Key Takeaways
- Volume resistivity is a measurement of a material’s ability to resist the flow of electric current through its volume.
- While the ASTM D876 provides a guide for testing, the AS23053 provides values for specific heat shrink material properties.
- Though not required unless specified, the adhesive internal layer should be evaluated for flammability.
Heat Shrink Electrical Resistance
Since its invention in the 1950s, heat shrink tubing has provided a convenient means of providing an additional protection layer that contracts when exposed to heat. This additional layer provides extra electrical insulation, physical protection, and strain relief at connector backshells. Beyond initial wire harness fabrication, heat shrink tubing is also a common part of wiring repair.
From an aerospace perspective, the SAE AS23053 “Insulation Sleeving, Electrical, Heat Shrinkable, General Specification” is among the more common heat shrink standards employed. The standard itself covers a variety of testing methods including physical, chemical, and electrical tests and evaluations to assess if heat shrink product meets the requirements set forth.
The AS23053 not only provides testing guidelines for heat shrink generally, but also requirements for specific types of heat shrink tubing, represented by various “slash” types (e.g., /11 or /12). The differences between the slash types vary, such as chemical differences and performance levels. Within each slash type there is a set of requirements for the material properties, one of which is volume resistivity.
Volume Resistivity
Broadly, volume resistivity is a measurement of a material’s ability to resist the flow of electric current through its volume. Conductive materials have a lower resistivity, where current flows more easily, while insulating materials have a higher volume resistivity, where current flows is greatly decreased. Heat shrink tubing may use fluoropolymers or other insulating materials, where a higher volume resistivity is desirable. The AS23053 standard specifically guides testing and evaluation of a material’s volume resistivity.
Test Method
The AS23053 standard references ASTM D876 “Standard Test Methods for Nonrigid Vinyl Chloride Polymer Tubing Used for Electrical Insulation” for volume resistivity test procedures. ASTM D876 calls for a heat shrink specimen (approximately 300mm) to be shrunk around a specific sized mandrel. The specimen is then tightly wrapped in foil (approximately 150mm) acting as the external electrode. In addition to the primary electrode foil, there are grounded guard electrodes in place to reduce electric field edge effects that can skew the test results. The specimen is then connected to a 500V DC power supply and the power is applied for 60 seconds, after which the current through the specimen is measured.
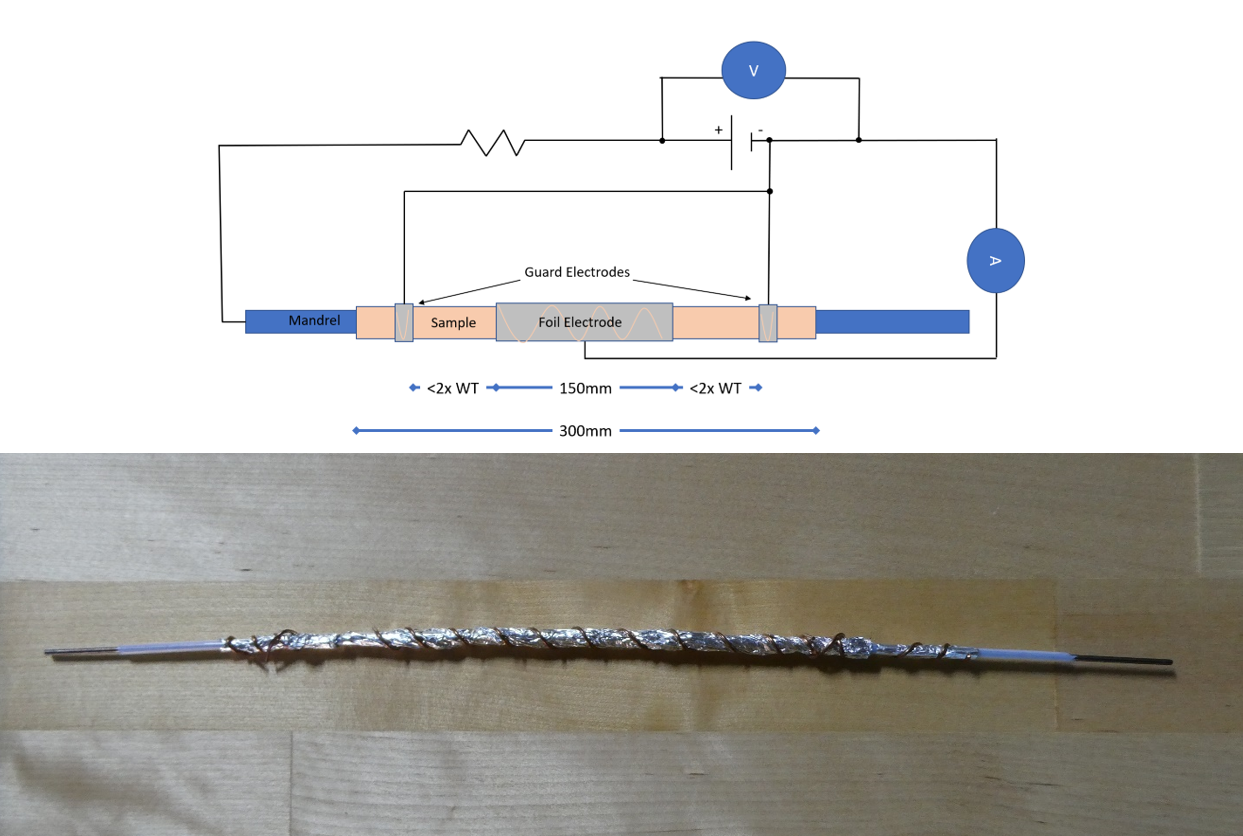
