Most components for electrical systems will have an accompanying product specification or product information sheet. These information sheets contain a lot of information that include mechanical, thermal, and electrical performance and this information is regularly used by engineers to make technical decisions. This performance information is necessary to reduce engineering time and avoid the need to independently evaluate every single component.
However, is the right information being conveyed to the engineer? For example, many aircraft electrical components include a maximum voltage, maximum temperature, and component specific information (e.g. trip time for circuit breakers, DO-160 humidity thresholds, etc.). But is it possible that this information would be misunderstood and lead to improper engineering decisions?
Consider this: an example wire’s voltage rating is 600VAC with a temperature rating of 260°C. Should it be expected that the wire should have a long service life if it is constantly used at 600VAC in a 260oC?
To answer that question, we must first go through how components are tested.
Testing
When components are tested for qualification, the test is performed in such a way to evaluate a single element of the component performance. For example, when a wire insulation’s electrical properties are evaluated, such as insulation resistance, this is often at ambient temperature either on a virgin sample or after some stress, such as high temperature exposure.
The key here to remember is that the insulation resistance, and many of the other properties identified on product specification sheets, is not monitored or evaluated while the wire is under stress. It is perfectly rational to assume that the properties will change a hundred different conditions, but how much will it change is uncertain and nearly never provided with the product information.
Mechanical
One of the first properties to degrade is with mechanical stressing. For example, the standard testing for wire is performed at multiple temperatures, but for some wire types it is not. Lectromec has performed this testing and found as much as a 90% reduction in cut through performance between ambient to maximum rated temperatures.
As one would anticipate, as the temperature is increased, the mechanical performance of polymers degrades. But a 90% reduction suggests that nearly any mechanical compression of the wire (such as under an undersized clamp) at that temperature would result in failure. This is because when a wire is temperature rated the test requires only thermal exposure without mechanical stressing (full test information here).
Product Manufacturers
To the defense of the product manufacturers, there are far too many permutations of environmental and operational conditions to be shown on a product specification sheet. Many of the components that are produced have product sheets that contain a lot of information and should be used as a baseline for first round product selection which is then subsequently reduced through additional component evaluation.
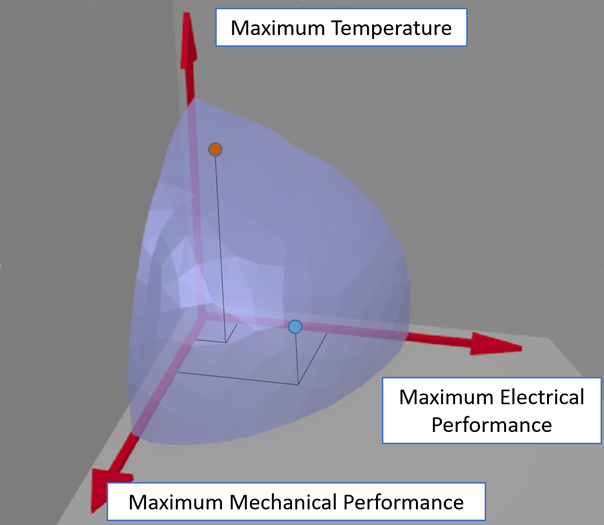
As highlighted in the previous section, it is important for engineers to know that the product performance information is often under idealize conditions. When placed in real world applications, it is necessary to derating the product performance to allow for the margin of error and for the safety factor.
Combination of Environmental Factors
A graphical representation of this is shown in the graphic where a given wire/cable has maximum performance criteria for a combination of operational environments. In the figure, we see two example configurations.
Figure Location | Description of Performance | Representative Location on Aircraft |
Orange | Cable with a more limited mechanical electrical performance but a very high maximum temperature rating. | Cable routed in a high temperature environment that is electrically derated and it has been derated such that there is less current on the circuit than would be in a lower temperature environment. Further, to prevent insulation degradation, the cable’s movement is limited through additional clamps and harness protection. |
Blue | More mechanical and electrical performance is desired than the orange configuration, but the maximum operational temperature of the wire is limited. | Cable is used for a high current application, but placed in a relatively benign environment |
In both the orange and blue dots indicate maximum long-term reliable performance for the component for a given set of environmental conditions. As such, the maximum performance criteria for any electrical component should be considered as a combination of multiple factors. To go beyond this would reduce the overall service life of the electrical component. This is perfectly fine, however, this should then be associated with life limiting and having this addressed as part of either an EZAP program or instructions for continued airworthiness (ICA).
Conclusion
While product information sheets often contain a lot of good information, the information needs to be taken with the knowledge that it is gathered from a particular set of tests. It is often necessary to do additional evaluations to ensure that the product is proper for the desired application. This is not necessary if the product is being used in scenarios well below the limits to which it specified, but as the product is used closer to those limitations it is better to evaluate during design them before use than when the product is in the field. Lectromec can help you identify the best product for your application. Contact us to find out more.