Today Gregg Turcich sat down with Lectromec to discuss the topic of aircraft secondary harness protection, or what some call aerospace protective sleeves. Gregg is certainly qualified to talk about these topics because he has a degree in chemical engineering and decades of experience in aerospace technology.
Gregg enumerates the four kinds of protection that his company’s protective sleeves accommodate. These include chafing, fire, thermal, and Electromagnetic Interference (EMI). He sees increased concern in the area of EMI in the aerospace community today. During the interview, Gregg talks about his experience with a wide range of materials include the synthetic fluoropolymer Polytetrafluoroethylene (PTFE). This is the commercial product from DuPont known as Teflon.
One intriguing comment Gregg made involved some of the concerns with manufacturing components for aerospace secondary harness protection. Environmental concerns are altering the materials that companies like Federal-Mogul use to produce products. This is a world-wide concern, especially for fire retardant components.
Gain insight into aerospace wiring, listen to the short 16 minutes interview.
Transcript below:
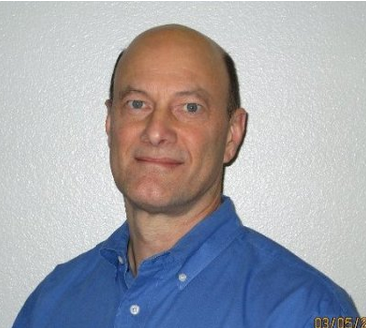
John: Welcome to the Lectromec podcast with John Gilroy. Lectromec provides you with the turn-key solution for aerospace wiring assessment, testing, and certification. The purpose of this podcast is to keep you informed of trends in the rapidly changing aerospace industry. Today’s guest is Gregg Turcich. He’s the EIT Sales Director for Federal-Mogul. Good morning Gregg, how are you today?
Gregg: Great John, thanks for calling.
John: You’re up in New England, it’s August has it started to snow yet?
Gregg: Not yet, but I’m sure it’s not far off.
John: You got your snow boots in the hallway there for later on today. Huh?
Gregg: Right now we’re getting rain.
John: Yeah. Gregg, our audience may not be familiar with you, could you tell our audience a little bit about your background, and how you wound up working for Federal-Mogul?
Gregg: Sure. I graduated from Drexel University in Philly with a chemical engineering degree and went to work for a company called ICI where they were making PTFE resins or what other people know as Teflon. We used a different trade name and a lot of PTFE resins end up in aerospace applications. I started doing some technical service and moved into technical sales with ICI. Then went to work for a company in New Hampshire. That’s how I ended up getting up here in New Hampshire. They made materials that went on wiring, insulation materials using PTFE and things like that. Then I ended up at Federal-Mogul back in 2003.
John: I’m here in Washington DC, the Federal Government head and I saw Federal-Mogul, I thought to be down the street from us. Tell us about the origin of that kind of funny name, a split name or merger, or how did that happen?
Gregg: It’s a very old company, it started in like 1893, or something.
John: Same year I was born.
Gregg: I guess you’re doing well then.
John: I’m doing pretty well.
Gregg: You’ve been eating right.
John: 1899, wow, been around a while.
Gregg: Yes, yes. I actually don’t know the origin of the name to be honest. The group that I’m with which is known as Bentley Harris, that’s the trade name we use, it was a company that started in 1923 in Pennsylvania. They were acquired by Federal-Mogul in 1998, so that’s how we became part of the Federal-Mogul family.
John: Companies don’t stay in business that long with luck. They stay in business that long by being innovative and keeping up with trends, and responding to customers’ needs. I think that’s the whole idea with companies that respond to the needs of people in the aerospace industry. And that leads into the topic of our subject today, is that, some of the listeners are very familiar with you, and your company, and your products. Some may not be familiar with secondary harness protection materials. Could you give us just a brief summary of what they are and how they’re used?
