Key Takeaways
- Backshells and accessories are a necessary part of wire harness design.
- In 2004, the FAA funded a study to examine how tightly bound a backshell must be to a connector before there was an impact to the backshell connector resistance.
- The AS85049 aerospace standard provides various test methods for connector accessories, including backshells.
Introduction
The backshell of a connector is an item that perhaps does not get the attention that it should. Often the discussion of EWIS focuses on the wiring, the connectors, or managing the risk of EWIS failures, but the connector backshell is ignored. The simple connector backshell (that is anything but simple) is designed for support and protection of wires and cables physically and, in the case of signal cables, support and protect electrically too.
The following is a brief introduction to backshells, their use, associated standards, and research that has been performed to determine what to look for when performing maintenance.
Backshells
In general, connector backshells fall under the classification as ‘connector accessories’. Backshells are the components that attach to the back of connectors often designed to guide the wires and cables that are terminated at the connector. The backshells are often mated with strain relief components, environmental seals, the shielding. The backshell may be made from metal or molded using a rubber or neoprene covering over the backshell of the connector.
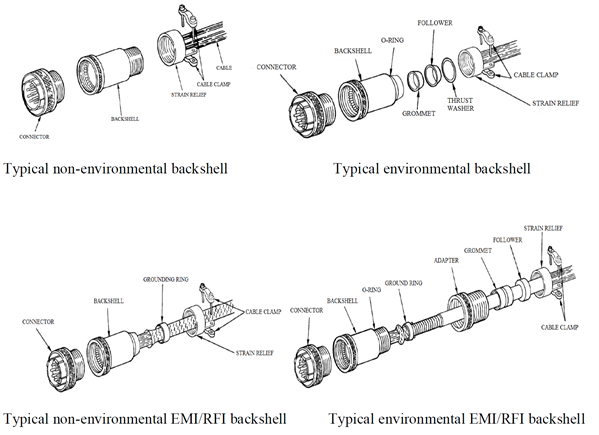
Standards
Most connectors will have some backshell and accessories, and this should be considered as evidence that backshells and accessories are a necessary part of wire harness design. Perhaps the most common connector backshell/accessory standard for aerospace is the AS85049. The standard is written to address the generalized needs of connector accessories covering a wide range of applications. In the latest revision, there are 17 accessory categories to cover different stress environments and EMI protection requirements.
Within the AS85049, the test methods for accessory evaluation are listed. These cover the environmental stresses, fluid susceptibility assessments, mateability, mechanical stresses (vibration and physical shock), as well as electrical performance requirements. Taken together, the AS85049 provides a set of assessment methods to evaluate just about anything that might be attached to the backside of a connector.
Maintenance
EWIS inspection is mandated for part 25 aircraft and should be part of all other aircraft periodic maintenance and inspection activities (discussion of enhanced zonal analysis programs EZAP, can be found here). So, what should a maintainer look for with backshells during maintenance and periodic inspection activities?
To aid in the assessment of connector backshells from a maintenance perspective, the FAA funded a study to examine this issue . Specifically, the study examined how tightly bound a backshell must be to a connector before there was an impact to the backshell connector resistance.
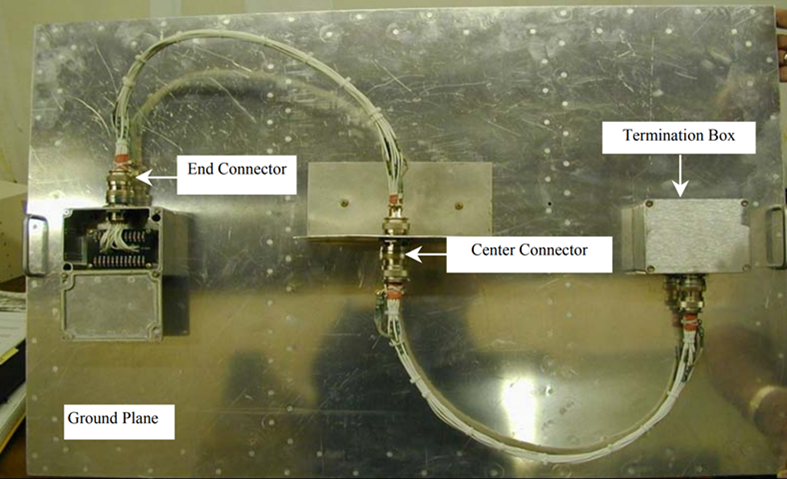
The testing examined the loop resistance for a series of backshells with the various degrees of disengagement (see accompanying figure for the test setup). The level of disengagement was identified by the rotation of the backshell from the proper set position.
Within the testing, there were three different levels of loosening:
- Thread loose backshell: after the backshell was torqued to the particular manufacturer specifications, the backshell was loosened by rotating back between 90° and 360°. Once an additional thread of the connector was visually observable, then the backshell was declared thread loose.
- Visually loose: The ‘visually loose’ term identified visually identifiable misalignment of the initial position marker.
- Hand loose backshell: in this scenario, the backshell was identified as hand loose if it could be easily manipulated by hand.
As expected, as the backshell pulled back from the engagement with the connector, the loop resistance value increased. Data is presented in the FAA report showing how this loop resistance changed for the different connectors based upon various environmental stresses which included vibration, altitude and thermal cycling, and mechanical degradation.
Based on the above observations, the following is recommended.
- Connector backshells should be checked for looseness during scheduled maintenance. Approaching this from an EZAP mindset, that means that each connector must be within arm’s reach during inspection and EWIS sustainment actions.
- A visual inspection using a mark reference, to indicate any loosening of the backshell, is the most effective method for the two types of backshells studied. This mark can be made with a wax/silicon bead, a permanent marker, etc. If the backshells are not marked, a check for hand looseness should be performed during scheduled maintenance.
- A visual inspection with no mark reference (thread loose) is not efficient in determining backshell looseness.
- A loop resistance measurement should be made on wire bundles when their backshells are not visually or physically accessible during routine maintenance.
The conclusion of the FAA report indicates that there was a significant variance found during the testing between two different types of backshells. Because of this, there was a recommendation for an additional study to determine what was the best mechanism for maintenance procedures for a wide variety of backshells. Unfortunately, the FAA did not fund any additional study (the report was released in 2004 and FAA funding has moved to other areas), but the recommendations of the first body of work are still valid.
With that said, what does a maintainer or someone who was building a maintenance program need to consider for connectors and backshells? The enhanced zonal analysis procedures should include physically touching the back shells of connectors to ensure they are not loose. The results of the study did find that the loop resistance had the greatest degradation once the backshells could be physically turned by hand. Initial quality inspections of the connector backshell mating, can help to reduce the likelihood of backshell disengagement. Beyond this, the data from the FAA study can help to guide inspection intervals for these items.
Conclusion
Those testing new backshell configurations for their vehicle should consider the procedures outlined in the FAA document as a guide for assessment. The testing is relatively quick and can be very informative in the definition of maintenance/inspection procedures. This is certainly recommended for those backshells supporting high-speed data cables or EMI sensitive wiring. It is well established that maintaining a good shield to backshell to ground plane connection reduces the overall noise of the system.