry that seems to be making a transition. We see more and more higher voltages in aircraft. We see systems that try to expand in the commercial world, they’re trying to add wifi and every system whether it’s military or commercial we are looking at, well they’re probably going, “how can we make this product more lightweight?” Every step along the way they have to test it to make sure it’s effective so, if I can knock on your door and say, “you can save 50% of weight with this type of wire, put the wire in.” You have to know it’s gonna be working correctly, so that’s where your company fit’s in, is that right?
Chris Teal: That’s correct, that’s correct.
John Gilroy: So tell me a typical situation you’re in, maybe a typical environment … What you’re doing over the weekend and how that fit’s in, so my listeners have a better idea of what Eclypse international does.
Chris Teal: What a basic product does for any of our customers is, a lot of the avionics designed by the airframe manufacturers have the theory that you have a bit test and the bit test is gonna tell you that this LRU or this box is bad, this component is bad. What our systems do is, not only for doing predictive maintenance, but our systems allow to check the EWIS systems rapidly and almost faster than it takes them to take another avionic package, which is pretty darn quick. So we are changing the rules and the flow sheet, the troubleshooting diagram, or the Fall Isolation Procedures, they call them FIPs in the military. We are actually adjusting the top of the flow diagram that says swapped the avionics. Instead of swapping the avionics, now they can check the wiring EWIS faster and then not lose out that avionic asset into the spares pool, which cost some, you know, 30 to 300 thousand dollars, for each component. So you’re talking a big … Even if it’s not bad it has to go through and be rechecked and retested so. It does come down to money, there is a lot of safety involved with our EWIS testing but the financial side is pretty darn big when you look at it. So one of the things we’ve noticed, one of the things I’m sharing at the conference next week is presenting roughly… There’s about a 20% savings in a reduction of avionic requirements and repairs, they’re going in your pool. Anybody that runs repairs for avionics can sum the value of that and for airlines it’s millions of dollars, for military it’s billions of dollars. So it’s big money.
It does come down to money, there is a lot of safety involved with our EWIS testing but the financial side is pretty darn big when you look at it.[…] There’s about a 20% savings in a reduction of avionic requirements and repairs. […] for airlines it’s millions of dollars, for military it’s billions of dollars.
John Gilroy: So this is what AWTS, Automatic Wire Tests, is?
Chris Teal: Yes. The Automatic Wire Test Set is an acronym given to our product circuit analyzer that was known as a simple model 503, circuit analyzer in a ruggedized enclosure. The acronym that the navy and air force and marine corps gave it was AWTS, which is called the AWTS. We have to put an acronym on everything I believe. But it’s a name they gave it back in 2008 when they acquired over 240 of these systems to be propagated out to the different air frames.
John Gilroy: If you’re listening this podcast and you want to learn more, you go to Facebook, type in Eclypse-international, and you can go to the website, which is simply Eclypse.org and you go to YouTube. I went to YouTube this morning and there’s like 4 or 5 videos. So you can actually go on YouTube and see exactly, images of what’s going on in the system can’t you?
Chris Teal: That’s correct.
John Gilroy: So what’s the technical implementation of the AWTS? So what happens is, a technician brings it onboard and plugs it in or how exactly how is it set up?
Chris Teal: Well, it’s an offboard equipment test. There have been folks who have taken it in flight but it’s very few and far between and it’s larger aircraft when they do that. For like an F16 or smaller aircraft or a Learjet you would probably not bring it inside, you’d probably bring it up to where you, what we call the business end of our equipment where the connectors are at and they tie in with what’s called test adapter cable or TAC and that mates into either what we call a one end test or a double ended test. A one end test is checking it from like the ebay out to the cockpit and we’re leaving the avionics on the other side tied in. So you’re not really disassembling your aircraft too much. That’s the common mode of using it as a troubleshooting tool. It’s one ended testing ’cause it saves time, you don’t have time to tear apart the jet and take off the plastics and panels, the axis, the power relays, and so forth, and the conduits.
John Gilroy: You know in civil engineering when they test concrete they have what is called non-destructive testing, which I’m thinking that can apply to what you are doing here. You’re not ripping things apart, you’re just going through the system itself.
