XL-ETFE and ETFE are not the same. ETFE (or commonly referred in the industry as Tefzel®) is a well known material used in the aircraft and space industry. In fact, ETFE is a widely used material in applications as diverse as automotive fuel systems to greenhouse films. ETFE has a long history of use as electrical wire insulation in transportation systems like rail, automotive, marine and of course aircraft applications.
To bring attention to the differences between these materials, the British Civil Aviation Authority (CAA) issued in September 2006 Civil Aviation Publication 455 to specifically address the use of single non-cross linked ETFE extruded insulation. The CAA notice states, “There are a number of performance limitations with this type [ETFE] wire construction.” The notice also points out, “The insulation of this wire type can lose its mechanical properties (begin to melt) when the wire is subjected to high fault currents or is influenced by an external heat source.”
If you would like to learn more about wire degradation, you can read Lectromec’s XL-ETFE Aircraft Wire Degradation article on this subject.
During one of the cross linking processes, an additive is mixed with the ETFE which links chains of molecules together, thereby increasing the apparent molecular weight and the ability of the material to handle hotter environments and increased mechanical stresses.
Though neither the XL-ETFE nor the ETFE performs very well at temperatures over 200oC (482oF), the XL-ETFE will last longer in hotter environments. The XL-ETFE typically has a higher melting temperature than the straight material. This is not to say that the single wall ETFE constructions do not have their applications; when in common applications, the material will hold up extremely well. For example, straight ETFE has been in use in the rail transit application for over 20 years without a single material failure.
There is a growing concern that, because the specifications set a lower limit on the molecular weight of the material, some of the wire produced may not be as robust a material as it potentially could be. With a lower molecular weight comes a greater probability for cracks to form in the insulation. These cracks can form in the extruded material in a manner that is similar to those associated with polyimide insulations (aka Kapton).
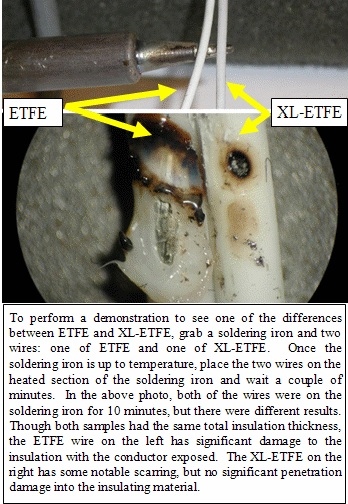
Some of the wire specifications that use extruded ETFE insulation, such as AS22759/16, there is only a single layer of extruded material, as opposed to the typical aerospace wire specifications which have two or more layers of insulation.
Because of the single layer of the insulation, a crack or nick can expose the underlying conductor. In the event of a crack in the insulation of a dual wall construction, as in AS22759/32, the propagation of crack is often limited to breach one of the layers.
Another concern is that the military wire specifications such as AS22759/16, which are now governed by SAE AE-8D Wire & Cable Sub-Committee, have not been recently updated. The additional requirements that are now standard with newer specifications have not been applied to this, making it an outdated standard.
If you are a maintenance operation with the goal of replacing ‘in-kind’ the damaged wire that you find on an aircraft, it is important to know that there is a difference. It is important not to assume that the two materials are the same; though they have similar characteristics, they are not the same.