Gregg: Sure. We make, as you said, secondary harness materials, or what we refer to as protective sleeving. There’s basically 4 applications, general applications, so it’s used for chafe and abrasion protection, that’s probably the primary one. Then, fire protection, thermal protection, and then EMI protection. If you got issues with any of those 4 types of problems, we have a solution. Typically, or historically, they were tubular and typically textile-based. Over the last 20 years or so we’ve moved into it all being what we refer to as open solutions, so instead of having to pull it over top of the harness this is basically open down the side and its ease of insulation, it’s very flexible. It’s one of those things where a lot of people are familiar with peach ring type products, they tend to go on to protect against chafe and abrasion but they tend to make a very stiff harness once you heat shrink them. With our products they’re much more flexible.
John: Yesterday I did an interview with a vice president from a company called Inmarsat they have a satellite going out here on August 28th I think. Maybe some of your products are in that spacecraft too?
Gregg: Yes, we’re pretty much on quite a few platforms. Like I said, we’ve been … The Bentley Harris part of Federal-Mogul has been around almost as long as Federal-Mogul. A lot of protective sleeving going into almost all aerospace applications. John: Many of the readers of the blog at Lectromec are application engineers, what do you think they should know about secondary harness protection or protective sleeving?
Gregg: As I mentioned, we typically are there to solve problems. Obviously in aerospace applications you want to put in the least amount of weight into the aircraft, so you don’t want to use our products unless you have to. If you look on some of the fence industry, like the J Swag group, when they put together a pie chart of faults that they have in the system, chafe and abrasion issues are pretty high in that pie chart. Typically you’re going to use it where you have potentially coming against [inaudible 00:10:14] abrasion where you’re coming against other parts of the aircraft, where the materials bending, or is flexing. From chafe and abrasion that’s sort of the main focus. EMI’s become real big in that few years and that’s been a focus of ours for the last 10 years.
John: From the perspective of an application engineer, give me an example of secondary protection that may not be a good fit. Gregg: Again, as I just said, the only thing … Again, you don’t want to add anything you don’t need. In a case of say the wire bundle running along the main body of the air frame, you won’t find any chafe an abrasion protection, or secondary protection. For instance, we sell fire protection it goes on the hose and tubing area and that’s there as a secondary protection to make sure, for instance, the hose doesn’t leak if there’s a fire. If the test is actually a 15 minute fire test where they put the hose in a 2,000 degree flame, they vibrate it, they pressurize it with hydraulic fluid for instance, and that hose cannot leak for 15 minutes. Without some of our products on there that hose it wouldn’t meet that requirement.
John: Tell me Gregg, what are some of the latest advances in protective sleeving?
Gregg: We’ve really, like I said, historically they will have the products be tubular so they have to put it on typically when you’re building the harness. You would have to put it on before you pin out the connectors on your connector. We came out with open “wrappable” in the last 10 year, 20 years, but really an aerospace 10 years. It makes for easy installation, it can be put on after the fact.
John: Gregg, you talked about a 15-minute test for heat, I think. I mean, how do you test something for EMI?
Gregg: EMI is one of those things historically it’s a little bit of a black art. Things have gotten much more rigorous obviously, over time. We run what’s known as a transfer impedance test, it’s a tri-axial test method, and it’s still, it’s one of those things where we ask the OEMs for their requirements and sometime we get a little piecemeal information. We’ve done enough work over the last ten years in EMI that we generally know what’s required in commercial aircraft as far as what the R0 needs to be, what the transfer impedance curb needs to look like. There’s other methods but typically that seems to be the one that everybody’s gelling around is this transfer impedance.
John: Everyone has technical challenges. We just had a technical challenge with the internet here. What are some of the challenges that you face with your products.
Gregg: Today, obviously, lightweight. That’s always a trend. Lighter weight materials. There’s always something new, a lighter weight product out there. The challenge is always cost. With lightweight typically there’s a cost penalty. We also try to balance giving the best performance with the best cost. That’s the challenge, it’s typical engineering. You always have a balance and you have to find that right balance. You can spend a lot of money and get something but can you sell the final product. That’s always the challenge in most engineering technical issues.
