The three-day SAE 8A (Wire Installation) & SAE 8D (Wire and Cable) committee meeting was held in Melbourne, Florida on the famous Space Coast. The focus of the meeting was aircraft wiring.
It was collocated with the AE-7 power committee and the solid state power control/switching committee (AE-8B) to promote intercommunication between the areas of interest. Conflicts can arise when these systems need to be integrated and one or more of the components do not work well together (e.g. a 600V wire is attached to a connector rated at 300V).
The best input to these committees comes from system integrators and Original Equipment Manufacturers (OEMs). For those who work in these capacities, your involvement into these groups ensures that the standards match the industry needs.
Listed below are five areas that were discussed at the SAE Conference.
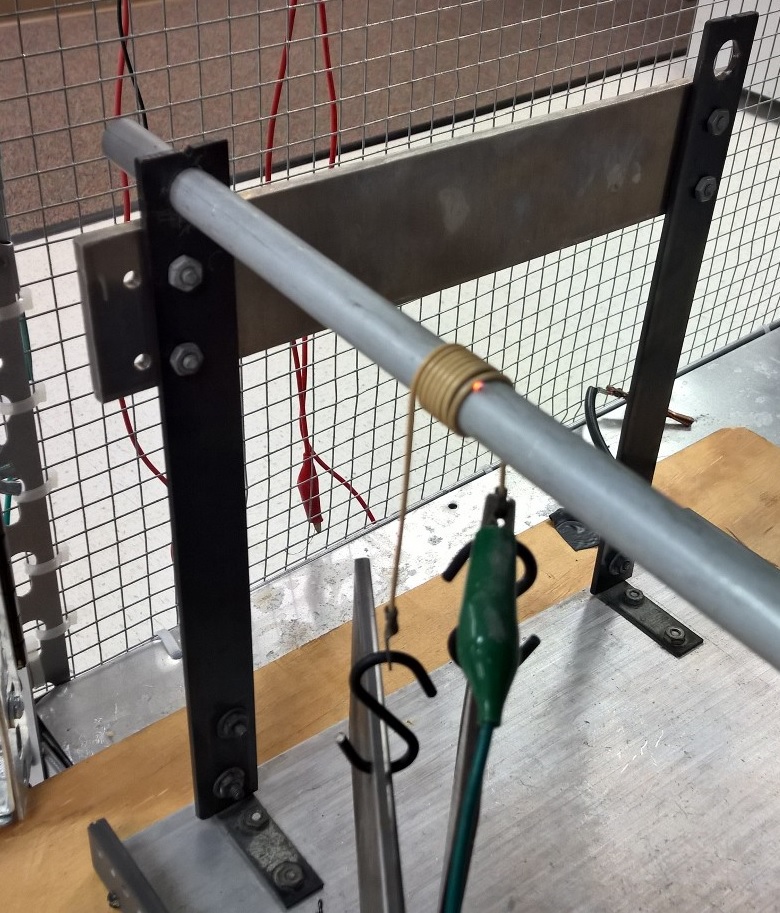
1. Higher Voltages
In the past, Lectromec has discussed the issue of higher voltage power systems in aircraft. This is an important topic and task group updates are provided at every SAE meeting. The task group has been making progress on identifying the complexities of design, implementation, and assessment.
Although higher voltage systems significantly impact wire/cable’s design, the task group has focused their efforts on these four assessment techniques:
- Dielectric Withstand Voltage: the required dielectric test for a wire rating at some multiple of the rated voltage.
- Insulation Resistance: may include long-term elevated temperature exposure at rated voltage without a significant degradation of insulation resistance.
- Corona Discharge: need to consider the voltage impact both at sea level and operational altitudes.
- The Arc Track Rating: when applying the arc track resistance requirements, should the acceptable damage limit be the same as that for lower voltage systems? The counter to this argument of wire assessment is that any sort of arc track impact could be mitigated at the system installation level (e.g. solid state power controllers, etc.).
Depending on the work from this task group, several voltage classifications may be created. Each of these voltage classifications could potentially mean that thicker insulations will be required to safely withstand long term voltage exposure.
2. Design Implications for aerospace wiring
With respect to the issue of switching devices, there are several considerations that must be factored into design:
- When switching from “on” to “off,” there is a need to control the air gap distance to ensure the circuit is broken (peak gap voltage).
- The electrical field strength enhancement effects on adjacent dielectric, as well as surface breakdown mechanics, can result in a design that fails at lower voltages.
- The dielectric breakdown strength at the highest possible voltage to be experienced by the system.
- Any voltage above the 327V (minimum air breakdown voltage) threshold will increase the likelihood of an electrical discharge.
- Height and volume reduction goals. Will the high voltage systems cause a net reduction in system weight?
3. New System Definitions
When MIL-E-25499 was created (General Requirements for Electrical System, Aircraft, Design, and Installation), the overall aircraft architecture was much simpler. An example from this standard is shown in the following figure (source: MIL-E-25499).
In a purely fundamental sense, the system remains the same (power is created, transmitted, then used by some load). However, since the initial design, much has changed (for additional information, you can read Lectromec’s Introduction to Aircraft Electrical Power Distribution Systems article) and will continue to change with new technology. One aspect of this improvement ae solid state power controllers.
4. Solid State Power Controllers
One of the most interesting comments during the inter-committee discussions of the meeting was that “Solid State Power Controllers (SSPCs) have become a virtual component with no defined envelope or location – they are no longer a defined piece of hardware.” The algorithms for power controllers combine both hardware and software to handle the power routing, circuit protection and, in some cases, fault detection.
As these devices become more advanced, there needs to be a set of requirements designed for these systems. Some of the issues to consider when designing the requirements include:
How should these devices fail? Should they fail open (break the circuit) or closed (maintain power), or should a more general case of the system should “fail-safe” be applied? The answer is that it depends on the technology implemented by the SSPC designer. However, it should be clear to the electrical system designer what to expect from the equipment in normal operation and in fault conditions. For some systems, it may be advantageous (or necessary) that the device fails closed to ensure a critical system’s power is not cut.
Beyond the operational considerations, there needs to be a set of minimum specifications for the mechanical, environmental, and electric requirements on the equipment. Like all aerospace equipment, these devices are evaluated with the DO-160 requirements in mind, but these flight critical components should have a minimum performance specification.
5. Laser Marking Product Codes on Wires
Laser wire marking has been successfully used in aerospace applications for a while now as a suitable option to ink marking and far superior to hot stamp marking. A question has been raised regarding whether the manufacturer code and product ID that are printed on the wire/cable should also be printed using this proven technology. On wires, the manufacturers’ code is typically seen with green ink. The benefit of using the ink-printed systems is that they provide a color contrast to the black UV laser marks and make it easy to identify the difference between the product code and the circuit ID printed on the wire/cable by the aircraft OEM. Several ideas were proposed on how to avoid the overlap and/or ensure both codes were distinguishable.