Key Takeaways
- Tools, equipment, materials, and an adequate understanding of each are integral to any maintenance task.
- Specialized equipment and materials are utilized in the process of cleaning avionics components.
- Proper knowledge and methods are utilized to minimize the possibility of hazards to personnel and equipment.
Introduction
In two previous Lectromec articles (part 1, part 2), we discussed preventative measures, identification methods, and cleaning procedures for corrosion on avionics equipment identified in AC 43-206. Here, we discuss some of the cleaning equipment/tools, materials, and potential hazards identified in AC 43-206.
Tools, equipment, and materials are clearly an integral part of any maintenance task and, in coordination with these, an understanding of potential hazards is a must. Anyone involved in maintenance must be educated in the proper use/application of any materials, tools, or equipment they are expected to use as well as the potential risks posed by exposure to or misuse of such items.
Cleaning Equipment
Due to the diverse variety of avionics equipment present on a single aircraft, many different tools are required for adequate maintenance. The minimum requirements for an adequately equipped cleaning facility are identified in the AC as follows:
- Facility/ Equipment
- Adequate lighting
- Applicable cleaning and support equipment
- Ventilation system with controlled temperature and humidity
- Sufficient space for any cleaning equipment to be operated
- Documentation
- Operational instructions/manuals for all applicable equipment
- MSDS/ Hazardous SDS for each substance used (cleaning fluids, etc.)
- Trained Personnel
- Quality assurance inspectors
- Avionics technicians
- Support equipment operators
- Those trained in accordance with AC 43-206 to identify corrosion of avionics
Outside of the more straightforward hand-cleaning methods many of the common cleaning equipment can be categorized as abrasive cleaning tools, ultrasonic cleaners, or spray booths
According to AC 43-206 “Abrasive cleaning tools such as portable mini-abrasive units and blast cleaning cabinets are used to remove corrosion and corrosive products.” Though useful in a wide variety of cleaning applications, it is important to understand the limitations of abrasive cleaning tools; many sensitive pieces of avionics equipment are prone to damage under abrasive conditions (the medium used for abrasion particularly affects this); either the use of alternate methods or the expertise of properly trained personnel must be considered in these situations.
Ultrasonic cleaners are employed for the removal of oils, dust grease, hydraulic fluid, and loose corrosion deposits on certain avionics equipment. These machines clean using either a solvent solution or an aqueous detergent solution for ultrasonic scrubbing of the equipment to be cleaned. Only approved detergents and solvents should be used in ultrasonic cleaners.
A water base spray booth may be used for either rinsing or cleaning of avionics equipment as applicable; it is preferable that such a booth be equipped with a 360o turntable to allow for the rotation of the avionics equipment within. If used for rinsing equipment, the spray booth may be utilized before and/or after other cleaning methods are applied.
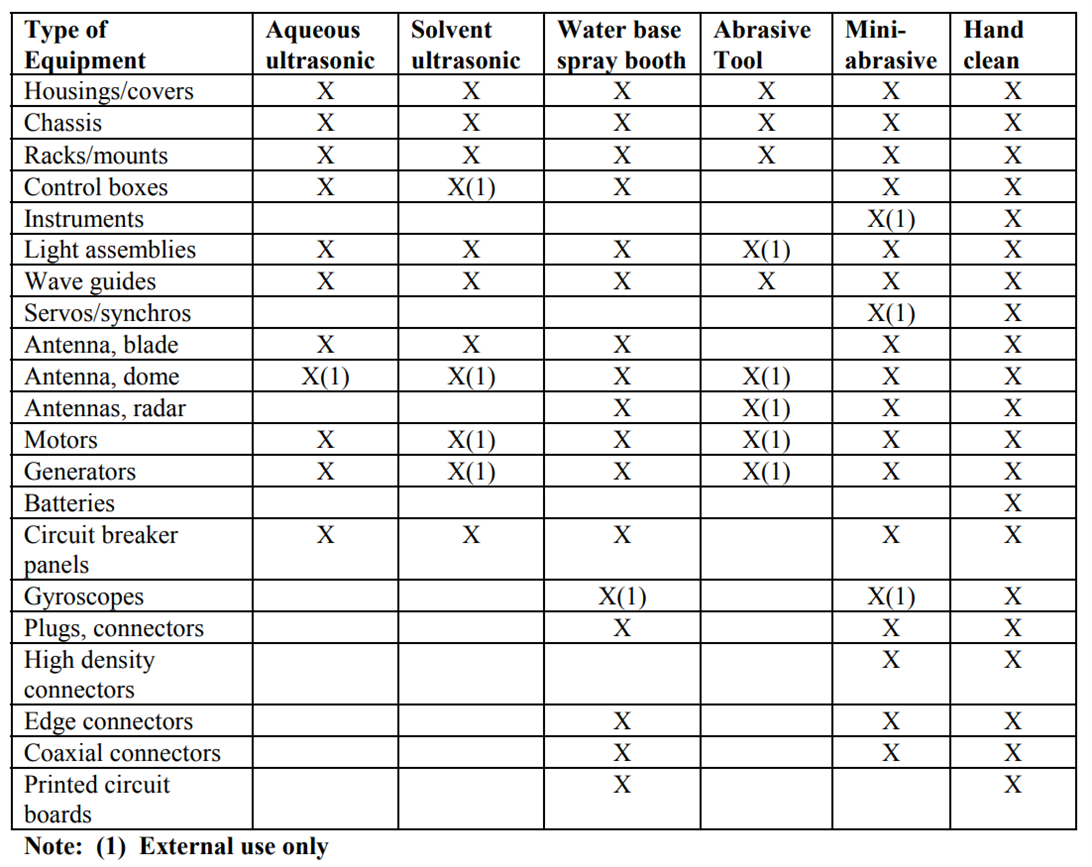
Table 4-2 of AC 43-206 identifies common avionics equipment along with the cleaning tool(s) recommended for each piece of equipment.
