Key Takeaways
- The goal of the forced hydrolysis test is to represent decades of wet/humid environmental exposure on an aircraft.
- Forced hydrolysis testing is typically limited to wires/cables where polyimide is part of the insulation system.
- Pass/fail criteria of the test effectively depend on a dielectric voltage withstand post-test used to identify any breaches in insulation.
Forced Hydrolysis
Fluid immersion of electrical components is often done to determine material compatibility. However, there are fluid immersion tests that are more about material degradation and accelerated aging than compatibility; this is where forced hydrolysis testing comes in. While it is not part of every wire/cable qualification testing, it is applicable to some constructions, and how/why that is the case is important when building qualification plans and selecting parts for use.
Objectives and History
Forced hydrolysis testing exposes a wire or cable to a long-term submerged water application at near-boiling temperatures. The original idea behind this was part of the degradation analysis around polyimide wire. It is known that direct exposure to humidity, heat, and mechanical stress will rapidly degrade polyimide films (if not for additional precautions or advanced techniques for material protection). To verify the long-term endurance of polyimide wire, the idea of forced hydrolysis was developed.
Understanding the rationale for forced hydrolysis testing starts by understanding how polyimide insulation is used and how it degrades. The film that was used in wires constructed the 70s, 80s, and early 90s was known as H-film. It had great mechanical properties, great flame resistance, and great radiation resistance, but when exposed to heat, humidity, and mechanical stress, the insulation degraded rapidly usually leading to rapid wire degradation observed with radial insulation cracks. After this was identified, companies developed techniques to extend the life of polyimide film for wiring applications.
Other wire insulation types, such as ETFE and PTFE, are unlikely to show degradation under these test conditions, and as a result, wires with those material types are not typically tested to forced hydrolysis. In fact, forced hydrolysis testing for aerospace wiring is only included as part of qualification testing if the insulation construction includes a polyimide film, such as the AS22759/80 – /92 or AS22759/180 – 192.
Test Performance and Applicability
In this test, several lengths of the wire are cut, typically about 18-24 in. These samples are then wrapped around a mandrel, for the 20-gauge wire size, the mandrel diameter is about 0.5 in. While not specifically called out in most forced hydrolysis test methods, the mandrel diameter and sample size should scale based on the wire or cable diameter being evaluated. The sample is then submerged in a saline solution at 70°C for thousands of hours. The ends of the sample are positioned above the water line to avoid fluid ingress between the wire conductor and the insulation.
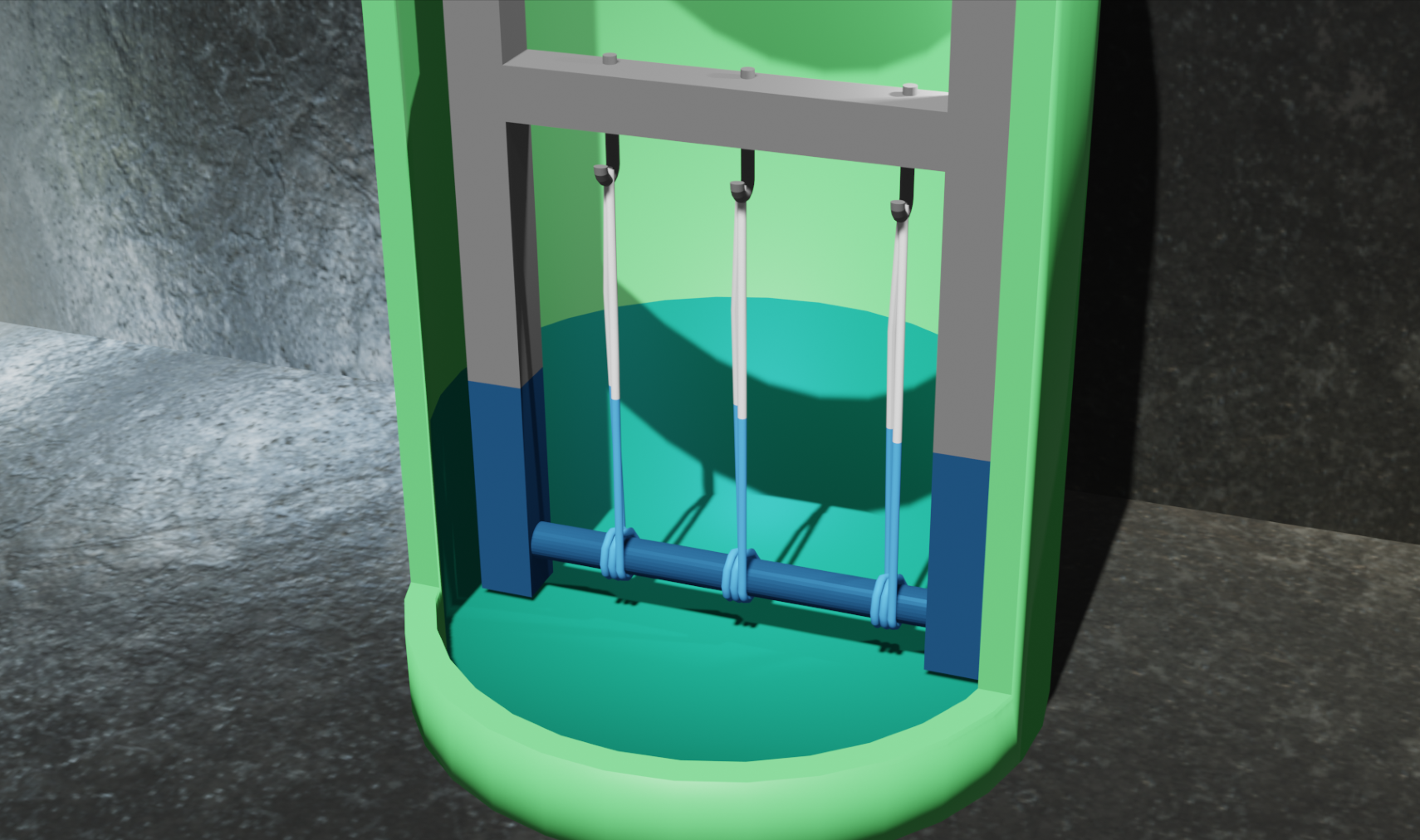
While no testing is performed on the samples during the long fluid immersion, a simple modification would be the periodic performance of dielectric voltage withstand tests where a voltage is applied to the conductor and a ground return is placed into the fluid bath. This would verify the insulation integrity and determine if any samples have insulation breaches thereby reducing the test duration based on sample performance.
