A couple of weeks back, we wrote the Wire Failure and Incident Investigation article that reviewed some of the characteristics of wire failure and the means to detect them in a post aviation incident investigation. That article focused mostly on the conductor failure mechanisms. The three failure mechanisms that will be covered in this article are:
- Insulation Fracture
- Thermal Damage to Insulation
- Conductor Discoloration
Insulation Failure
This actually covers a wide variety of aircraft wire failure mechanisms. The general idea behind the insulation failure mode is that through one mechanism or another, there is a reduction in the insulation dielectric strength.
This reduction in dialectic strength may be caused by:
- Mechanical strain stretching the insulation (as can be seen at locations with tight bends)
- Poor wire construction leaving weak points in the insulation (more susceptible to voltage breakdown or mechanical failure)
- Insulation degradation (exposure to higher temperatures or more severe environmental conditions)
- Chaffing (rubbing against another wire bundle or against structure)
More often than not, these types of failures (with the exception of chaffing) will have other indications of similar degradation elsewhere in the aircraft. Lab analysis of the wire construction and level of degradation are possible.
Thermal Damage to Insulation
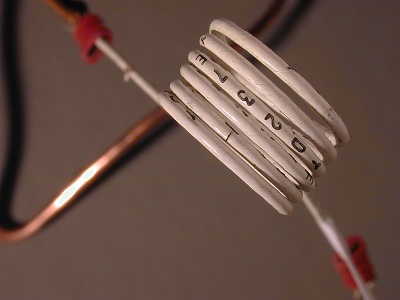
Thermal damage to the insulation can provide information as to the temperature, duration, and location of a failure event. Wire insulations have a low thermal conductivity meaning that the damage is usually restricted to areas near the heat source. The signs of thermal damage include:
- Gradual discoloration, usually darkening
- Loss of insulation flexibility and cracking
- Loss of electrical resistance (dielectric) properties
The thermal damage will start at different temperatures based on the polymer. Depending on the insulation, this can be as low as 105oC for PVC (not common on aircraft) or as high as 600oC for polyimide based insulations. The level of discoloration can provide information as to the temperature as well as the duration of the event. Some polymers will have a different insulation color based on the exposure temperature.
Conductor Discoloration
Conductor discoloration is another sign indicating exposure to high temperatures. More often than not, exposure to high temperatures leads to either conductor plating diffusion or chemical reactions that result in conductor discoloration.
For silver-plated copper conductors, the silver and copper will diffuse into one another at temperatures above 200oC. This is identifiable by seeing a reduction in the conductor surface luster. A similar process occurs with tin-plated copper conductors above 150oC.
Conclusion
These tips only provide a starting point for identification of wiring failure. Available power, wire gauge, wire specification, and environmental conditions are some of the other factors that modify the potential damage from a wire failure. To get to the root cause, sometimes it is necessary to recreate the scenario in a lab environment. Careful control and monitoring under laboratory conditions can provide insights.
Lectromec’s laboratory is equipped with a variety of power conditioning stations and environmental chambers to sufficiently represent the most common aerospace environments.