Failure analysis and system reliability are a fundamental part of the aerospace industry. With the extremely rare exception, modern aircraft are assessed and evaluated at the component, system, and aircraft level for all manner of failure impacts. This article will give methods for effectively analyzing data and discuss the commonly accepted Failure Mode and Effects Analysis (FMEA) technique as it is applied to the Electrical Wire Interconnect System (EWIS) for aerospace, using MIL-HDBK-683 as a guide.
As the title implies, the MIL-HKBK-683 is a set of guidelines the military uses to discuss tools and analytical techniques used for effective decision making. Although MIL-HDBK-683 is primarily focused on process improvement, the particular application will have industry specific language describing the means of assessing failure modes common across industries.
FMEA is a common qualitative analysis tool developed in the 1940s for failure analysis that requires an in-depth analysis of all sub-systems for the purpose of identifying potential failure modes as well as their root causes and effects. In this assessment, each failure mode is given a probability of detection and a probability of system failure. The following steps can be used as a guideline when performing an FMEA.
1. Identify Failure Modes
Assess all potential failure modes in a system. This requires an in-depth understanding of how each sub-system interrelates and contributes to the whole system. Identification of potential failures can be the most challenging step when performing an FMEA, especially in complex systems where one failure mode can be the cause for another failure mode in another sub-system. When applying FMEA to an aircraft’s EWIS components, there are numerous potential failures that need to be assessed. One common failure mode found on EWIS is harness chafing; it will be used as an example throughout the rest of this article.
2. Root Cause Analysis
Determine the root cause of each failure mode. This step requires an underlying problem assessment. If performed with a new design, this may include the development of a “fishbone style” analysis to examine potential weak points in the design. When looking at EWIS, one common cause for chafing is improper clamp installation. When clamps are installed improperly, the harnesses can have too much room or they can be too tight. In each situation, the harnesses will either chafe on each other or against the clamp causing the harness to deteriorate over time.
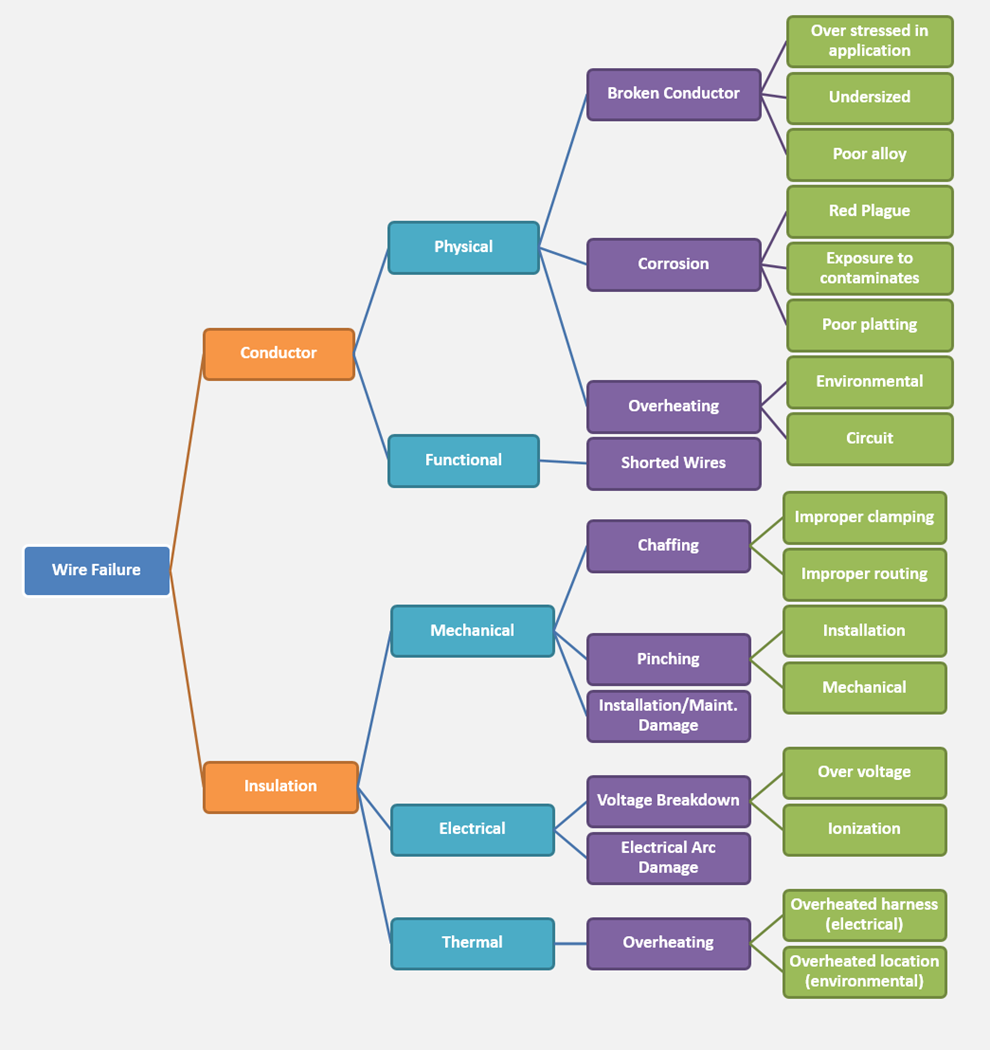
3. Probability of Failure Occurrence
Calculate the probability of occurrence for each failure mode. If component failure data is not available, then a qualitative scale can be used. For the example here, a scale of 1 to 10 (1 being a very low probability and 10 being a very high probability of occurrence) will be used. Chafing points found on older aircraft are often due to more maintenance and replacement activities. Since it is common to find various chafing points, the score for the probability of occurrence is a high score of 8.
4. Failure Criticality
Estimate the weight or criticality of each failure mode on a scale of 1 to 10 (1 being a very low failure criticality and 10 being a very high failure criticality). For those familiar with FAA AC 25.1701, five severity levels are defined ranging from “No Safety Effect” to “Catastrophic.” In our example, the wire harness being chafed contains some power wires, but mostly low power and signal wires for the In-Flight Entertainment System. While the functional impact due to failure is low, the physical damage may cause damage to structure and other systems. Therefore, chafing will be given a moderate score of 6. For further discussion about EWIS failure criticality, you can read Lectromec’s EWIS Regulatory Compliance with 25.1707 – Part I article.
5. Latent Faults
Estimate the probability of “escaped” defects. Escaped defects are the number of failures that are not detected during system checks, such as an inspection. Being able to detect chafing on harnesses is fairly easy when inspection and maintenance checks are performed on a regular basis. Consequently, the probability of having escaped defects is small resulting in a low rating of 3. This value can be modified if routine maintenance checks are not performed on a regular basis.
6. Risk Priority Determination
Calculate the risk priority number by multiplying the values determined in Steps 3, 4, and 5. The resulting value can be used as a way to prioritize and allocate the necessary resources to mitigate the high-risk potential failures. Mitigation may come in the form of rerouting, secondary harness protection, or reducing the likelihood of failure with regular inspections. If periodic inspections are considered, the FAA has suggested a process called Enhanced Zonal Analysis Procedures (EZAP).
Conclusion
This article summarizes the FMEA analysis discussed in MIL-HDBK-683 as applied to EWIS. This analytical technique can be applied to almost any system for determining potential failures and identifying effective mitigation solutions. For more information on other techniques including design of experiments and cause analysis refer to MIL-HDBK-683. If you are looking for turnkey EWIS risk assessment, you can check out Lectromec’s EWIS Risk Assessment Tool (EWIS RAT).