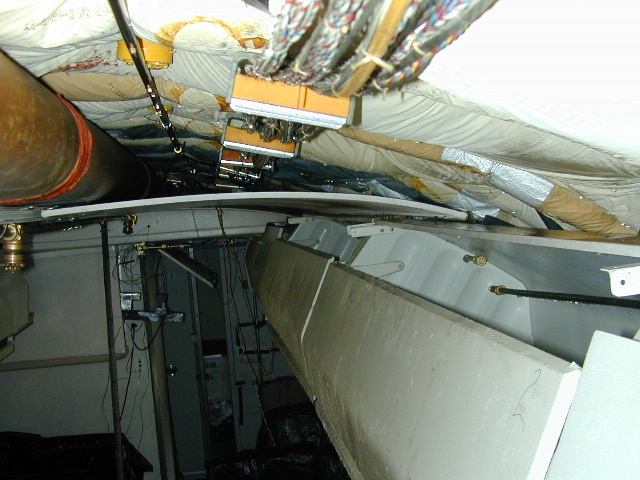
Every person flying on a plane has a reasonable expectation for safety when they ride on a commercial aircraft. Owners of transport vehicles also have a reasonable expectation to maximize their investment.
Starting in January of 2015, Lectromec begins a series of articles aiming to inform how to safely extend the life of commercial aircraft from the electrical wire interconnection system (EWIS) perspective, or what some would call EWIS Life Extension. Through this series, Lectromec will provide articles with a focus on scheduling EWIS inspection, a deeper dive into the inspection itself, and then a thoroughly detailed understanding of EWIS degradation and how it can impact the continued aircraft operation.
This article will give an overview of the 2008 Federal Aviation Administration’s guidelines for EWIS.
All aircraft are built and certified for a given service life. For those looking to extend aircraft use, they must recertify any aircraft that reaches the end of its designated service. This recertification means that the aircraft must show that it will be airworthy during its continued operation.
Recertification is of particular interest to operators who have an aged aircraft that has been in operation for the last 20-30 years and wonder what to do with it, especially when it has had a good service history and no significant problems. The decision to extend service life is made easier if the structures show little degradation, the interiors are in good condition, and the aircraft can still be flown economically. But what about an aircraft’s EWIS?
Structures, avionics, engines, and interiors are considered in such a life extension project. But there is also a need to examine the EWIS components. What must be considered here, as with crack growth on structures, is a degradation prediction that can provide a maintainer with the needed information as to when a component performance will decrease and create an unsafe operating condition.
Technologies such as Time-Domain Reflectometers (TDRs) are excellent at detecting broken wires and hard shorts, but they cannot tell much about the health of the wiring system. Relying solely on a TDR for your EWIS health assessment is like trying to tell the health of a person by only checking their pulse.
EZAP
Back in 2008 the FAA produced a set of EWIS regulations that included the aforementioned EZAP. The EZAP require that operators develop a plan for the continued EWIS airworthiness that includes regular EWIS cleaning and visual inspection to identify any degradation. The frequency of the inspection is based on the environmental conditions in the zone (e.g. fluid exposure, flammable/combustible materials, etc.) and it may range from a general visual examination once a day to close examination with a magnifying glass and flashlight once every D-check. This has been included into the ATA’s MSG-3 guide for “Operator/Manufacturer Scheduled Maintenance” Rev 2013.
Although a visual inspection will find points of chaffing, fluid exposure, and overheating, it will not find wire degradation. A thorough EWIS assessment cannot be done on the flight line as access to several locations within aircraft is necessary.
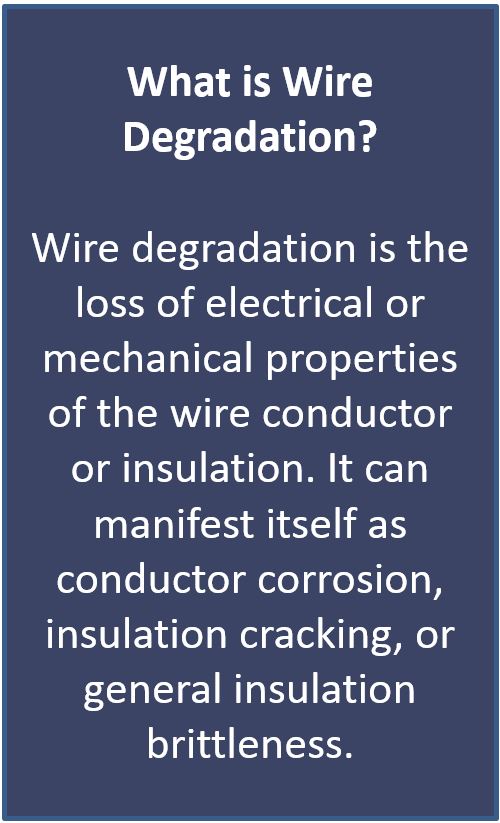
If a Service Life Extension Program (SLEP) is to be considered, then the obvious consideration for a full EWIS examination is during the performance of a D-check.
Steps for EWIS Examination
The steps for the EWIS examination can be expanded or contracted based on the particular needs of the maintainer/operator, but should include the following tasks:
1. Gather historical/maintenance data on EWIS
Find out the locations on the aircraft that are hotspots for maintenance. Lectromec will provide more details in future articles.
2. In-depth visual inspection
This should be based on an existing EZAP plan and augmented by Task #1.
3. Laboratory analysis
The EWIS components are removed from the aircraft and examined to determine the degradation. For many EWIS components, it is possible to provide projections on the remaining reliable service life.
4. Impact assessment
Depending on the laboratory results, the results may warrant the need to understand the impacted systems within a given aircraft location/zone. This will help to identify the impact of wire degradation on airworthiness.
5. Recommendations for Airworthiness
Once the data has been compiled, provide recommendations on sustainment/replacement of the EWIS components.
These steps can be scheduled to be performed in parallel with a D-check. When the D-check and the above tasks are completed, an operator has time to make a determination if the aircraft should be considered for continued service or should be retired from service.
Continuing
In future articles we will discuss the tasks in more detail, scheduling, and understanding EWIS degradation predictions and how they can impact the continued aircraft operation.