Key Takeaways
- Aluminum conductors are often preferred in aerospace applications because of their significant weight saving benefits.
- Electrical, mechanical, and physical properties limit the use of aluminum conductors on aircraft.
- Aluminum conductors used in aerospace applications are expected to be in conformance with ASTM B230.
Aluminum Conductors
The drive for lighter aircraft led to the use of aluminum structure for decades, it was only natural that engineers would seek to replace copper in the electrical distribution system as well. For years, the use of aluminum conductors has primarily been limited to power feeders for many aircraft for the improved current carrying capacity per kilogram versus copper. The limited use however is based on several factors that include, material creepage, tensile strength, temperature limitations, and resistivity. Here, we discuss the fundamentals of aluminum conductors, their limitations as described by aerospace standards, and techniques for their implementation.
Primary Differences
For those unfamiliar with aluminum conductor construction, the primary difference between this and a standard aerospace copper wire conductor is that an aluminum conductor will not have any plating. This means that the conductor termination techniques cannot include soldering and are limited to compression/crimping termination techniques or ultrasonic welding (USW). It is important to note that USW has been used extensively in the automotive sector and is relatively new to aerospace thus its performance requirements are not covered by any aerospace standards.
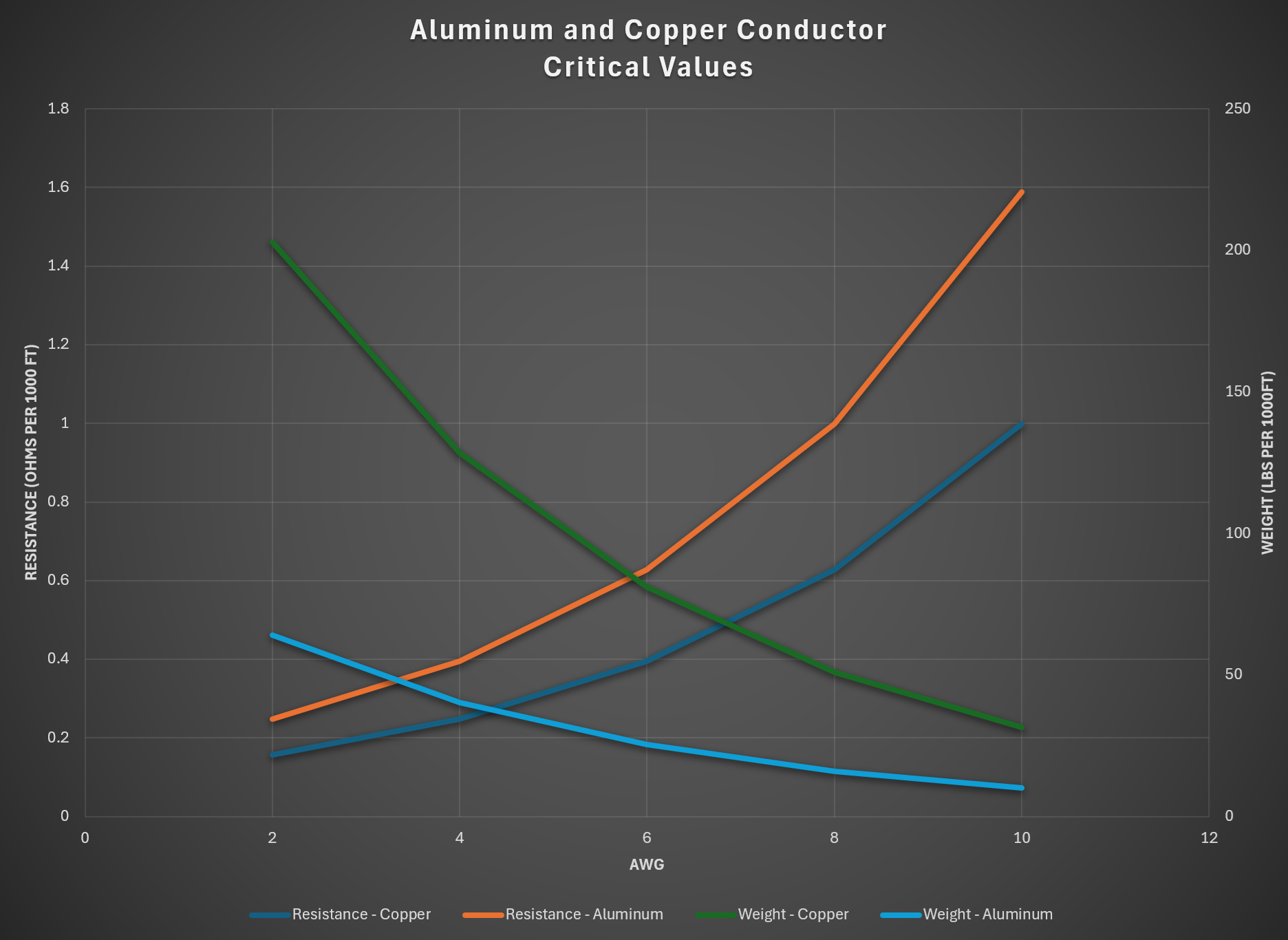
Aluminum conductors are lighter than copper conductors of the same gauge, however, there is a trade-off for electrical conductivity. An aluminum conductor of the same gauge as a copper one will have a 59% greater resistance. It is for this reason that a direct replacement of a copper wire with an aluminum one usually requires that the aluminum conductor be increased in size by one wire gauge (e.g., from a 16AWG copper conductor to a 14AWG aluminum conductor). Even with this resistance increase, there is typically a 50% conductor weight savings by switching to aluminum conductors. There are other factors to consider such as increased diameter, more insulation weight, and potentially larger terminations, but the weight saving can be appealing for many applications.
