
Separation standards are starting to emerge to help improve wire management systems. A number of airworthiness directives have been recently issued dealing with the wire hazards that result from lack of separation, either from other wires or structure (see box). System functionality is assured by adequate separation, highlighting that the airplane’s Electrical Wire Interconnect System (EWIS) is a vital part of the maintainability and reliability of the airplane.
The lack of industry-wide standards for adequate separation is apparent from a variety of documents indicating there is no universal guidance for what constitutes minimum safe separation:
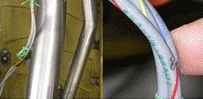
The National Transportation Safety Board (NTSB)’s final report of the TWA Flight 800 crash (caused by electrical arcing) states:
Although airplane manufacturers generally provide protection for certain critical electrical circuits, there is no FAA regulation that specifies wire separation criteria or identifies which circuits must be protected. … Safety Board investigators reviewed the general wire separation standards and practices of several airplane manufacturers and found that these standards are not uniform. For example, Douglas Aircraft Company specified that wiring for certain systems (including FQIS and other fuel system wiring, fire warning system wiring, primary generator feeder cables, and electro-explosive devices) must be separated by at least 3 inches from other electrical wiring. In contrast, Boeing specifications do not require protection for some of the systems specified by Douglas (such as the FQIS) and, for those systems that are designated as protected, the required separation distance is only ¼ inch in pressurized areas and ½ inch in unpressurized areas. The potential for short circuits to damage nearby wiring (more than 1½ inches away) has been documented in Safety Board investigations of numerous accidents and incidents.
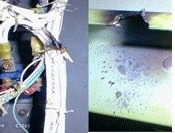
In the final report of the Swissair Flight 111 crash (caused by electrical arcing), the Transportation Safety Board (TSB) of Canada found, “…that there are limitations associated with the interpretation and application of FAR 25.1353(b). In aircraft design, it is not always possible to maintain physical separation between wires, especially in the cockpit area where, typically, space available for installations is confined. The guidance material does not specify what measures or criteria would be acceptable to meet the requirements of FAR 25.1353(b).”
The ATSRAC was sufficiently concerned about the lack of separation standards to register a formal statement to the Federal Aviation Administration (FAA):
An extensive review of wire design resources did not yield any definitive independent source that an aviation engineer can reference to determine what is good wire separation criteria for a given situation…Until such time as data is developed for a source document that details proper wire separation guidelines for varying conditions, design engineers must rely on ‘corporate knowledge’ when determining what is proper wire separation. This knowledge varies widely from one design department to another.

If you are interested in wire management systems, you may want to read Seven Considerations for Aerospace Wire Separation article.
In releasing a proposal to industry, the FAA recognized the lack of standards:
Today, there are no available criteria for what is a safe separation from a wiring fault perspective…Separation and/or segregation requirements due to wire bundle internal faults are subjective with little guidance available. … What are safe clearances between power wires and other essential wiring?
The closest to a policy may be the FAA’s Oct. 6 initiative requiring zonal inspections of all EWIS within 2” of structure or flight critical wiring circuits, hydraulic or pneumatic lines. However, this is a guideline for inspections, not design. Until such time as the FAA mandates specific separation criteria, the type certificate holders’ separation requirements should be followed.