Testing can be complex. From test identification, locking down on test parameters, sample preparation, accurate test performance, proper data analysis, and delivery of a final report, an error anywhere in the process can cause costly delays and spurious results. Using the correct laboratory for testing is undoubtedly important.
This article provides an overview of how testing comes into Lectromec’s lab, how the testing is performed, tracked, and what to expect from the final results.
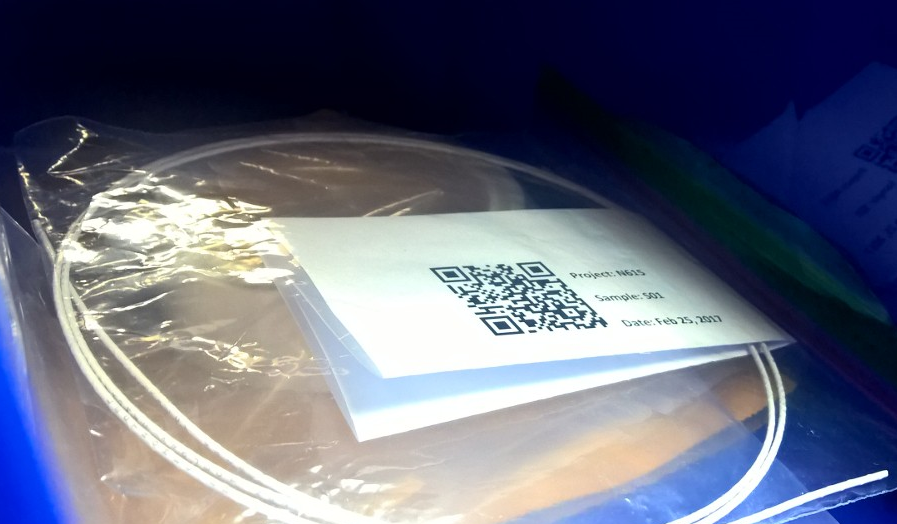
Client Request and Purchase Order
Prior to any testing is performed, a project work or purchase order is created identifying the type of test methods to be performed as requested by and agreed upon with the client. After the purchase order for the work has been completed, work items associated with the samples created and added to Lectromec’s project tracking system. During this time, if any tests require clarification on test parameters (e.g. temperature, weight on sample during testing, etc.), these are communicated to the client and agreed upon prior to moving forward with testing.
For larger projects with multiple samples and/or a variety of test methods with specialized parameters, a project tracking matrix is reviewed with the client to ensure that all tests are performed to match the particular specifications of the client.
After the agreement is finalized and modifications to the work completed, the client works to supply the samples for testing to Lectromec’s lab for the next phase in the project.
Client Sample Receipt
When the client’s samples have arrived at Lectromec, they are added to Lectromec’s receiving queue. Here, each specimen in verified against the project work or purchase order to ensure the sample is allocated to the correct project and handled accordingly. Furthermore, a preliminary visual examination is performed on the samples to determine if any damage occurred during shipping. Any suspected damage is immediately report to the client.
If no damage is identified, the sample is the entered into Lectromec’s project tracking system as a receivable, assigned a unique internal tracking number, and a unique identification or QR code is affixed to each sample. This provides a reliable means of tracking the sample throughout the project.
The samples are then placed into a climate controlled environment ready for the next phase.
Project Testing
The testing start date will vary depending on the particular test requested and the number of other projects ahead in the test queue. Lectromec continually strives for testing to be completed within three weeks after receiving the client’s samples but this may vary due to some tests that are designed to run until failure. As an example, the scrape abrasion test may take anywhere from 6 minutes to 6 days – and 10 trials are required by the test method.
When the samples are ready to be tested, Lectromec’s lab personnel assigned to perform the test select and verify the correct sample by scanning the QR code, remove the necessary quantity or length per the test method, and begin test preparation.
As an ISO 17025 certified lab, we care about the quality of all tests performed in our lab, therefore, tests are only performed by individuals that have been trained on the test method selected and have shown a high level of proficiency within the previous 12 months.
Each test station is paired with the tools necessary for test performance and most up-to-date instructions to ensure the test is performed according to specification. This means that there is never a question about how the test should be performed. As part of Lectromec’s continuous internal review process, whenever a new test variant is identified or needs clarification, the internal procedures are reviewed, and if necessary, updated.
Depending on the test being performed, the data may be recorded digitally or is converted after the test is complete.
For those interested, Lectromec can provide a live web feed or video to watch the testing be performed. Please note that this may be an additional cost for your project.
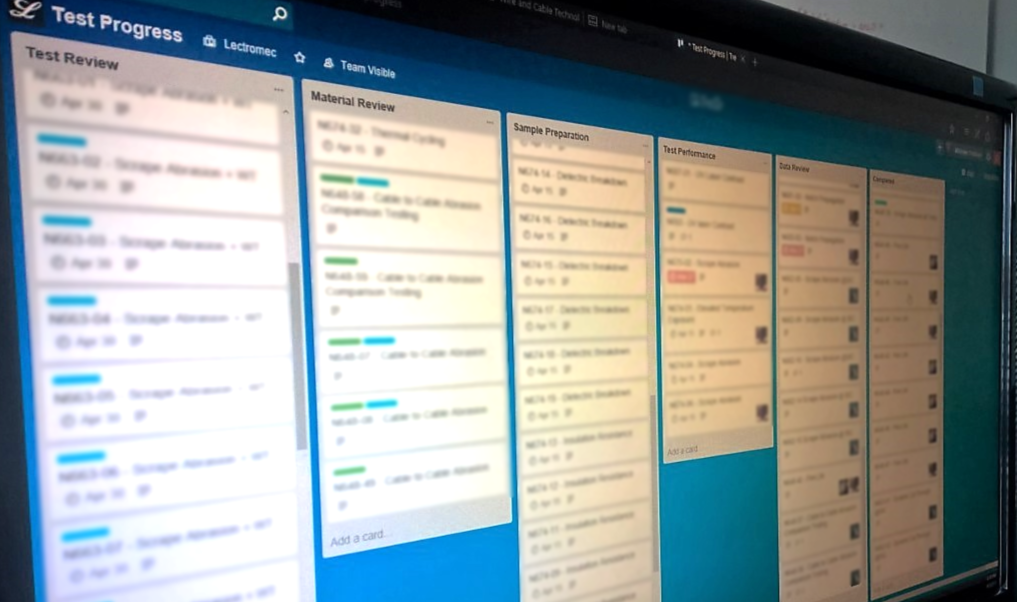
Reporting
Lectromec provides a detailed report for each of the tests that is performed. Typically, a client can expect the report will include many of the following:
- Description of what is evaluated with the test method used,
- Clearly identified parameters and margins of error on measurements,
- Photos of the test setup,
- Test results often with pre- and post-test photos (if applicable),
- Data analysis, and
- Comparison against a specification to identify if the component passed or failed the criteria.
- After the report is delivered, Lectromec schedules a final consultation to address any questions the client may have with the project results.
Summary
At Lectromec, we care about providing high quality results and transparency when handling client’s testing needs, which is why we integrated throughout our process ways to track and communicate project status to our clients. This ensures that each project is handled with the utmost care and that each client has opportunities to present questions at each phase of the project cycle. Contact Lectromec to find out more.