When testing aerospace wire, there are several test standards that might be considered; however, the one that is most commonly referenced is the SAE AS4373 “Test Methods for Insulated Electric Wire” which covers a wide range of mechanical, electrical, environmental, and workmanship tests. In this first article of a two part series, we describe the tests that are included in the method and how they can be used to determine wire performance.
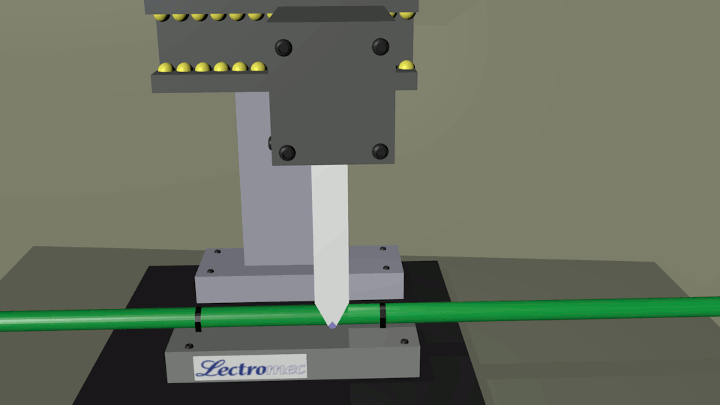
This is the first article in this series, the next article will be published the last week of January 2017.
Mechanical
Wires undergo a variety of mechanical stresses, which are dependent upon their installed application. To determine their performance, one or more of the following test methods should be considered for performance evaluations. The following is a listing of the AS4373 mechanical tests that stress the insulation, conductor, or both.
Test Method |
Test Name |
Short Description |
301 |
The specimen is placed under an oscillating jig simulating abrasion across a surface. |
|
702 |
The specimen is slowly wrapped around a mandrel at extremely cold temperatures. If no insulation cracks are found, then the specimen has passed. |
|
703 |
A blunt edge is pressed into the specimen until the insulation is breached. May be performed at ambient or elevated temperatures. |
|
704 |
The specimen is flexed until the conductor is broken. Important for high flex applications. |
|
705 |
Insulation Tensile Strength and Elongation |
The insulation is removed from the specimen and pulled until broken. |
706 |
A small cut is made in the insulation and the specimen is flexed. If the notch propagates to the conductor, the specimen has failed. |
|
707 |
Stiffness and Springback |
The specimen is flexed and the flex memory is measured. Important metric to determine workability. |
708 |
The specimen is wrapped on itself and heated. Any insulation crack constitutes a failure. |
|
709 |
Wrap the specimen and look for wrinkles in insulation. Particular application to tape wrapped constructions. |
|
710 |
Similar to Method 301, but examining the durability of wire marking. |
|
711 |
Durability of Wire Installer’s Identification |
The specimen is exposed to mechanical, thermal, chemical, and environmental stresses to determine mark durability. |
712 |
This test is typically used in coordination with other tests to mechanically stress a sample after environmental/thermal exposure tests. |
|
713 |
Circumferential Insulation Elongation |
The insulation is extracted from the specimen and expanded outward. Used to quantify insulation performance under radial stresses. |
714 |
Similar to Method 712. |
Electrical
Wires are designed to transfer electrical energy from end to end. Electrical tests are conducted to evaluate the wire’s capability to perform this basic function. The following tests are electrical tests that, for the most part, assess the electrical performance of the wire insulation.
One item to note here is that the following test methods do not cover anything that is related to signal integrity. Other standards, such as the AS6070 (*double check) is designed for signal application evaluation.
Test Method |
Test Name |
Short Description |
501 |
The capacitance per unit length of the wire is measured. (Article) |
|
502 |
The specimen is wrapped around a grounded mandrel and the applied voltage is slowly increased until corona is detected (corona inception). The voltage is then lowered to find the extinction voltage. Useful to determine voltage rating. |
|
503 |
The specimen is subjected to a high voltage pulse. No insulation breaches shall be detected. |
|
504 |
Also known as ‘volume resistance’, this measures the insulation resistance. Important for high impedance circuits. |
|
505 |
Assembly line style test where a high voltage is applied to the specimen as it is pulled through a grounded chainmail. Good for finding insulation breaches in spools of wire. |
|
506 |
Surface Resistance |
For most applications, the surface resistance of wire should be as non-conductive as possible. |
507 |
An electrical current is stepwise increased on a sample until smoke is visually detected. |
|
508 |
Mechanical abrasion of the specimen initiates an electrical fault to determine arc track resistance/propagation. |
|
509 |
A fluid is dropped on a pre-damaged specimen to initiate an electrical fault to determine arc track resistance/propagation. |
|
510 |
Most often used in combination with other tests. This test applies a high voltage to find insulation breaches. |
|
511 |
Wire Fusing Time |
A high current is placed on the wire to determine time to fusing (separation of conductor). |
512 |
Voltage Rating |
Still not defined. See here for a discussion on voltage ratings. |
513 |
Apply a current on the sample to reached target temperature. Visual detection of smoke shall be considered a failure. |
Review
The methods above provide the process for electrical and mechanical testing needed on aircraft wires to determine wire performance. The next article will cover the environmental tests, conductor, and final product quality checks that are included in the AS4373 test standard.