RTCA/DO-254, Design Assurance Guidance for Airborne Electronic Hardware is a commonly used document that provides instructions and process for airborne electronic hardware development and aircraft component certification. Formally recognized by the Federal Aviation Administration (FAA) in 2005, the DO-254 serves as a standard for ensuring the highest level of safety in the design of electronic airborne systems.
Process Requirements
This standard includes a process that has very rigorous compliance requirements. That is because it has five levels of compliance, A through E, that are hardware failure effect dependent and the subsequent impact on aircraft airworthiness. For example, a Level E failure would not affect the aircraft’s safety (low failure severity) while a Level A failure would result in a catastrophic failure and loss of aircraft and/or life (certainly a high failure severity). As one might expect, satisfying Level A compliance requirements necessitates more effort and attention to verification and validation than satisfying Level E compliance requirements.
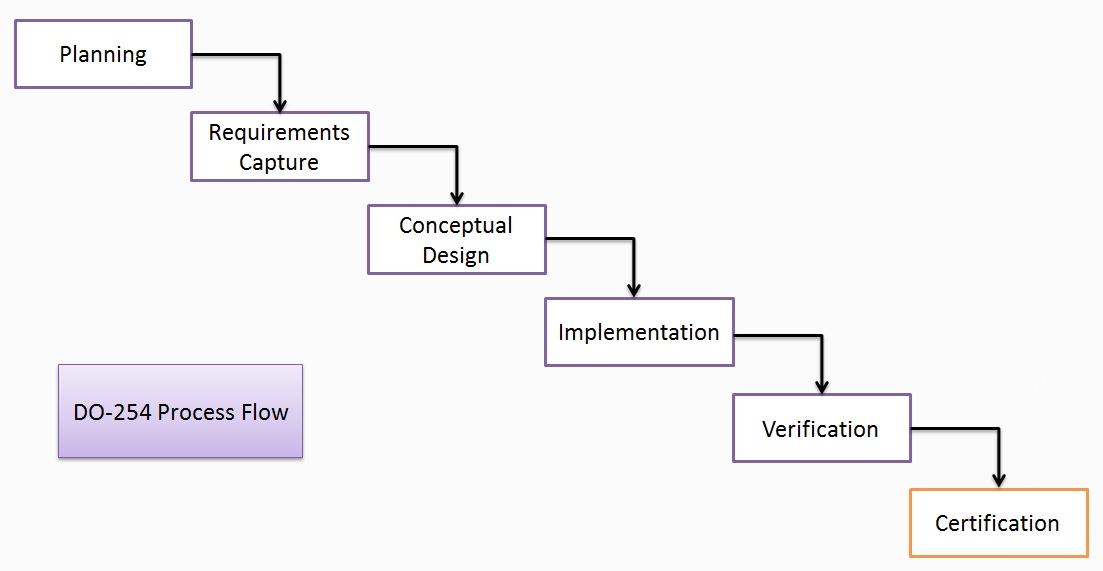
Illustrated in the above flow chart is the typical process flow of a DO-254 compliant design. By going through the associated tasks of this process, the design should prove that its implementation meets all of the requirements. Different tasks may be used depending on the project in question, however a key principle remains constant: verification results must be traceable and linked to the formal requirements.
Requirement Tracking
Because of the importance of requirements in the verification process, capturing the formal requirements is the first step in any DO-254 design development and it is often done by using a special tool such as IBM’s DOORS® or Mentor Graphics’ ReqTracer. After all project requirements have been discussed and accounted for, the design specification and verification plan are generated. These documents are required by the FAA for certification by DO-254 compliance regulations and are used in a ‘Verification and Validation’ process at the end of the design process.
After making a list of formal requirements, the tools used in the process must also be assessed. This tool assessment includes verification and validation of both input and output of these utilized design tools. For this purpose, a document entitled the ‘Plan for Hardware Aspects of Certification (PHAC)’ is created and used. The document should contain information pertaining to the functionality, suitability, and any known limitations of the tools selected for the project. The Independent Output Assessment, relevant history, and basic tool qualification of each tool is described and compiled into the PHAC document.
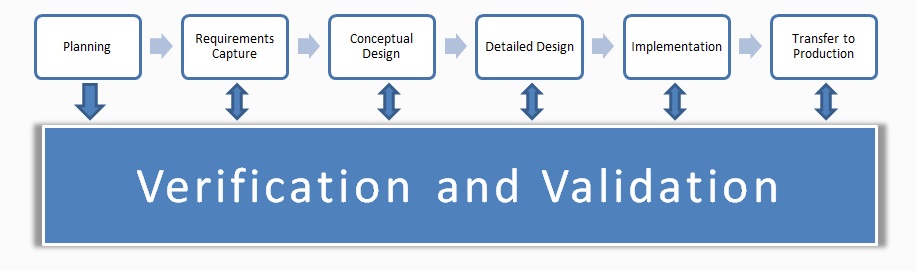
Verification and Validation
As with any formal hardware design assurance process, the ‘Verification and Validation’ is the most crucial phase in a DO-254 compliant design process and occurs throughout the project lifetime. It ensures that the requirements are valid, implemented, and fully tested even after becoming certified. Tests are run and models are created to prove that the project successfully meets the formal requirements and does the desired function. The project must continue to undergo the process even after it has been certified to assure continued DO-254 compliant performance.
Lastly, before submitting the project to the FAA for approval, a ‘Hardware Accomplishments Summary’ (HAS) is written to assemble the compliance data accumulated during the project development period. The document should demonstrate that the project has achieved the objectives outlined in the initial final requirements, design specification, verification plan, and the PHAC. Once the team is satisfied that the DO-254 compliancy process has been followed correctly and satisfactorily, the HAS can be submitted for FAA certification and assessment.
More Information
For more information about the RTCA/DO-254, read the White Paper and Position Paper on the subject. These documents provide more in-depth explanations and details about the process and references for additional reading.