Aircraft maintenance engineers do not pay much attention to the impact of storage on electrical components. This article discusses several aspects of storage in the general category of the electrical wire interconnection system (EWIS), or aircraft EWIS components. We will examine the stowage of connectors, waveguides, harnesses, as well as capping and stowage of terminal wires in Severe Weather and Moisture Prone (SWAMP) areas.
Conductor Stowage Background
Stowage of conductors is dependent on the aircraft’s operational requirements. There are four categories that determine the aircraft’s components’ state:
- Operational – The conductors are ready for flight status.
- Non-operational – The conductors are not ready for flight status (they will require major maintenance either scheduled or unscheduled).
- Long term – The system’s components are available for use during specific mission configurations, but are not regularly used on a daily basis for longer than a month.
- Short term – The system’s components are removed for maintenance for less than a month.
These categories are combined to make statuses such as “operational-long term” and “non-operational-short term” to describe the state of the aircraft and its components. Each of these statuses has its own set of instructions for stowing and cleaning the connectors. (See Lectromec’s EWIS SLEP: Five Days in the Desert article for more information on the boneyard).
Connector Stowage
For operational-long term and operational-short term aircraft connectors, military standard metal covers are preferred and should be used over plastic covers. However, if the standard metal covers are not available, then the end of the connector can be wrapped in pressure sensitive tape for electrical connectors and secured with lacing tape. Before sealing the connector, it should be cleaned.
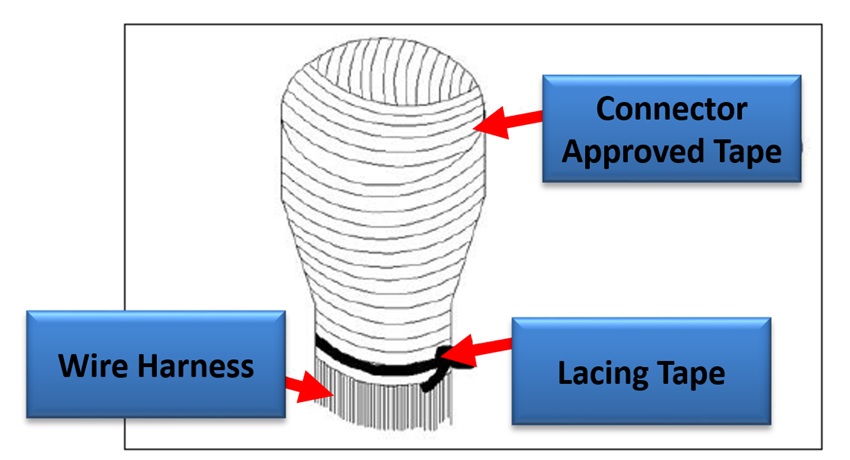
As for the non-operational-long or short term aircraft, the requirements are the same as those for the operational-short term aircraft.
SWAMP Areas
Wires and connectors located in SWAMP areas are required to have extra layers of protection. During the cleaning the connector prior to starting the procedure, a Corrosion Prevention Compound (CPC) must be applied to the conductor. Failure to apply a CPC prior to connector stowage and re-application at required intervals will result in corrosion damage to the connector. Note that this is for storage applications and should not be used for in-service conditions (see Lectromec’s Corrosion Prevention Compounds (CPCs) and EWIS).
When in SWAMP areas, wrap the connector end with stretch seal tape then apply a heat-shrink end cap on top of it. In order to prevent moisture accumulation in the conductor during stowage, secure the connector vertically using a clamp or tying and lacing tape.
WAVEGUIDES
Waveguides are important yet incredibly fragile devices. Waveguides must be kept extremely clean and dry—even the slightest amount of moisture or smallest speck of dirt can reduce their effectiveness in transmitting proper wave forms. Since they are so fragile, only pressure sensitive tape should be used on the waveguides.
After ensuring that it is clean and dry, simply tape over the end with the tape overlapping to ensure all openings are covered. Depending on the temperature and vibration application of the waveguide, different lacing and tying tape should be considered to secure the device.
CAP and Stow
There are three ways to stow and cap terminals and wires based on the environmental applicability and the temperature of the area.
- Heat-shrinkable end caps – Environmental applications up to 150°C
- Stub splices M81824/13 – Same as above
- Pre-insulated end caps that be crimped – Non-environmental applications up to 105°C
After the ends are secure, coil the wire into a loose coil and secure it.
Conclusion
It is incredibly crucial to pay attention to detail when dealing with a high risk area like a SWAMP area or high risk devices like wave guides. Failing to do so may reduce the effectiveness of the wire system and may require more maintenance. Thus, it is important to store and care for wires properly so that they are not exposed to additional degradation. Following these steps will ensure longevity of the aircraft and make it safer for use.