Effectively, the test’s pass/fail criteria is entirely based on the post-test dielectric withstand assessment. The sample is considered to have passed the forced hydrolysis test if it is found without an insulation breach at the end of the exposure duration.
As stated earlier, this test technique is primarily designed for polyimide-insulated wires. However, the same technique may be used for other component tests where long-term fluid exposure is required. For example, if a component is to be submerged in a fuel application for years or decades, the forced hydrolysis test can be adjusted to use kerosene in place of a saline solution. This is very similar to the fluid immersion test albeit with a much tighter bend on the wire cable under evaluation (Fluid immersion testing usually calls for the bend radius to be at least 14x the specified maximum diameter of the wire).
Potential Issues
As the test is performed at an elevated temperature, it is important for there to be a reflux mechanism to ensure that the fluid is not boiled off too quickly. This ensures that the water levels are maintained, otherwise, the sample is hanging in air exposed to steam or hot dry air. Lastly, the wire or cable should be inspected before the test. Visual examination and pretest voltage breakdown should be done to ensure that the sample is not damaged before the test. Lectromec will typically do a voltage withstand test once the sample is installed to ensure that no damage was incurred during the handling or installation. This does place additional voltage stress on the insulation, but it is done to ensure that thousands of hours of testing are not wasted.
When considering the application of this test, it is important to consider the material properties of the insulators. For example, the original MIL-W-81381 wires had a humidity resistance test as part of the product verification, yet the material was still prone to degradation when exposed to long-term moisture and mechanical stress.
Application Factors
The goal of the forced hydrolysis test is to represent decades of wet/humid environmental exposure on an aircraft (think SWMAP zones). While most aerospace wires will not spend their service lives submerged in water, the test, like many accelerated aging tests, uses conditions that exceed expected service conditions to generate results within a reasonable duration. The impractical test condition is accepted because the results generate data to support service life predictions.
As with any accelerated aging test, the parameters are very important. It is possible to perform the forced hydrolysis with a tighter bend radius or perform the test in a pressure vessel so that the water could be at an even higher temperature; the testing under these more stressful conditions might introduce other failure mechanisms that would not occur under normal conditions.
Conclusion
Forced hydrolysis testing is used for wire/cable evaluation and accelerated aging in numerous industries and product constructions. For aerospace, the use of this test method is typically limited to wires/cables where polyimide is part of the insulation system. While the test is frequently a long-term test taking thousands of hours to complete, it is a necessary part of product verification to ensure reliability when installed on aircraft. To find out more about this test, contact Lectromec.