Key Takeaways
- Harness protection materials address needs such as fire protection, physical damage protection, chemical protection, and wire management.
- Additional harness protection may be used to achieve equivalent separation distance when routing space is limited.
- Protected harness designs face challenges such as overheating and difficult access for maintenance/inspection.
At the onset of design, wire harnesses are nothing more than reserved space in aircraft between electrical equipment. As designs mature, the electrical needs usually emerge first (Carry X Amps, or need to be 50 Ohm impedance with less than 3dB/100ft attenuation at 100MHz), followed by physical needs (must be rated for 260oC and have no impact due to hydraulic fluids), then lastly, practical needs (the harness is routed in a high traffic area and needs additional physical protection). As these factors emerge in design, the harness goes through review cycles to ensure that it can achieve its performance needs.
When the wire/cable cannot achieve the performance requirements on its own, additional harness barrier materials may be used and implemented. These harness protection materials address needs such as fire protection, physical damage protection, chemical protection, and wire management. This article covers the factors for the use of harness protection materials and how they may impact design and performance.
Harness Protection
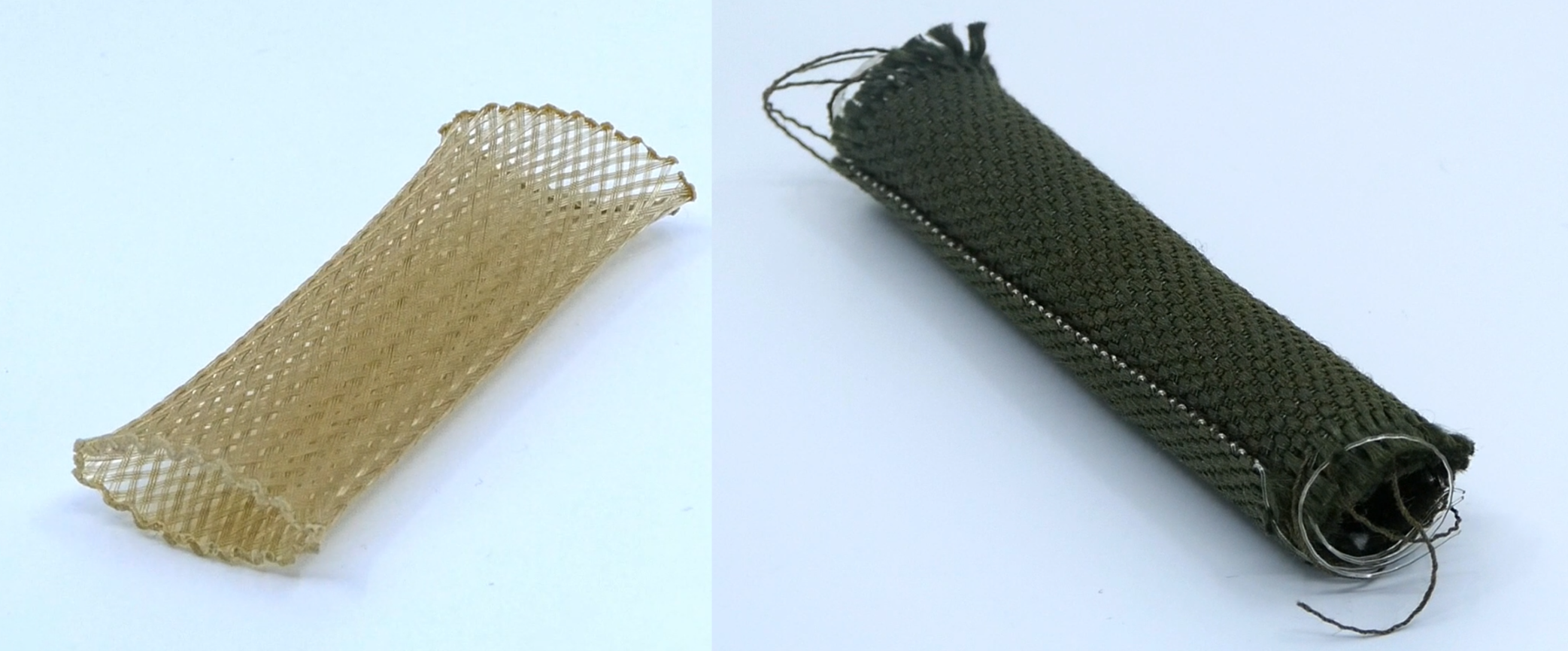
Secondary harness protection is any additional material that is added, wrapped around, or encloses a length of the wire harness. This enclosure/sleeve may be made of textiles, plastics, fluoropolymers, or any other type of material. The wire harness may be fully enclosed such as by an aluminum conduit, or it may be rather open with limited optical coverage of the wire harness (think open weave mesh).
