The SAE Wire Installation Guidance document, AS50881, provides guidance on considerations for designing an aircraft wiring system. In this article, we examine sections of the AS50881 and discuss how each of these sections should be addressed and what factors should be considered when designing an aircraft’s Electrical Wire Interconnection System (EWIS).
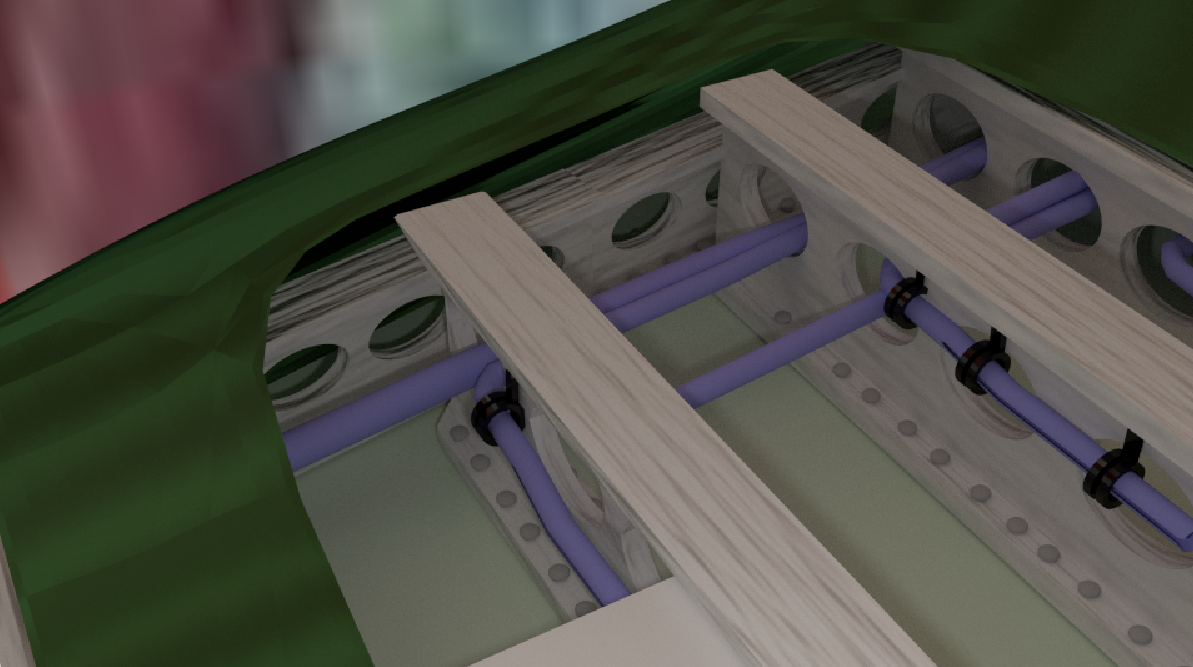
Like many other aircraft systems, the maintainability of the EWIS is critical to airworthiness. In AS50881, a single sentence is provided to describe how sustainment should be factored into the EWIS design. It reads:
Wire selection shall be affected by considerations of the types and frequency of maintenance actions.
This single sentence has broad implications. So how does one show that the wire selection has been done to take into account these “considerations”? That will vary from project to project and client to client, but there are several factors that do not change regardless of the project or client specifications and must be considered to achieve the goal of maintainability compliance.
Harness Protection
Secondary harness protection materials are those materials that are placed over a harness to protect it from external damage. Secondary protection may be needed for various reasons, such as moisture protection, to prevent/limit damage during operations, and/or chafe protection. Wherever the secondary harness protection is installed in the aircraft, it is critical to remember that the harness protection materials are life-limited parts and, ideally, should not impact the EWIS maintainability. Chafe protection materials, if applied in areas where chafing is to be expected, require to be considered as life-limited parts or at the very least, need to be able to remain intact without wearing through between a maintenance cycle.
Furthermore, if a harness is protected by a secondary protection, and the maintenance procedure in the maintenance zone calls for visual inspection, the visual inspection should include a specific line item for evaluating the component’s mechanical wear.
Automatic Wire Test Set (AWTS)
With automated testers becoming more central to aircraft sustainment activities, how should their use affect or define maintenance intervals? If a harness is regularly checked with an automated tester, then it may help to justify the selection of a cheaper/lighter wire type with lower performance characteristics (e.g. less scrape abrasion resistance, lower operational temperature, etc.). The caution here is that if the choice is made to go with a lower performance wire for the goal of saving money, the money may well just be spent on the development of wire test protocols and test equipment (listen to a podcast on AWTS).
Further, if the AWTS style system is part of the vehicle maintenance plan, then the EWIS design should incorporate changes that would accommodate the use of AWTS. For example, connectorized EWIS design will maximize the usefulness of AWTS evaluations.
Accessibility
The accessibility of EWIS components will undoubtedly be based on where the wires are installed in the aircraft. Those areas that are less accessible (e.g. areas that require the aircraft to have significant down time and lots of equipment removed and/or possibly structure), must have the wire selected such that they are, in effect, performance excessive for the location. The idea here, as with most of the aircraft design, is to minimize risk. By reducing the likelihood of failure by selecting an ‘over-qualified’ component, the potential failure or damage between maintenance cycles is reduced.
Defining the EWIS Inspection Interval
The best guidance that exists today is the FAA’s Enhanced Zonal Awareness Procedure (EZAP) program. This process was developed by the FAA to help designers and maintainers define inspection intervals. Each of the factors discussed above are included in the definition of maintenance intervals, as well as severity of failure. For those with more OEM risk data (e.g. fault trees), a more in-depth failure severity analysis can be done (an analysis that Lectromec’s EWIS RAT can perform). For after-market modifiers and MROs, the EZAP process provides excellent guidance on what factors should be considered when deciding on the appropriate maintenance intervals: fire zones, cargo areas, and fuel line routing.
The combination of maintenance intervals, EWIS design, and component selection should be done such that the aggregate risk between inspections is limited.
Summary
The AS50881 does provide a wealth of lessons learned and key recommendations when designing an EWIS. However, given the concise language, the implementation and key factors are often not specific enough and need additional clarification. If you would like more information on EWIS system design please read Lectromec’s Wire Selection Testing article.