Some failure mechanisms in aircraft wire systems technology are easy to find. Among the failure mechanisms faced by a wire, one is often overlooked: the failure of the layer to layer bond of wrapped wire insulation. When the bonding material fails to hold together the successive wraps of insulation, this is known as delamination.
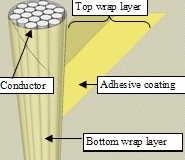
Wrapping of high performance materials is a means to significantly increase the thermal and mechanical performance of wire insulation. In wrapped insulating tape wire constructions (as opposed to extruded insulation types), there is an adhesive bonding material that holds successive layers of the same wrap together (see figure below). The bonding material is a melted plastic that can be as thin as 0.1mil and is usually a fluoropolymer. This bond holds the various layers together to complete the insulation system. Failure of the bonding material can lead to reduced abrasion resistance or the ingress of contaminates, such as fluids, which may reach the conductor, leading to electrical shorting or corrosion.
The quality of how successive wraps of insulation are held together is usually built into the wire design and in the manufacturing process. Qualification testing of each construction type is done to assure high quality wire. Despite this thorough examination, there is no performance testing of the individual bonding layers; a potential means of validating the construction of these wires and the adhesive layer may be via forced hydrolysis testing. This test involves the submersion of the wire into a high temperature water bath under a severe bending stress. Depending on the specification to which the wire is being tested, the test may take between 3,000 – 5,000 hours.
If you would like to learn more about wire systems, you can read Lectromec’s The Age of your Aircraft and Wire Systems Implications.
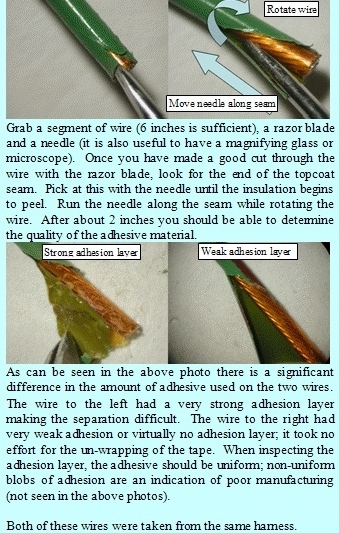
Delamination is a failure mode that does not exclusively appear itself in wires that use a single wrapped insulation system. Composite or multi-material constructions may also exhibit this failure mode. Delamination can be caused by the environments to which the wire is exposed; environmental factors such as excessive temperatures and temperature cycling can weaken the bonding material. Mechanical strains like high vibration, tight bends, excessive force, and improper anchoring can be contributing influences to adhesive failures.
During recent work performed by Lectromec on harnesses removed from a military aircraft, it was noticed that there was significant variation in the adhesion or bonding quality within the wires taken from the same bundle. The adhesive layer on some wires made it near impossible to unwrap the insulation, while on others it was as though there was no adhesive layer at all. The fact is that unless there is a breach in the top coat of the wire, it is unlikely that you would be able to see any signs of delamination.
At this time there is no practical or effective way of testing a wire harness for delamination other than by performing selective sampling. The box above provides a procedure to investigate delamination of in-service wire.