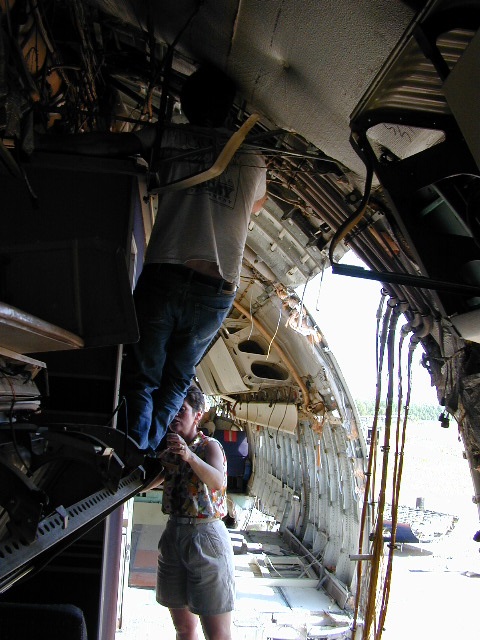
This is the third article on visual inspection of aircraft electrical wiring systems (Part I and Part II).This part of the visual inspection series focuses on the inspection of splices, especially regarding electrical wiring for aircraft. When it comes to examining EWIS, it is important to remember that splices are components that require the same care and attention as all other parts. Here are a few points to keep in mind when inspecting splices in harnesses:
1. Splices should be staggered in a harness as much as possible
Staggering of splices is recommended because it:
- Limits the increase in bundle size
- Reduces chafing opportunities in a given area
- Simplifies identification of a given splice in harness
2. Conduct location specific checks
- Verify that splices are not installed within 12 inches of a fuel tank
- Verify that splices are not under support clamps
- Verify that the splice is not installed in a high flexibility area of the harness
3. Crimps
- Wire should be flush with front of barrel
- Crimps should be on the side containing the inspection hole
- No part of the conductor should be outside the insulation sleeve (i.e. there should be no conductor strands poking out)
- If using an environmental splice, there should be sufficient sealant in the splice to close the splice
4. Additional items to note
- A wire should never, ‘feel loose’ in a splice. If this is ever the case, either recrimp or redo the splice.
- No discoloration is acceptable. If there is a discoloration of the splice sleeve, it can be an indication that the splice has not been crimped correctly and/or the splice is not rated for the environment.
This covers most of what is necessary to know before performing an inspection on wire splices. Of course, there are tools for checking the quality of splices, but the best tool is an experienced and knowledgeable technician.
If you are interested in electrical wiring for aerospace, you may want to read the article on Heat Shrink Tubing Applications and EWIS Components.