The standard governing stranded conductors for aerospace is the AS29606 which specifically calls out aluminum conductors in compliance with ASTM B230. Within this ASTM standard, there is a limited set of tests to be performed on the base conductor. These tests include diameter measurement, visual inspection of the conductor finish, tensile strength and elongation, and electrical resistivity.
These are all standardized tests and do not have any specific or unique activities related to them. An interesting item identified in the ASTM B230 standard is that it specifies for the conductor to,
“…be free of brittleness as evidenced by its ability to be coiled or looped around its own diameter without a mandrel. No fracture shall occur. Slight surface checks shall not constitute cause for rejection.”
In applications, as will be discussed later, aluminum conductors are not typically installed in tight bend locations, but even if they are bent for installation purposes, it is important to know that the conductors will not simply break with limited of bending or flexing.
In Application
Aluminum conductors are permitted for limited applications in aerospace. Using the guidance of AS50881, the use of aluminum conductors is restricted to sizes 8 AWG and larger. The reason for this historically has been to limit their use to only higher power applications and ensure that there is sufficient conductor tensile strength to prevent breakage during normal operations.
Furthermore, the use of aluminum conductors is limited to mostly benign areas within a vehicle and use in high vibrational equipment, such as engines, is prohibited. The rationale for this prohibition is the cold flow of aluminum from compression points. To further expand on this, aluminum is a strong material and does perform well in many applications however, when aluminum conductors are placed under pressure, such as under a crimped terminal, the metal may slowly flow from the compression stress creating a higher resistance connection point that can potentially lead to heating at the termination, and if not identified early, may lead to fires.
Length Limitation
One of the limitations in AS50881 is that the aluminum conductor may only be used in wire runs greater than 3 ft; this limitation has created a lot of questions and uncertainty. The rationale for this statement in the AS50881 standard is that, when the weight benefits of aluminum conductors were examined, the overall benefits became more limited as the conductor length decreased. As such, the guidance evolved to limit the minimum wire length to 3 ft to avoid designers and engineers attempts to install and use aluminum conductors throughout the aircraft with limited benefits.
Furthermore, aluminum conductors should not be installed in areas where they might be exposed to corrosive fumes. Aluminum can corrode when exposed to highly alkaline or acidic compounds, sulfates, chlorine, etc. To limit the risk, aluminum conductors should be installed in within fairly benign areas of the aircraft that are unlikely to be exposed to fluids.
The last item that should be considered before selecting aluminum conductors is that they should be installed in relatively permanent applications. In other words, aluminum conductors should not be in locations where regular movement or equipment swaps are necessary. The rationale is to limit the flexing and bending of aluminum cables. Since this precaution was added to AS50881, there have been improvements with aluminum cable design that make them easier to use and install, however, adherence to this guidance is still recommended. Deviation from such guidance does require extensive testing to ensure that the production processes, installation, and use profile do not create an unnecessary increase in risk to the aircraft wiring system or the airworthiness of the vehicle.
Conclusion
The use of aluminum conductors is appropriate for aircraft use if they are used in accordance with the lessons learned and captured in aerospace standards such as AS50881 and ASTM F2639. Deviation from the best practices outlined in the standards requires extensive testing to ensure that the fielded deviation does not create an unsafe condition for the vehicle. While there are opportunities to replace copper wires with aluminum, care must be taken to ensure that there has been due diligence in matching the parts selection with this installation as required in the EWIS regulation 25.1703.
For those seeking to qualify their cables, connectors, terminals, or other parts of their aircraft wiring system, contact Lectromec.