Finding wire faults/damage is not an easy task; Lectromec’s last two articles [here and here] went through several test methods in an attempt to detect damage on a coax cable, and even in lab conditions, the damage was not detectable.
Now consider that problem across an entire aircraft. In-situ testing of wires/cables has always been viewed as something of a challenge to the industry. Given the branching that most harnesses undergo, the various wire lengths, splices, and numerous termination conditions, it can be difficult. Attempts to automate some of the testing has come to the development of Automatic Wire Test Sets (AWTS [pronounced “Eh-Wits”]).
Because there are so many ways to test a wire harness, the US military sought to create a performance standard to cover the general ideas and best practices of this equipment. Here, we review the standard and some of the performance features that can be expected when using equipment in compliance with the standard.
The Specification
MIL-PRF-32070A (available on the DLA website) is the current revision of the “Performance Specification for Test Program Sets” managed by the Naval Air Warfare Center in Lakehurst NJ. In general, the document sets out a performance profile for the Test Program Sets (TPSs) that are, “a collection of hardware, software, and applicable documentation used for testing, fault detection and isolation, maintenance, and any other evaluations of components and equipment” [ Section 6.4.22].
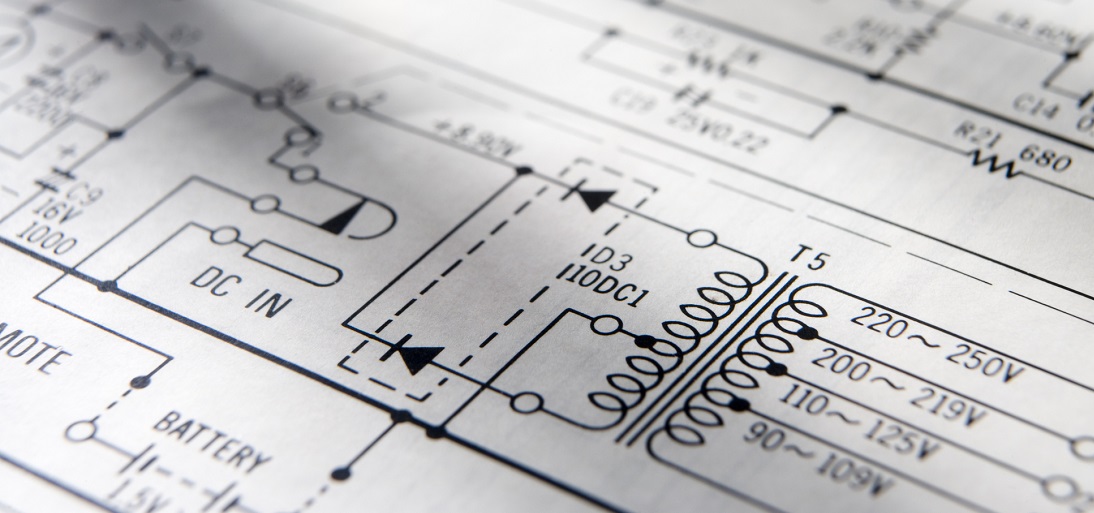
How the test system performs the fault isolation is left entirely to the individual test set and the system under test, but must conform to several performance requirements including (not all encompassing):
- Hooked up wire
- Equipment footprint
- Transportability
Identifying Faults
As part of the equipment’s performance testing the equipment must do the following:
“
[Section 3.3.6.4] The TPH performance test shall functionally test and evaluate the TPH (Test Program Hardware). If a failure is detected, the TP (Test Program) will halt any further testing, including UUT (Unit Under Test) testing. The TP shall direct the operator to execute the TPH diagnostics to effect repair of the TPH. At the completion of this test group, the TP shall return to the MAIN MENU. The TP shall:
- A: contain modules that provide test segregation to allow verification of applicable TPH for testing a specific UUT with the UUT disconnected (for example, wraparound test using shorting plugs or cables).
- B: have a run time interval not greater than ten minutes for each performance module and/or entry point.
- C: detect 100 percent of detectable TPH faults, including faulty wire paths.
- D: allow the ATE (Automated Test Equipment) operator to repeat/cycle each test or test sequence if more than one individual test is required to set up a test condition. A TPH GOOD message shall not result if a test is repeated due to a failed performance test.
- E: be performed without removing TPH covers, using TPH extender boards, or probing of the TPH.
- F. not require an additional interface device (ID).
“
Of course, the loaded statement is related to the detection of “100 percent of detectable TPH faults”. For wiring, the easy faults to detect are the hard shorts and open circuits, but what about corrosion on connector pins that increases the circuit resistance? Is this not a detectable fault? But therein lies the question between different types of equipment: How sensitive is the equipment as to not generate a false positive? This will vary based on the equipment and the setting of the equipment.
From a fault isolation perspective, within the range of the TPH capabilities, it must be able to fault isolate. The concept raised in the performance standard is that of ambiguity groups. This idea is the process of identifying the system fault that generated the fault message. Where possible, the equipment should be able to differentiate where the fault is (e.g. an issue with capacitor A versus capacitor B). The equipment is of little help if it identifies that there is a fault in the system without helping to troubleshoot where/what it is.
Implementation
When put into service, the TPH must be well designed. The MIL-PRF-32070A does place requirements on the workmanship of the final assembled product and includes the quality of soldering, wire routing, and harness/cable shielding requirements.One hinderance with implementation of much of this equipment is the time needed to build the specific test package (place what voltage/current on which pin and what the expected result should be), and the connection cables from the TPH to the UUT. It can be done, but it can be a time-consuming process.
Conclusion
The MIL-PRF-32070A places requirements on automated test equipment but does not place requirements on the types of faults or the sensitivity of the measurements – that is left to the individual application. As such, it is suggested that comparative testing be performed on any TPH prior to fielding a full suite as part of maintenance operations.
Further, it is important to remember what this equipment is: test equipment to help identify the current condition of the wiring – by its very nature it is not predictive. To get data to support predictive wiring system maintenance requires focused testing and analysis available from Lectromec. We have helped dozens of fleets get ahead of their wiring system maintenance needs saving millions of dollars of reworked and aircraft downtime.