Key Takeaways
- Current guidance for wire harness derating is conservative.
- Modern wire constructions allow for higher currents to be used.
- Lab testing can help save EWIS weight.
If a wire supplies power to a component, and the power signature for that equipment is Pulse Width Modulated (PWM), does this require different considerations than one with steady state power? A first level approximation would be to take the average energy on the different circuits and compare. This is a good first approach, but, if implemented in an aircraft design, this cannot be the last.
The fundamental concept here is harness ampacity: the maximum amount of current transferred down a wire harness without exceeding the temperature rating for any component. Several past articles from Lectromec have considered this from different perspectives:
- Temperature derating in space [link]
- How to derate a wire harness [link]
- Ampacity improvements [link]
- Circuit protection selection guidance [link]
The basis of the derating data was work that was performed back in the 1960s. In this, hundreds if not thousands of configurations were tested, evaluated, and the generalized curves were created for the MIL-STD-5088.
Now part of AS50881, the derating information was created and the basic formulations were adjusted to be conservative. While generalized, the formulas and graphs provided in the standard provide better guidance than that available in EN3197 which limits the topic discussion to, “Wire shall be selected so that the rated maximum temperature is not exceeded for any combination of electrical loading, ambient temperature, and heating effects of bundles, conduit and other enclosures.”
Some of the recent published work by NASA has shown that the position of wires and wire harnesses can have a noticeable impact on the heating of the wire harness. As an example, if the high current carrying wires are placed in the middle of the wire harness, this will generate a higher harness temperature than if those same wires were randomly placed in the wire harness.
As part of the original research, and confirmed with recent findings, there are cases where the AS50881 curves have very little margin. This reduced margin tends to involve larger gauge wires in certain configurations.
Electrical and Thermal Insulation
Beyond the insulation temperature rating, the wire insulation has another significant impact on ampacity: its thermal conductivity. When the tests were performed, PVC was a common wire insulation type (no longer recommended for aerospace applications). Although these wire insulations used in the original study are no longer used on aircraft, the figures still remain.
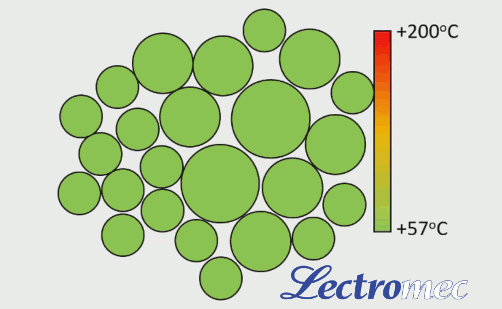
The insulation material is important because the thermal conductivity of PVC is 1.7 – 3.2 times less than typical aerospace insulations today (e.g. PTFE and polyimide). Modern insulation thermal conductivity provides a means of moving heat more quickly from the wire harness, making it possible to use higher currents.
A consideration here is if secondary wire harness protection has a positive or negative impact on the harness ampacity. The overall impact is dependent on the harness protection material. Secondary harness protections that are textiles or designed for fire resistance will likely result in an overall temperature increase of the wire harness (ampacity decrease). However, if the same wire harness is routed in a metal conduit and has good wire-conduit contact, this may have an overall positive impact on harness ampacity.
Validation
From a validation perspective, harness derating, in particular wire harness thermal modeling, has been an SAE 8A task group for a couple years. The task group has had two objectives: first, develop a set of procedures for lab evaluation of wire harness temperatures. Second, develop a set of guidelines that can support modeling tools for wire harness thermal modeling.
In Lab Assessment
To get the most power through a wire harness requires a focused attention to the design, installation, and materials. Lectromec can help you get the data you need to certify your EWIS design choices with our ISO 17025 accredited lab. We have the electrical, thermal, and environmental test capabilities to test your wire harness design to the extremes of your EWIS.