Key Takeaways
- Lectromec’s arc damage modeling tool can be used for 25.981 compliance.
- Achieving certification is more than just showing a design a safe but also showing that there is a legitimate margin of safety.
- This process has been employed on several certification projects.
- Listen to the podcast here.
FAA regulation 25.981 covers the requirements of fuel tank ignition prevention. While there are numerous elements that must be considered as part of the 25.981 regulation, this is a Lectromec series of articles, and here we focus on the electrical hazards that must be identified and mitigated as part of certification.
The last article ended with an example of three-wire three-phase 115VAC power wires harnesses. The open question at the end of the article was: “What are the possible consequences when an electrical arcing event occurs in this scenario?”
Released Energy
The event begins with predamage to the wires and contamination creating an electrical path between two of the three wires. When considering the voltage, available current, and circuit protection devices in the system, a first-order estimation of the energy released is more than 60,000 J (or about twice the total stored electrical energy in a fully charged iPhone X battery). While it is an impressive amount of energy, this energy gets split among multiple elements of the arcing event: this includes burning the wire insulation, destroying the electrical conductor, heating the local environment (arc plume), and potentially transferring heat and energy to the fuel tank wall. From a safety perspective, it is important to quantify how much energy goes into heating of the fuel tank wall. Further, the data must be gathered to identify if there was enough arc energy to have electric arc jump the gap from between the wires directly to the fuel tank.
Starting with the second item (arcing directly to the fuel tank), tests and simulations performed by Lectromec have shown it is entirely possible that the scenario described here would cause the electrical arc to bridge the 0.5 inch gap from the wiring harness to the fuel tank. If fuel tank penetration occurs, this can only be classified as a potentially catastrophic event. If the fuel tank is not breached, but direct arcing does occur, this can also be considered as a potentially catastrophic event; to determine the severity of this event requires an evaluation of the temperature of the inside fuel tank wall.
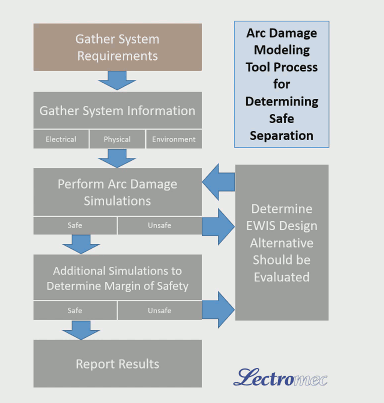
Safe Design
What method is available to prove that your EWIS design a safe and achieve compliance with fuel tank ignition prevention and EWIS requirements? As with most systems, this can be approached either through physical testing or through numerical analysis. The first option of direct physical testing is something that Lectromec has discussed through multiple articles and multiple papers. An area that can be used to expedite 25.981 certification is Lectromec’s numerical analysis/simulation tool we refer to as our Arc Damage Modeling Tool (ADMT) (whitepaper on ADMT).
For the scenario to be addressed with the ADMT, Lectromec will gather the system’s electrical, mechanical, and physical parameters. This information is then entered into the arc damage modeling tool as a parameter set as the simulation initial configuration. The ADMT takes the system information, evolves the arcing event (wire damage, local environment ionization, etc.) and produces a set of data that can identify whether this configuration is safe or unsafe.
In the case of safe configurations, the tool is then able to examine the margin of safety. This is done by increasing the amount of energy involved in the arcing event (either through an increased duration or increased power) until the point a failure condition is observed. From a regulatory/risk assessment perspective, it is important to know that a design is not near the razor’s edge of an unsafe configuration.
For those scenarios in which an unsafe condition is identified, there are several options that can be explored to achieve a safe configuration. Many of those are explained in this article. Each one of these parameter variances, physical protection, increased separation distance, modification of circuit protection, etc. and each is are capable of examination through the modeling tool.
Back to the Fuel Tank
Returning to the fuel tank simulation and configuration discussed earlier, the ADMT is able to identify that this configuration is unsafe. The output identifies that, under common aircraft conditions, the probability of an arcing event creating an unsafe condition is very high. The simulation is then rerun with the inclusion of an arc fault protection device and the new simulation identifies separation distance as safe and no further modifications to the design are necessary.
At the end of this, a report is generated identifying that the configuration is safe, the estimated margin of safety associated with the current configuration, as well as another report identifying what elements of the original design were unsafe.
Conclusion
Achieving the certification of the electrical wiring interconnection system is a challenge; ensuring that the wiring system does not impact reliability or cause fuel tank ignition, is even more complex. But this complexity can be addressed in a methodical approach that has been applied to several platforms as part of their certification package. Lectromec’s arc damage modeling tool is a one-of-a-kind solution that can help your fuel system certification go through more smoothly. To find out more about the arc damage modeling tool or to schedule a demonstration of its capabilities, contact Lectromec.