With More Electric Aircraft (MEA) being the big push in the industry, it is important to take a moment and think about the wiring system that is going to be supporting these new designs. The following are some of the consequences resulting from an increased electrical load on the aircraft wire system:
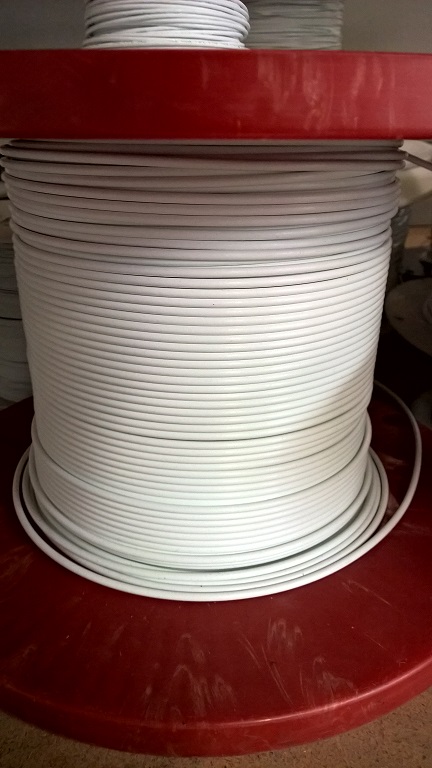
A Push to Higher Voltages
To learn more about the consequences of high voltages, read Lectromec’s article on effects of high voltage on aerospace wire connectors.
Higher temperature wire harnesses and increased electrical load on the aircraft wire system
Maybe the solution is not to go to larger gauge wires, but to simply push more current down the same size conductors. This can be done if the existing design has a large enough temperature margin (see Lectromec’s article on harness derating). But there are consequences for pushing more current down the same wires:
- High temperature on the wires: In the short term, this may not have an impact on the wire longevity, but higher temperature exposure to polymers will accelerate degradation. Each insulation type will have different rates of degradation based upon stresses, but the one constant is that temperature exposure does accelerate aging.
- Higher temperature for other EWIS components: The other materials that support the EWIS also have temperature limits. The clamps, connectors, splices, and harness sleeving have temperature thresholds. Before increasing the load on circuits, the impact on these factors must also be considered. This may require the use of different material types, which may also require reassessment of operational conditions and limitations.
- Impact on the zone: Where the harness is routed also plays a big impact on the design. Questions like, “Where is the harness routed?” and “Is there a high temperature or poorly ventilated area through which the harness is routed?” need to be answered. Increasing the current on these wires will also increase the temperature in these locations. How much will be dependent on several factors, but this heating impact cannot be ignored.
Larger gauge wire
The increased electrical loads on aircraft wire system could be addressed by using larger wire gauges. Of course, this leads to a number of drawbacks such as:
- Weight
- Size
- Flexibility/routing
Electromagnetic Interference (EMI)
Higher voltages and higher currents generate more EMI. With the need for more signal cables with EMI protection, this increases the need for more/better shielded cables, which drives up weight and cost. In addition, from a maintenance perspective, the cost for maintaining a multi-core cable is higher than that of unshielded cables.
Impact on system separation
It comes down to this basic question: which harness is less likely to cause damage to a fuel tank separated at 1.0 inch:
- a 10 wire harness filled with 20AWG wires powering 115VAC devices?
- or a 10 wire harness filled with 8AWG wires powering 115VAC devices?
Without question the 8AWG harness is going to need a larger separation. But here is the question: if there is a larger harness to feed the power-hungry devices, what solutions are necessary to address the new separation requirements? There is only so much physical space available on the aircraft and adding segregation materials on every harness is cost/weight prohibitive. Check out Lectromec’s whitepaper on the topic for more information and potential solutions to address this issue.
Summing it up
More power does not mean more of the same when it comes to the wiring system. More thorough analysis is necessary to examine these factors and others to ensure system longevity and reliable performance. There are tools, such as Lectromec’s EWIS RAT that can do an accurate analysis for More Electric Aircraft (MEA) EWIS.