Corrosion prevention compounds (CPCs) are compounds that are placed on many aircraft components. Applied to a variety of mechanisms, these compounds have been found to increase structural life by reducing corrosion. While there are benefits to reducing corrosion, the impact of the CPCs on wire insulation and the aircraft Electrical Wire Interconnection System (EWIS) in general is not well understood.
Current CPC Requirements
Section 4.6.3 from MIL-PRF-81309G, the military performance specification on “Corrosion Preventive Compounds, Water Displacing, Ultra-Thin Film”, states the following with regard to testing of wires:
Compatibility with polyimide, wiring insulation. Approximately 24 inches (61 cm) of wire conforming to MIL-W-81381/11, shall be formed into a coil. Place the coil in a 4-ounce (118 ml) wide mouth jar and add enough corrosion preventive compound to the jar to completely cover the coil of wire. Cap the jar and store it at room temperature for 14 days. Repeat this procedure using distilled water as the test medium. At the end of the storage period, remove the coil and rinse thoroughly with tap water at room temperature. Suspend the coil and allow it to drain until completely dry. Each wire shall be wrapped tightly around a 0.125-inch mandrel and unwrapped slowly, noting the appearance and number of any cracks in the insulation. The wire shall meet the requirements specified in Table I. The wire shall be immersed in a 5 percent by weight sodium chloride solution and subjected to a one-minute dielectric test of 2,500 volts (rms).
Note that this is the only wire specification that is required to be tested in this specification that is not permitted on new military aircraft. There is nothing about ETFE, FEP, or other common wire insulation types. There is nothing about impact evaluation to heat shrink tubing, clamp cushions, or splices. Clearly, the existing standard needs to catch up with the modern EWIS.
Use of CPCs and Connectors
When using CPCs, it is important to ensure that the internal parts of the connectors (the parts conducting energy) are not exposed. Open connectors should be capped with the proper size cap to limit the ingress or exposure of CPCs. If caps cannot be located, the connector should be placed in a plastic bag and closed. The reason for doing this is that the CPCs can leave a thin residue on connector terminals, which can impede signal conduction or create high resistance locations, thereby limiting electrical current flow.
At no point should CPCs be sprayed into connectors with fiber optics as this can degrade the transmission through the connector. Although there is documented evidence that this is being applied in at least one platform, this application appears to be used as a bandage for a design error.
Examination of EWIS CPCs Effects
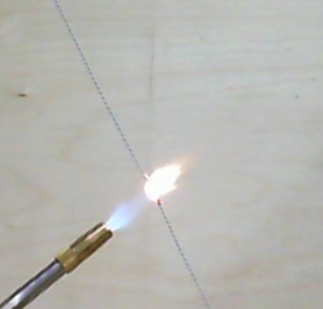
A project to be taken up by the USAF will try to determine the impact of CPCs on wire insulation and other EWIS components. Because of the different characteristics of wire insulations, it will become necessary to test all modern wire insulations. In case CPCs negatively impact one or more wire insulations, it will become necessary to quantify this and recommend that EWIS be protected during the spraying of CPCs or when compartments are fogged.
As a proactive measure, the Navy 505 wire installation and repair manual recommends against applying CPCs into the mating areas of connectors. Furthermore, the manual states that CPCs should not be placed on wire/cables as the contamination may degrade the wire insulation and performance.
Impact to the User
Although more data is necessary (and research results are pending), it is recommended at this time that EWIS be protected in any area in which CPCs are being applied.