The arc track resistance test is a basic performance test for most aircraft power carrying wires. As with any component assessment tests, there are many ways to evaluate a wire insulation’s propensity for arc tracking. The European wet short circuit test standard, EN3475 Method 605, is one means to determine the arc track resistance performance of wires and cables. This article discusses some elements of this test, comparison between the test method and other common arc track resistance test, and advantages of this test.
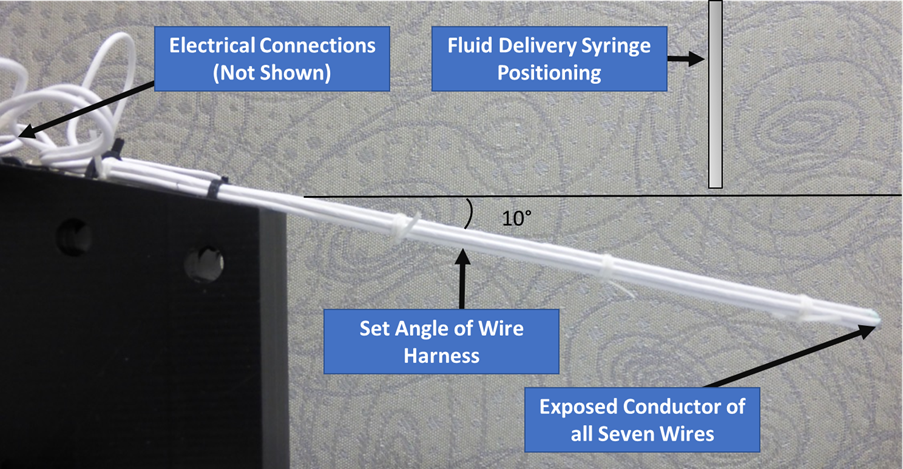
Physical Configuration
Prior to performing the wet short circuit test, a seven-wire test harness is prepared such that the conductors at the end of the harness are aligned in the same plane. With the wire ends aligned, the circuits are separated with a short air-gap.
As shown in the figure, the harness is inclined downward at a 10° angle. During test execution, a saline solution is dropped onto the wire harness, bridge the air-gap between the circuits, creating a conductive path between the circuit. The downward incline of the wire harness makes it easy for the saline solution to flow towards the open end of the wire harness.
The saline solution flow rate set such that there is sufficient fluid to initiate electrical arcing but not too high as to over-saturate the sample. Oversaturation with a conducting solution would prevent arcing because the solution creates a conductive path that can result in shorting and cause the circuit protection to trip.
Circuit Configuration
The EN3475 test standard calls for 18 trials to be performed with three trials at six different circuit resistance values. These in-line circuit resistance values are not specified by the standard, but the fault current (the possible current if the circuit is shorted to ground) is specified.
The EN3475 test standard does provide fault currents and recommended circuit protection ratings for several wire gauges that range from 10 – 26AWG. This addresses a gap in the MIL-STD-2223 and AS4373 test method as these methods only specify configurations for 20AWG.
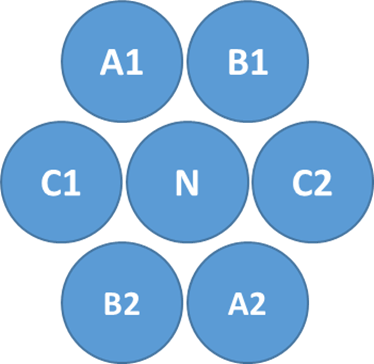
Test Performance
During the test performance, the 3-Phase, 115VAC 400Hz power is applied to the test sample, and a saline solution is dripped onto the wire harness. The most common occurrence is an evaporation of the saline solution and brief periods of scintillations or small arcs.
Regardless of the wire type or configuration, there are three possible test outcomes:
- Nothing happens – Less than 10 mm of the harness may be damaged/destroyed within the 2-hour duration limit.
- Shorting between wires – Welding and carbon tracking between the wires can cause circuit breakers to trip multiple times. This ends the test.
- Burn back and damage – The arc could damage/destroy the harness beyond the saline solution drip path. For wire with poor arc track resistance performance, the arcing can propagate for several inches destroying most of the test harness.
Does it Pass?
The pass/fail criteria for the test is determined by the damage length. This is indicated by the length of harness that is destroyed or damaged. The manufacturer’s detail product specification defines the pass/fail criteria for each cable size. Typically, more than 5cm of damage length would indicate a failure criteria.
Those familiar with the AS4373 arc track resistance test methods might anticipate other pass/fail requirements. Since the EN3475 Wet Short Circuit test involves a conductor exposed end on one side of the harness with terminals on the other, there is no method or purpose to test the insulation for breaches. The damage only occurs on the open end of the harness and burns toward the terminal end, therefore, only the damage length is considered.
Comparing to the SAE Methods
The EN3475 wet short circuit test initial harness configuration has a greater propensity for electrical arcing events than the SAE AS4373 wet test method. The test wire harness is prepared to arc more easily in the EN3475 test method since all wires have exposed conductors at the end of the harness (in the AS4373 the insulation of two wires is pre-damaged). Furthermore, the EN3475 test method features six powered wires whereas the AS4373 wire harness is configured with only five active wires and two non-grounded “floating” wires. Since the EN3475 test method better facilitates the initiation of electrical arcing than the AS4373 standard, the EN3475 test calls for a maximum test duration of 2 hours instead 8 hours as specified in the AS4373.
For more information or to discuss your needs, please contact Lectromec