Power transfer through aircraft or any electrical system requires components that have the capability to turn on and off. These switches, contactors, transistors, and electrical relays that route power through the aircraft are life limited parts. Whether from a design or sustainment view, understanding how these components degrade over time and what to look for when they do, ensures high system performance and long-term reliability.
This article evaluates some of the characteristics of mechanical relays and factors that should be considered when selecting them and their limited life.
Relay Basics
The fundamental relay design is an electromagnetic coil that activates when a current is passed through it. This electrical current causes an armature to move creating a circuit between a pair of contacts. The complexity and design of these relays and number of circuits controlled varies from relay to relay, but all function under the same basic properties.
Often relays are activated by low current low-voltage circuits to power higher current higher voltage circuits. Depending on how these are used in circuit design, they can provide a weight savings by avoiding long unnecessary runs for heavy gauge wire.
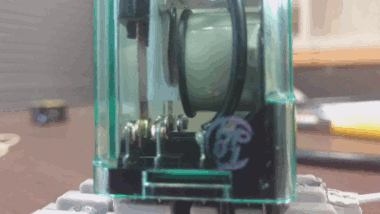
Relays have been on aircraft for decades in one form or another and because of the continued questions for a more electric aircraft, they will continue to be used. Progressively, these will be replaced by solid-state relays, solid-state power controllers, and other transistor-based technologies.
Life Limiting
Relays are both electrical and mechanical devices and can wear out or fail due to degraded the performance in either. The expected life of common relays is about 100,000 resistive load cycles unless otherwise specified. As a relay is cycled, the armatures, springs, and pins fatigue. The electrical contacts, typically nickel or gold plated, begin to wear and corrode leading to increased resistance between contacts and less electrical energy transfer. The poor connection creates more resistance and more heating, thereby accelerating the component degradation. Eventually the contact resistance increases to point of an open circuit or the contacts heat up and become welded together.
Stressing a Relay
Before fielded, relays must be tested for performance; one method for assessment is outlined in MIL-PRF-83536. The life cycle test method suggests running a relay through a series of tests with a variety of electrical loads including: resistive, motor (AC and DC), inductive (AC, DC), lamp, low level, and mixed loads.
Load Type |
Details |
Resistive Load |
The load resistance is set to match the contact rating. The relay is cycled at 20CPM. |
DC Motor |
The relay shall be subjected to the minimum operating cycles for making six times the rated motor load at rated system voltage; carrying and breaking the rated motor load. |
AC Motor |
The ac motor load test shall have an AC inrush current five times rated motor load current. |
DC Inductive |
The relay is subjected to a three-part procedure where an inductor is mounted in “normal operating position” and the load circuit is energized through a bounce-free contact from a power supply regulated within 5% of the specific rated voltage. The time is measured for the current to reach 63% of its final value. The DC inductance is calculated as L=Rt. |
AC Inductive |
AC inductive loads consist of inductive and resistive elements with .7 lagging power factor at the voltage and frequency specified in accordance with the applicable specification sheet. |
Lamp |
The relays are subjected to 12 times the rated lamp load and breaking the rated lamp load with a duration of 15ms to 20ms, with the total "On" time of 5 seconds and an "Off" time of 5 seconds. |
Low Level |
The minimum cycle time is 10 times the maximum specified operate/release times. For latching relays, the minimum cycle time is 2 times operation time. Each contact load is 10-50 μA at 10-50 mV (DC or peak AC). The coil is energized at rated voltage during 50% of each operation. |
Mixed Loads |
For mixed loads, the relay is subjected to 50,000 cycles. Tests on normally open and normally closed contacts are performed concurrently with at 28VDC test voltage. During each cycle, the relay coil is energized for 29 seconds and de-energized for 1.5 seconds. While the contacts are carrying the test current, the contact voltage drop measurements are made at the start of the test. |
From this, one should expect a relay’s longevity to be dependent on the type of circuit it powers. Changes in the circuit design type of equipment attached, and/or the current to draw can have a noticeable impact on the performance. This should be considered when determining the life-limit of a relay.
Integrating with EWIS
Whether selecting the relay for a new application or evaluating it as part of a routine Electrical Wiring Interconnection System (EWIS) components inspection, understanding what it is and how it is connected to the rest the circuit is important. Certainly, service histories can provide a great foundation for understanding pre-placement schedules of relays, but this can also be supplemented with thorough inspection and analysis. If it becomes possible to extend the service life of components by an additional two years without impacting the risk to the aircraft, should it not be done? This can provide an opportunity to save both time on inspection maintenance and on costs. To find out how, contact Lectromec. Our lab is ready to help you get the most value out of your aircraft electrical systems.