Materials/ Fluids
AC 43-206 identifies the following fluids for use in avionics cleaning:
- Nonionic liquid detergent Type I MIL-D-16791
- Electrical contact cleaning and lubricating compound Type I MIL-C-83360
- Trichlorotrifluoroethane cleaning compound Type II MIL-C-81302
- Dry cleaning solvent Type II P-D-680
- Isopropyl alcohol TT-I-735
- Distilled water
The AC goes on to describe the characteristics, applications, and restrictions for each fluid.
One of the key practices in the use of solvents and detergents is ensuring the correct concentration when mixing the fluids in water. The concentration of the aqueous solution needed for cleaning different parts will vary based on the part’s component materials.
Hazards and Considerations
As with any maintenance work, avionics cleaning comes with its own set of potential hazards; this includes hazards to equipment as well as hazards to personnel. There are many such concerns to bear in mind when developing cleaning instructions and performing cleaning actions on avionics components. Some pieces of equipment may become damaged when exposed to inappropriate cleaning fluids or methods, others may be prone to entrap cleaning fluids or other debris during maintenance activities.
Cleaning materials and fluids can be contributors to both equipment and personnel hazards. Some cleaning fluids contain CFC materials (Chlorofluorocarbons) which are known to be ozone-depleting substances; there may even be applicable environmental restrictions that ban or limit use. But even apparently mundane cleaning fluids may become hazardous if used incorrectly.
Cleaning methods must also be applied appropriately to avoid hazards to equipment and personnel. The use of incorrect cleaning methods for specific pieces of equipment may irreparably damage the equipment. For instance, there are devices within some PCBs (Printed Circuit Boards) particularly sensitive to electrostatic discharge that “may be destroyed by the static charge created in the rapid movement of air and abrasive agents in the abrasive cleaning tools.” Thus, it is imperative to identify an alternative safe cleaning method for such devices. Incorrect use of tools and machinery may also lead to injury of personnel.
Precautionary measures must be taken to protect both equipment and personnel during maintenance actions. The use of gloves, masks, goggles, and support equipment, as applicable, can be effective for protecting personnel, however, the most effective personnel protection is proper training. To minimize hazards during maintenance, AC 43-206 recommends the following pre-cleaning procedures:
- “Disconnect electrical and other power sources (mechanical/hydraulic).
- Ensure the work area and equipment are safe for maintenance.
- Ensure drain holes are open.
- Remove covers and panels for accessibility.
- Disassemble where practicable.
- Use only authorized materials.
- Ensure compatibility of materials prior to use.
- Mask and protect accessories or components to prevent intrusion of water, solvents, and cleaning solutions.”
Conclusion
At first glance, it may seem excessive to have such a lengthy document dedicated solely to corrosion prevention and maintenance on aircraft, but in a series of three articles, we have only reached the surface level of understanding corrosion modes, prevention, and maintenance. Due to the sensitive nature and extensive variety of avionics components present on a single aircraft detailed methods and instructions are crucial to avoid additional damage. Resources such as AC 43-206 are extremely valuable to anyone involved in aircraft maintenance activities, from the hands-on maintenance technician to the component manufacturer developing maintenance instructions for a specific part.
Contact Lectromec today for further information on how we can help with your corrosion assessment and prevention needs.