The reason for the 60 second duration is that the system is setup much like a capacitor. When the power is first applied, there is a small current flow as each electrode (the metal mandrel and the external foil electrode) builds up charge. At high resistance values, this charge buildup takes a while to fall to zero leaving only the leakage current. This requires a stable power supply and very sensitive equipment for the current measurements.
Output
This test yields a resistance measurement through a material, the unit for volume resistivity is ohm-meter (Ω∙m). It may seem odd that ‘volume’ resistivity is only in a linear length, but the resistance is decreased by the electrode-to-electrode surface area and increased by the material thickness. While the ASTM D876 provides a guide for testing, the AS23053 provides values for specific heat shrink material properties.
The AS23053/12, for reference, has a requirement for the volume resistivity to be a minimum of 1*1018 Ω∙m. This applies from the thinnest to the thickest single-wall AS23053/12 heat shrink and must be met for product qualification.
Standard Gaps
One presently overlooked aspect of heat shrink specifications is to address the proliferation of dual-wall heat shrink tubing. The dual wall construction may be accomplished several ways including combining a higher temperature, shrinkable tubing with a lower temperature, meltable tubing. Some implementations of the dual wall construction include an adhesive layer that fills in any air gaps between the heat shrink layers.
This adhesive layer between some of the dual layer constructions should be included as part of the flammability testing in accordance with ASTM D2671. Right now, unless specifically tested, some products may include this adhesive layer without flammability testing. It is recommended that those seeking a dual wall heat shrink solution review the flammability test data from the supplier.
Beyond the flammability concerns, the additional layer of heat shrink tubing should help increase the volume resistivity of the material, but there are no current qualifications or requirements around dual-wall heat shrink within the parameters of the AS23053 standard. The specifications around the outer and inner walls are a good starting point, but guidance should be developed to support these product requirements.
Supporting the Wiring System
Heat shrink tubing is used throughout an aircraft’s Electrical Wiring Interconnection System (EWIS) and must withstand the stresses set upon it in the standard testing. Volume resistivity is just one of many properties that are evaluated while qualifying heat shrink tubing. Attention to the specific setup of the test and using high precision test equipment are necessary to capture the relevant data. For those looking to assess or qualify heat shrink tubing, Lectromec’s ISO 17025 accredited lab is here to help.