Regulatory Reasons
Good design with separation from hazards such as chaffing, fire, maintenance damage, etc. should be the first means of protecting wire harnesses. Even with good design, this does not eliminate the need for secondary harness protection where routing alone cannot achieve the necessary protection of the harnesses. FAA regulation §25.1707 specifically, §25.1707(a) states:
“Each EWIS must be designed and installed with adequate physical separation from other EWIS and airplane systems so that an EWIS component failure will not create a hazardous condition. Unless otherwise stated, for the purposes of this section, adequate physical separation must be achieved by separation distance or by a barrier that provides protection equivalent to that separation distance.” [emphasis added]
These barrier materials that “provide protection equivalent to that separation distance” can include harness protection. The following are a couple of examples of how to consider the “equivalent separation distance” statement:
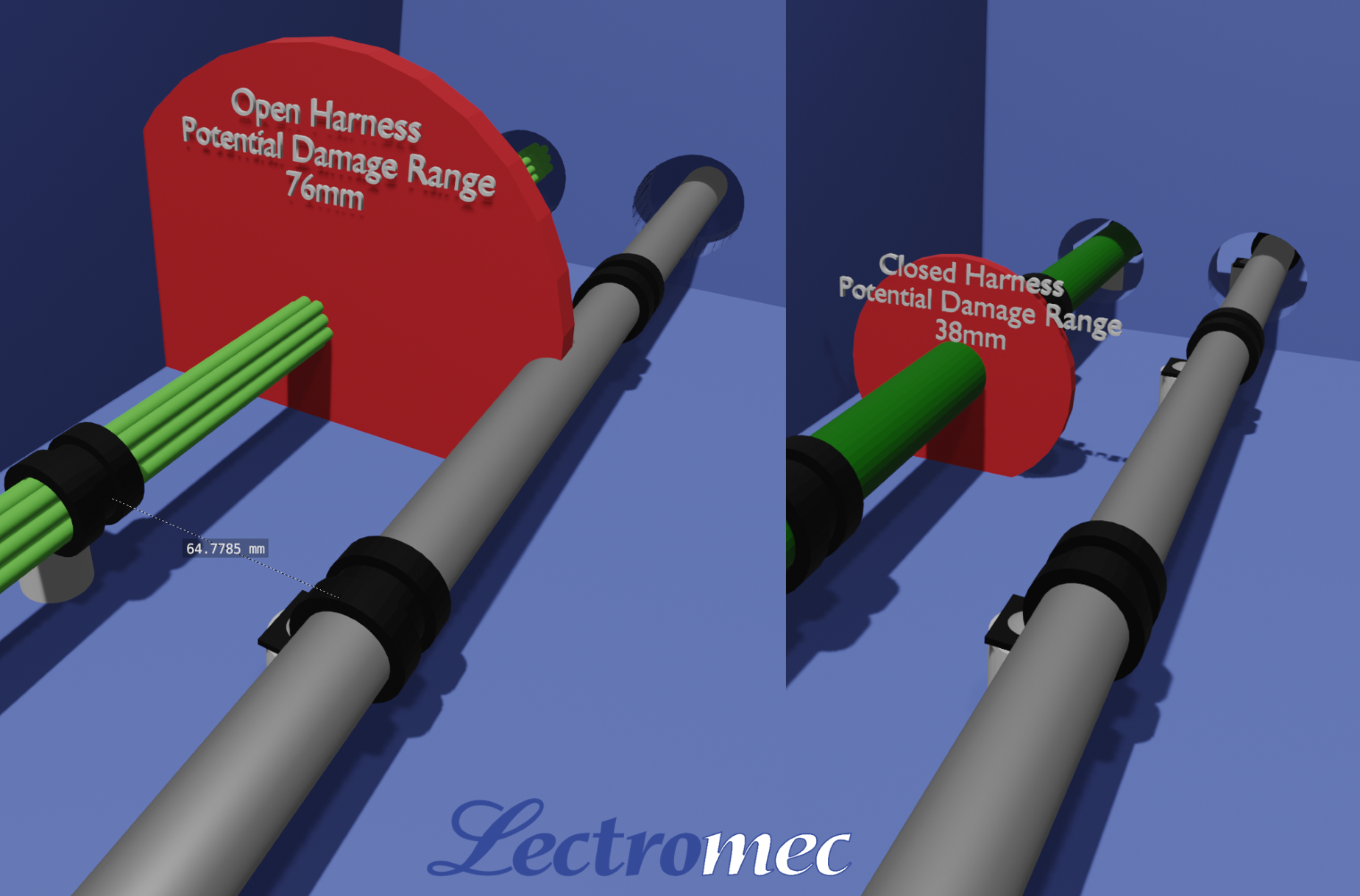
- A wire harness is routed near a hydraulic line. (see figure) Simulation and testing of an arcing failure within the wire harness showed that a minimum separation distance of 3 inches (76mm) is needed to prevent cascading damage and rupture of the hydraulic line. The physical limitations within the aircraft zone prohibit separating the hydraulic line to wire harness distance to anything more than 2.5 inches (64mm). Engineering reviewed design options and elected to evaluate a harness protection scheme. Simulations and testing found the selected harness protection material reduced the minimum separation distance from 3 inches to 1.5 inches (38mm) thereby achieving the goal of an equivalent separation distance.
- A wire harness is routed near a hot air duct. Testing found that rupture of the hot air duct could lead to wire insulation damage and potential shorting/arcing of the wires. To prevent direct hot air on the wire harness in case of duct rupture, an additional wire harness sleeve is added to slow thermal conduction to the wire harness. Additional protection prevents the need to move the harness and provides the equivalent separation distance.