John: You know Gregg, you’ve got a lot of experience in this industry, you have a technical degree. You’ve seen a lot of things, you can probably forecast things and see what’s going to happen in the next five to ten years here. Where do you see the industry headed?
Gregg: I think some of the problems, and you mentioned a challenge, the one thing I forgot to mention that’s been a big challenge of the industry over the last few years is all of the environmental requirements, with Rojas and Reach coming into play. Materials have become more difficult to get. Some of the flame retardants that we used to use are no longer available. I think that trend’s going to continue. I think we’re always looking for products that are inherently flame retardant rather than having to add a flame retardant. I think that trend’s going to continue. I think we’re going to continue to see more EMI requirements on aircraft as they move towards more composite materials. Again, the lightweight thing is always going to be an important feature in aerospace.
Did You Know? Lectromec’s EWIS component test lab is an ISO 17025:2005 certified facility. Lectromec has a wide range of wire and cable testing services.
John: In a competitive situation, if you’re competing with a company in Germany or France, just pick a country. Do they have to encounter the same kind of environmental restrictions as you have to.
Gregg: Yes, actually. A couple of those things that I just mentioned, Rojas and Reach, really have been driven by the European Union. Then they sort of seem to permeate through the rest of the industry. For instance there’s a deck of BDE brominated flame retardant that we use that was originally banned in Europe. We could continue using it here, however, over time the EPA came to agreement with the manufacturers of that flame retardant and they stopped producing it. Even though it’s not banned here in the States, the manufacturers are not producing it so you can’t get it. You have those kinds of things. It’s really, if you’re going to sell an aircraft across the globe, you’re essentially having to meet global requirements these days. That’s becoming a definite issue.
John: I think someone like you has to attend industry meetings, not only in the United States but all throughout the world. It’s a flat world for you isn’t it. You’re competing with everything that’s going on, everyone in different time zones, it’s got to be a challenge to keep up with all the new trends.
Gregg: That’s for sure, luckily for me, I actually just took over the global responsibilities. Up until six months ago I was just covering North America.
John: Just North America.
Gregg: Yeah.
John: I just played first base, second base, and third that’s all I was going. Now you have to pitch.
Gregg: But now, globally, there are industry groups both in Europe and the US. Obviously the Chinese and the Russians are trying to be more of a player in the commercial airspace market, there’s activities going on there. There’s a lot of things going on around the globe, that’s for sure.
John: I have to tell you, I had an appliance repair guy come over to my house, I was talking to him. He talked about his favorite airplane, “My favorite aircraft is a 707.” He went on and on why he liked it. It was his hobby. People have hobbies in doing that. You’re a professional in the industry so I’m going to ask you the same question I asked the appliance repair guy. Okay, Gregg, you’ve been in a lot of planes, you’ve seen a lot of things, what is your favorite aircraft.
Gregg: That’s an interesting question. If you had asked me six months ago, being I was just North America, I would have said the 787 because we had the most content on the 787 of any commercial in aircraft. However, today, since I have global responsibilities, we actually have more content on the A350.
John: Ah, the correct answer.
Gregg: Yes, yes. Reality if I had my choice it would be a Gulfstream G650.
John: Is that one of those executive jets.
Gregg: Yep.
John: Wow.
Gregg: Yeah, if you have an extra $65 million John we can go out and get one.
John: I have some spare change in my pocket here. I’m sure I’ll just buy one this afternoon.
I’d like to thank my guest today, Gregg Turcich, who is the Global EIT sales director for Federal-Mogul. Thank you, Gregg.
Gregg: Thanks, John.
John: And thank you for listening to the Lectromec podcast. If you would like to learn more about aerospace wiring, please visit our website at lectromec.com. We’ve got free white papers, newsletters, videos, blogs and much more.