Chris Teal: That’s right, and our approach first is NDT. Now, some of the airlines are coming at us right now looking for the capability to do what we call inspection test protocol or multiple test protocol, different names for it from different organizations. But what it does, is, we check the health and integrity by using different stimulus, either voltage and/or current to load the wire and load the lines, not to not to exceed SR88 rules for the wire types and voltages which is 600 volts for most of them, 1000 volts for the power feeders. But, we use 500 volts as our max, that’s the arm services standard now and we basically use 1 amp with the current, but we use different decade steps of current in order to evaluate the response back and measurements from those wires.
And to simplify it, what we are doing in our inspection test protocols, we try to make it as easy as Sesame Street. We try to make it like, which wire isn’t the same, which one is not like the other. And without showing you on this podcast, I’d like to say it’s like a visual excel chart, you can see the different measurements on each like 300 wires in a bundle. And we compare one with the other on not just in it’s conductor, but in it’s insulating capabilities. When you automate it you can see it real time, you can actually manipulate the harness with your hands and watch it change. So it’s very dynamic and a lot of people don’t understand that automation and speed allow you to do things like this.
John Gilroy: I imagine there’s some misconceptions involved in what your service does.
Chris Teal: Oh, most people think people think it’s just like a multi-meter, you go and check for so many ohms, but it’s not, it’s a science, it really is inspection test protocol. We are really testing a conductor in relationship with air frame and the rest of its system wires, so it’s pretty unique. Now, Lectromec takes you a whole step further and does aging properties of sulfur that we do not do, but the stuff we do is as much possible as we can do on wing or on aircraft.
John Gilroy: Tell me Chris, what are some of the biggest technical hurdles that you face with your products.
Chris Teal: Well. Culture change of people that are out there, the old-timers like me. The people that are out there that don’t want to change and I find it that there’s nothing better to me to change an old timer. Somebody like me out there, like uh… I’m working with a gentleman down in the navy, that’s been working in helicopters for many years and, you know, some people say “I’m not gonna carry that out to my plane, it is too big.” But they’re finding out now that they, you’re not gonna fly my airplane unless you use that on it now. That’s what we are at with the navy marine corps, they don’t even want to take the helicopter out of the hangar till it’s looked at by our equipment. So, they’re normally used to take in little handhelds out, little easy things to do quick checks with and be done.
What we have to change on the mentality is if you’re gonna start swapping boxes, you’re liable to damage things and continue to damage things, it costs money and time. So why not go out there a little bit smarter, take a cart with the system out there, spend a few more minutes in your pre-diagnosis, saves you sometimes hours and days and maybe even weeks if you damage your aircraft. So they are starting to learn, it’s the culture, the culture is the hardest to change.
John Gilroy: So on the Facebook page, is this the what you’re talking about, the big yellow box here?
Chris Teal: That’s correct, that’s the AWTS, that’s an AWTS set. Now, if you look up on the top of the Facebook page you will see a training class going on on what the marine corps calls, the mobile air logistics which is a little trailer, it is actually pretty small and condensed, but they tie it together and it could be deployed anywhere right off the ship. They lift them off the ships, they put ’em on trucks, they drive ’em to any part of the world and they plant ’em and they got a city and a maintenance facility in the middle of nowhere. And that’s what this is. The shelter in here, our AWITS fits in there as part of that now, the logistics. So everything is color coded, the boxes are yellow, the test adapter cables are yellow, it’s so that they can keep it together and they understand it’s for the AWTS.
But normally, they don’t have this type of equipment at that field location. This is something phenomenal, they are actually teaching it in their training commands from day one, which is how we have to change the culture. They’re starting to adopt this into their training curriculum from day one, so then it becomes natural to the young men and women that are out there working this.
John Gilroy: It increases reliability and reduces cost, I mean it’s almost a no-brainer.
Chris Teal: It is and the young folks today coming up are computer savvy. They can follow directions from the screen and they don’t have to be experts on a 20 year electrician. They can actually follow directions and become knowledgeable on how that aircraft, no matter how complex, what wire runs to what point pin to pin. And that’s how automated speed and displaying those sub-systems enables these young folks to learn so quickly.