Guidance from Standards
Open versus protected harness design as called out in 3.8.5 of AS50881 states,
“Harnesses shall be of either open or protected design. Open harnesses are preferred for maintenance considerations. Harnesses may be designed to meet mechanical or shielding requirements. The use of protected harnesses shall be avoided unless wiring design considerations dictate their use and is subject to the approval of the procuring activity.”
ASTM F2639 identifies that open harness design is,
“…used in point-to-point open harnesses, normally in the interior or pressurized fuselage, with each wire providing enough insulation to resist damage from handling and service exposure… This practice is known as open wiring and offers the advantages of ease of maintenance and reduced weight.”
Pros and Cons
The following are pros and cons of the open harness and protected harness design options. This is not a complete assessment of both options, simply a starting point for consideration of each option.
Pros |
|
|
Cons |
|
|
Conclusion
There is no one-size-fits-all answer for what scenarios are best for the use of additional harness protection and the use of any additional protection requires consideration of all the factors outlined above. As a closing consideration, AS50881 identifies that EWIS design precedence should start with flight safety, followed by ease of maintenance, and lastly, the cost. While open harness design is preferred for several reasons, there are few aircraft, if any that can have an EWIS without additional wire harness protection used somewhere in the design. Because of the wide range of options available, time must be taken to find one that best meets the aircraft performance requirements.
For those looking for a lab to assess harness protection, such as to the EN6059 standard, Lectromec’s ISO 17025:2017 accredited laboratory is here to help.