Arc flash is a problem for many industries; with increased demand for electrical power, arc flash is the likely consequence. To combat this growing hazard, most organizations have taken proactive measures to provide training to their staff in the proper way to protect against an arc flash. This training is the first line of defense in protecting from arc flash. But there are other consequences, such as damage to other equipment. How often is this investigated? This article provides a quick evaluation on what factors might need to be considered in the evaluation of the wiring system for facilities.
Ideally, a worker would never be near high voltage or high current equipment. The next best thing would be to limit the exposure to such areas. Although exposure to high energy areas cannot always be limited, intelligent design of the wiring systems can assist in limiting the potential hazards. When defining electrical systems and wire routing, the first focus of design should be limiting the potential hazard to people. Consider asking these questions:
- How easy is it for the wiring to be damaged by accident or careless error?
- If someone were to damage the wiring, would they know? (i.e. drilling through a wall)
- How often does the wiring get adjusted or moved? Is the wiring properly supported for this?
- Is the wiring accessible? Could someone visually examine the wiring if necessary?
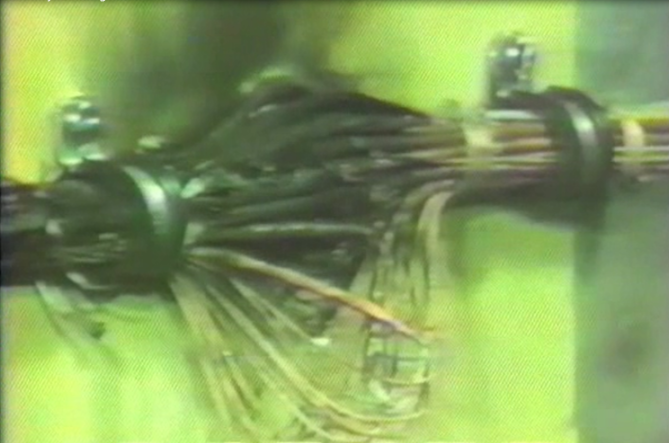
Unfortunately, there is never a shortage of incidents to choose from to show that electrical hazards cause harm. (After considering the human factors, the next goal of design should be to limit the potential damage to other systems).
- What systems are nearby? How would they be affected if they were also damaged?
- Is there enough energy in the case of an arc flash to damage the components for this system?
- If multiple systems were damaged, how would this affect the system reliability?
- If system reliability is affected, would this create a hazardous or catastrophic situation?
For most situations, the last question is not all that important. However in the case of a chemical factory or ship, catastrophic failures can adversely affect a large number of people. In the case of a factory, often there is a large amount of room for the wire routing to minimize such hazards. In contrast, ships have a limited space and the attention to the details of arc flash and the subsequent damage to systems is increasingly becoming a higher priority.
If you are interested in arc flash assessment, you may want to read Lectromec’s Wire Degradation and Looking in the Arc article.
While tools like Lectromec’s EWIS RAT (Electrical Wire Interconnect Systems Risk Assessment Tool) were originally designed for aerospace systems, the same analysis would be useful to those building or maintaining ships. Analysis tools such as collocation assessments can help identify where multiple systems are routed together. By combining this information with fault tree information (or system design principles), the user can identify areas where common cause failures could cause a hazardous scenario. Furthermore, by combing the electrical system information and the routing of nearby objects, the EWIS RAT is able to return the potential damage to nearby systems including hydraulic lines, fuel lines, devices, or structure (Lectromec has a wide range of experience with the investigation of arc damage from 400Hz systems). These analyses and others not described here (there are more analysis tools provided by the EWIS RAT), can increase not just the safety for personnel, but also increase system reliability for the vessel.