John Gilroy: So rather than rip and replace, it can really target a specific harness or even a specific section, they don’t have to worry about taking out a whole group?
Chris Teal: It actually has fault locations so it can locate down the pipe where it’s at.
John Gilroy: Wow!
Chris Teal: So they don’t even have to … like in a large aircraft you can estimate that it’s half way down, or 40% down, or 30% down, or 20% down and it gives you a percentage or distance of the whole length. So it allows them to judge. There’s a lot of human factors in judging lengths and feet you know, especially how the wires and harnesses are routed through the aircraft. It’s a 3D thing, it’s no a 2D print that they are looking at. In real life it’s a 3D shell skeleton of where that harness is running through. So it allows them a percentage of where that failure is down that wire harness path so that they can estimate, oh look at it, it has a 90 degree turn up here maybe that’s where it’s happening. So at least we are getting our head in the right area, 18 inches, so they can turn left and right and look you know?
John Gilroy: When you look at the next 5 to 10 years, where do you see the industry changing?
Chris Teal: I see more, more fiber optics, I really do, however, even though they increased fiber optics, I see an increase in electrical requirements for power. So if anything it’s going to get more electric, not less. In the next 5 to 10 years I see the electrical wire and harnesses being part of the skin. Part of the skins today are what, composites right?
John Gilroy: Yeah.
Chris Teal: So I see them being molded into composites where you remove a panel and there’s your harness in it.
John Gilroy: With increased number of sensors as well?
Chris Teal: Absolutely. Embedded.
John Gilroy: It’s like, okay there’s a hundred of sensors in there and you’ve got 500 channels and nothing to watch, I mean, you have to make sense of all the sensors that are there and I think that’s where sophisticated equipment’s gonna fit in.
Chris Teal: Good point! We’re actually collecting data on all these aircraft, unseen to these troops that are using it, that we as engineers and scientists can look at it and decipher, what is it we need to put in the next model of jets in those sensors? How do they really fail, how do they start to fail? When they start to fail, when is it a good time for us to change them?
John Gilroy: Now, I was talking to a fellow, and he is a high level executive at Adobe and he says he has 47 IP enabled devices in his house and I said well great, now what? (Laughter) I mean, so what? I mean what good is it, you could have 5,000 but if you can’t control maybe the security, the heating and the cooling, it doesn’t mean anything at all. So what you can do with this is, it will help you in making projections for reliability for future systems, which I would think would be important for increased reliability for military, for commercial as well.
Chris Teal: Yes, yes absolutely I agree with you. There are certain zones and certain subsystems that you would monitor first, those being flight critical and those being those exposed to the environment.
John Gilroy: Well, yeah, it’s the world of IP all around us. You know, I’ve done a lot of these podcasts for people who are in and out of all kinds of aircraft and here’s the up close and personal question for you Chris. You do a lot of flying and a lot of traveling, what’s your favorite aircraft?
Chris Teal: It’s sundown already. My favorite one is the F14 Tomcat.
John Gilroy: Really, isn’t that something? 10 people, 10 different opinions there, isn’t that something?
Chris Teal: The 15 is a good bird (laughs), but I was navy so I have to go with the 14 (laughter)
John Gilroy: You don’t have a choice, you probably have a tattoo on your arms saying hey I don’t have a choice here (laughs).
Chris Teal: Those are, they can almost go vertical off the tarmac when they are taking off. So they can almost go like a rocket straight up and there’s not too many jets that can do that.
John Gilroy: If you’d like to have more information about Eclypse International, you can go to their website Eclypse.org and I would go their Facebook page, Eclypse International. You’ll see all kinds of videos and actually see the product itself and get a hold Chris Teal if you have any information. He’s had a lot of different trade show or he can email you right from the website as well, that right Chris?
Chris Teal: That’s correct.
John Gilroy: Well Great.
Thank you for listening to the Lectromec’s Podcast and thank you Chris. If you’d like to learn more about aerospace wiring, please visit our website Lectromec.com, we have free white papers, newsletters, videos, 164 blogs and much more.
If you enjoyed this article and would like to read more, please consider: