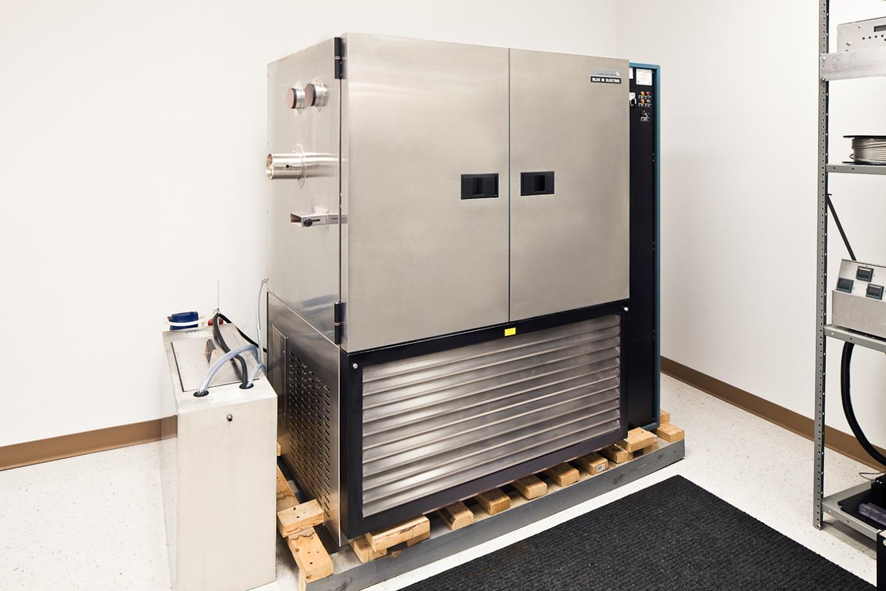
The hundreds of wire tests that exist for aircraft wire and cable can be categorized into five groups: environmental, electrical, mechanical, chemical, and thermal. In this series, we will look at common tests within each of these categories, what they are, how are they performed, and what the results mean.
From an environmental exposure test perspective, one of the more common tests for aircraft wire is humidity resistance. These wires will be sitting in the aircraft for 20-30 years. There is going to be a fair bit of moisture exposure during that time, particularly for those that connect to wire harnesses in the wheel wells or on the leading or trailing edge of the wings. The tests for humidity resistance of EWIS components have been around for decades. The last major change stems from issues identified with moisture-related polyimide wire insulation degradation in the 1980’s, which led to additional test requirements for humidity resistance assessment of wires. (Note: significant material improvements have been made on polyimide insulation humidity resistance since the 1980’s.)
In this article, we discuss two particular wire assessment test methods that are used to evaluate the performance of all types of wire insulations in humid environments.
Cycling
Ideally, a humidity test would be performed to best represent the aircraft conditions in-service. But doing so would take 20 to 30 years to generate all the data necessary. To avoid having to wait so long, the alternative is to perform accelerated aging tasks, which include elevated temperature and humidity conditions. By creating more harsh environments in which the samples are tested, it is possible to predict the performance of the wire for its in-service life.
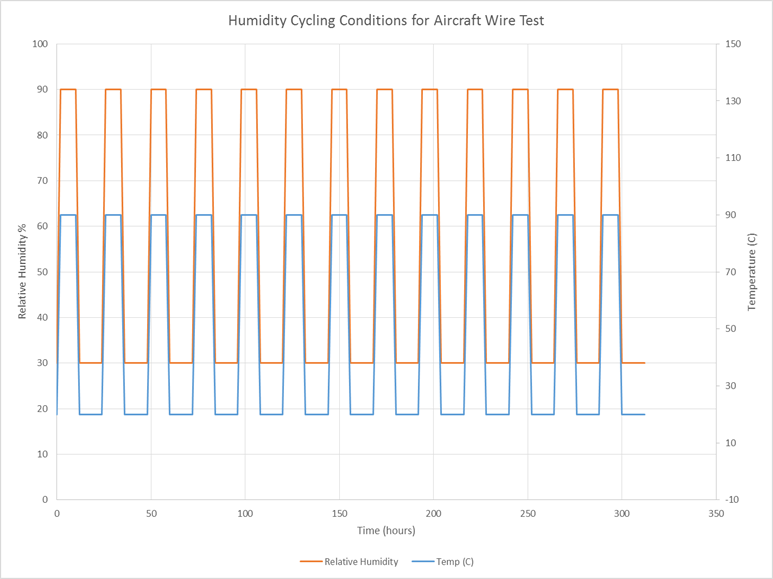
There are several standards that provide guidance on how to perform accelerated humidity resistance aging. The first of these is the temperature and humidity cycling and is included in aerospace industry standard AS4373. In this test method, the sample is placed into a humidity chamber and the temperature and humidity are increased over a couple of hours. The humidity chamber conditions are maintained for several hours, then cooled back to ambient. After 8 to 10 hours, the cycle repeats, with the temperature and humidity increasing again.
This cycle is repeated for a dozen or more times as detailed in the specification. At the end of the exposure cycles, the sample is then pulled out and exposed to a variety of electrical and mechanical tests to determine if there has been any degradation of the wire insulation. Failure is often determined by a significant reduction of insulation performance (insulation resistance) or mechanical degradation (cracks, breaches, etc.). No tests are performed on the conductor in this type of assessment.
Forced Hydrolysis
Another type of humidity resistance test is the forced hydrolysis testing, which is included in AS4373. In the forced hydrolysis testing, the sample is tightly wrapped around a mandrel and submerged in high temperature water. The ends of the wire are maintained above the waterline for thousands of hours. Once the sample is removed from the water bath, the insulation is visually examined and mechanical and electrical tests are performed.
Space Vehicles
The two test methods that we discussed above are more important for aircraft than for space vehicles. Still, they can be useful for spacecraft as well. For example, before the completed system is assembled, the components rest in facilities for months or years awaiting for final assembly (although, for the most part, they are kept in temperature-controlled environments). Given this, there must be some level of humidity resistance of the equipment, or at the very least, it should be considered as part of the virtual design.
The severe conditions mimicked by the forced hydrolysis tests are not nearly as likely for spacecraft. Therefore, other types of tests, not focused on humidity, are likely to be more important from an in-service condition assessment. Future articles will discuss elevated temperature assessments, mechanical suspense, and other tests that may be important for spacecraft applications.
Lectromec has the capability to perform both of these tests. To find out more, contact Lectromec.