The first meeting of the 8A and 8D committees for 2017 was held in Kissimmee Florida in April 2017. There were several topics discussed and voted upon that will have an impact on future wire component and system designs (previous article on SAE 8A/8D committee meeting available here). One common theme in the meeting was the need to address high-voltage component and system level requirements. This article will highlight this, as well as discuss the upcoming changes to the wire and cable design and installation standards.
High-Voltage
High-voltage power is an area that is being addressed across several of the SAE committees; and a combined session was held between the power systems and electrical component committees. The basic idea was that the power generation is increasing the supplied voltage therefore creating a need for the electrical wiring interconnects systems (EWIS) to have components designed to sustain these higher voltages for the entire length of the aircraft life. Just as you would not expect a connector to operate in a 300°C environment if it is only rated to 150°C, a connector should not be expected to perform perfectly with voltages that exceed its voltage rating.
At this combined session, the committees involved in power systems, connectors, wires, and system installation, came together to identify where the challenges exist. The first challenge that exists is to determine the delineation between low and high voltage system. For those in the utility industry, high-voltage power systems involve systems that are tens kilovolts. In the aerospace industry, this argument currently is whether high-voltage should be defined as voltages above 300 V or above 550 V. The reason for this discussion is that the current design for many of the EWIS components have only been tested in power systems views up to 115 V AC or three-phase power with a voltage difference of 208 V. Systems that use 270 V or greater now must rely upon custom solutions.
The argument for going to a higher voltage in terms of setting the threshold at 550 V is that 540V are already in use in multiple systems that are flying. By setting the bar at the 550V level, the committees can start to look at identifying and developing specifications and component configurations that can meet the challenges of systems that go beyond this.
High-Voltage Degradation
One of the presentations given during this combined session was from WL Gore and Associates describing their research on the impact of higher frequency power systems. This presentation specifically looked at the impact of higher frequency power systems on long-term longevity of wire insulation. Their research found that there was an inverse relationship between the power frequency and the time to failure for the wires they tested. This would suggest that the rate of change of voltage has a significant impact on dielectric performance and longevity.
When considering this with the push for pulse width modulated (PWM) power systems, this suggests that the use of PWM technology will greatly strain the electrical components. The PWM technology rapidly turns on and off a DC power source to a load in order to maintain high precision control of the component. As these systems typically involve higher voltage (e.g. 270VDC), the strain on the electrical components for the rapidly changing power can be great. It would significantly benefit those using PWM technology to evaluate the wiring and other electrical components before simply installing them.
Changes to AS50881
As with any time the AE –8A committee comes together, there was a discussion on several changes regarding the AS50881 standard. One of the changes that is of interest, was a recommended change on smooth surface wires and cables. The change that was proposed was to avoid using PTFE/polyimide smooth surface constructions in which a tin-plated copper conductor is used. The reason for this recommendation is that the sintering process used to create the smooth surface insulation adversely affects the performance of the conductor or shield in the case of cables. The investigation taken on by the U.S. Navy found that this high temperature processing can promote inter-metallic growth which can impact solder ability, contact resistance, and tensile strength when crimped.
Use of Connectors
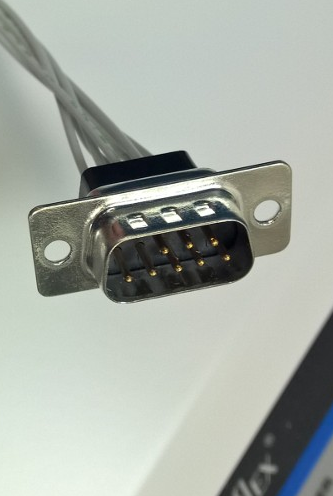
One issue that plagues the EWIS community is how to interface some aircraft of equipment that use D-Sub connectors. A lot of experience that has been gained has found that the use of D – sub connectors is not ideal for aerospace applications. The reason for this is that these connectors are not well suited for the environmental conditions in aircraft. While the D – sub connectors are cheap and easy to install, there are issues, such as a lack of accessories to control strain and environmental influences (like fluid ingress). Part of the committee discussion was focused on the best way to handle avionics equipment designed to have a D-sub connector interface.
Conclusion
A lot of the work that is being done in the aerospace wire and cable community is focusing on addressing the needs of upcoming higher voltage systems. What form these take still remains to be determined, but it is coming. It’s only with communication at the committee level with designers and OEMs, will it be possible to create components that are reliable, that have been tested for performance, and will be able to endure the full-service life on the vehicles in which they are installed.