This is the final article on the series devoted to the FAA regulation 25.1707 on EWIS separation. The previous six articles in this series are listed below:
- Jan 20, 2014 Part I: Damage assessment for 25.1707
- Jan 28, 2014 Part II : EMI compliance in 25.1707
- Feb 7, 2014 Part III: Heavy Current Cables in 25.1707
- Feb 15, 2014 Part IV: Grounding and Power Separation
- Feb 21, 2014 Part V: Component Separation Guidance
- Feb 28, 2014 Part VI: Control Cable Separation
This last article covers section ‘j’ from 25.1707. This section states:
(j) EWIS must be designed and installed with adequate physical separation between the EWIS components and heated equipment, hot air ducts, and lines, so that:
(1) An EWIS component failure will not create a hazardous condition. (2) Any hot air leakage or heat generated onto EWIS components will not create a hazardous condition.
Similar to the last article, this section of the 25.1707 was broken out because of a unique set of challenges that must be considered as part showing EWIS design compliance.
The parts that should be considered include:
- The heat generated by the local equipment/air ducts
- The ambient temperature of the zone
- The heat generated by the wire harness
#1 – Generated heat
Nearby equipment and air ducts may radiate heat that can impact EWIS components. Although the constituent harness wires may be rated to a 150oC or more, the supporting ancillary EWIS components, such as splices, heat shrink tube, clamps, and harness sleeving my not be rated to the same temperature. Thus, it is important to consider all parts of the EWIS and their temperature ratings.
#2 – Ambient zone temperature
The local radiant heat can impact the harness, but so too can the local environmental conditions. Like all other components, prolonged exposure to elevated temperatures can lead to degraded performance. While this item is fairly obvious, it is important to also consider the resistive heating of the wires, which leads into the third item…
#3 – EWIS heat generation
A means for estimating a harness’s rated current carrying capacity (or ampacity) is included in AS50881. Along with charts 1-5 in this standard, a formula is included for calculating the current carrying capability of a wire harness with a variety of wire gauges. Based on data gathered generations ago, this is a good first order estimate on the maximum current for the harness wires to not exceed the wire rated temperature. Lectromec has made available a tool that can be used to estimate the maximum electrical current on a harness made of multiple wire gauges and insulations.
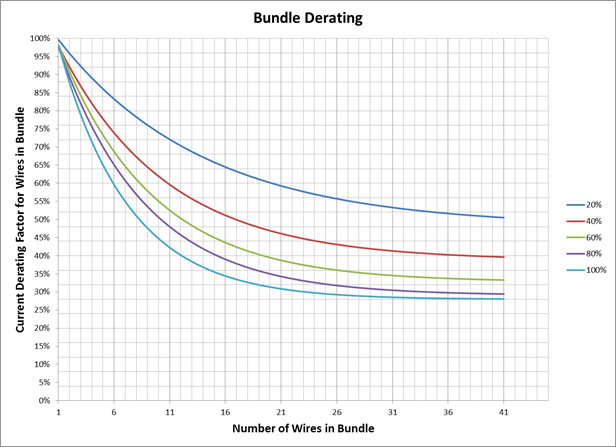
This formula can also be used to account for heating by nearby systems. For example, suppose we have a harness that is rated to 150oC (based on the wire specification). The ambient temperature in the zone during flight is 50oC, which leaves a potential for a 100oC increase during operation. Using the formulas and charts we find that the ampacity is approximately 40A.
Continuing with the example, suppose this harness is routed near a hot air duct. Testing has shown that the radiant heat will increase the surface temperature of the harness by 20oC. After recalculation, the harness ampacity drops by 10% to 36A. The results of the analysis may require use of larger gauge wires, rerouting, or the addition of a protective sleeve.