Key Takeaways
- Fewer restrictions on conductor materials for J1127 and J1128 wire allow for alternative conductor constructions.
- With the lower average exposure time and the exclusion of a post-exposure bend test, J1127 and 1128 fluid immersion testing is less severe than the parallel aerospace method of AS4373.
- Most AS22759 wires would be qualified for use in place of J1127 and J1128 wires if specific insulation thickness requirements were not needed.
It is no surprise that the automotive and aerospace industries have different approaches and requirements for wires and cables. The SAE J1127 and J1128 standards define two classes of automotive vehicle wiring. SAE J1127 covers heavy gauge battery cables (e.g. starter and chassis ground leads) and SAE J1128 covers lighter primary wires used in general purpose wiring harnesses. Battery cables (J1127) are typically 6 AWG or larger to carry high currents in 12–24 V systems. In contrast, the general-purpose primary wires (J1128) are smaller conductors used for lighting, sensors, and low‐power circuits up to ~60 VDC.
In this article, we review the J1127 and J1128 wire standards, the extent of testing performed on these wires, how they stack up against aerospace wires, and if there are parts of these standards that could benefit their aerospace counterparts.
Overview
Whereas aerospace wire insulations are often fluoropolymers, J1127 and J1128 use alternative insulation types. The primary three types of insulation identified in these standards include:
- Thermoplastic insulated (includes PVC insulation),
- Cross linked polyolefin insulated (XLPO), and
- Thermoset Elastomer (Synthetic rubber) insulated
The insulation types here have different thermal performance levels starting with a temperature rating as low as 80oC.
The conductors may be tin, silver, or nickel coated conductors as long as they meet the performance requirements identified in the standard. The standard does not have specific requirements that the conductor must be plated, just that, if the conductor is plated, then it must meet some performance requirements.
Furthermore, there is not a specific requirement in the J1127 and J1128 specifications that the conductor substrate be a specific material/alloy, so alternative conductor constructions, such as copper clad steel may be used.
In contrast to aerospace applications, where the conductor substrate and plating are specifically identified for each configuration. This is done to ensure greater intermateablity of aerospace parts and reduce the potential for the occurrence of galvanic corrosion.
Voltage Rating
Both the J1127 and J1128 are designed for low voltage applications with a maximum use voltage of 60VDC. The insulation integrity is verified via a voltage withstand test performed at 1000VRMS. This high voltage test ensures the insulation can withstand any voltage surges that might occur in the system.
Oil/Chemical Resistance
Fluids exposure is also part of the J1127 and J1128 specifications. As should be expected, these automotive cables are assessed for their resistance to typical engine fluids (gasoline, engine oil, coolant, hydraulic fluid, battery acid, etc.). The exposure duration for each is 20 hours at different test temperatures that are in alignment with their typical use on the vehicle. The post fluid exposure assessment includes a diameter change assessment (identifying if there was absorption and swelling of the insulation) followed by a dielectric voltage withstand test.
AS4373 fluid exposure testing of aerospace wires follows a similar path but the post test of the sample includes a bend test where the sample is wrapped around a mandrel several times. Doing this helps to exacerbate any insulation degradation, increasing the chance of dielectric voltage withstand failure. The important factor for both approaches is the assessment of swelling/diameter change and DVW capabilities.
Mechanical Tests
A review of the J1127 and J1128 specifications shows that there are mechanical performance requirements limited to the performance before and after accelerated thermal aging of the cables. These tests assess the tensile strength and elongation of the insulation and follow the requirements of ASTM D412. Because there are performance minimums, this means that there can be significant mechanical performance differences of J1127 compliant cables. As such, users should be careful not to swap suppliers without assessing the performance differences.
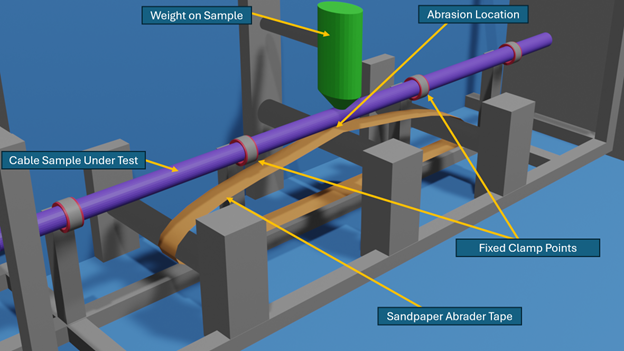
For J1128 cables, insulation abrasion resistance is assessed with a “Resistance to Sandpaper Abrasion” test. In this test, the wire is suspended between two fixed points with a defined weight placed at the center of the wire span. Under the cable, a sandpaper band abrades against wire at a defined speed until an insulation breach is detected.
This contrasts with the common abrasion test method used in aerospace where a needle abrades against a wire’s insulation until breach. This has been discussed in several Lectromec articles.
Flammability
Flammability is an area where there is a divergence between the automotive and aerospace standards. For the J1128 standard, the requirement is for the cable to be exposed to a flame for 15 seconds and not to continue burning for a duration greater than thirty seconds. In contrast to the AS4373 or FAA requirements on general purpose EWIS flammability requirements, a wire or cable must self extinguish within 3 seconds after a 30-second flame exposure, no propagation of the flame, and have no molten insulation drops ignite tissue paper below the test sample. As such, while a general-purpose aerospace wire may be appropriate for automotive applications, the opposite is not true.
Conclusion
The J1127 and J1128 standards provide a good framework for wires used in automotive applications with assessment techniques for thermal, mechanical, electrical, and environmental performance. The testing is limited to those tests that are most applicable for the application and does not include those that might be deemed as low risk for automotive applications. Because of this, qualification testing of J1127 and J1128 cables should typically be a straightforward process that can be completed in less than 8 weeks.
Based on the review of these standards, most AS22759 wires would be qualified for use in place of J1127 and J1128 wires if specific insulation thickness requirements were not needed (e.g., the grommet size at the back of a connector). The qualification tests of AS22759 and other aerospace wires go far beyond the J1127 and J1128 requirements as is necessary for aerospace applications.
To find out more about qualification for J1127 and J1128, contact Lectromec.