Over the years, the Lectromec website has received hundreds of thousands of visits. Often the topic of interest deals with Aircraft Wire Service Life Extension Programs. Because of this popularity, the Lectromec Podcast sat down with the president of Lectromec, Michael Traskos, to talk about Service Life Extension, or SLEP.
During the interview Michael starts by defining what SLEP is and who needs it. From there, the discussion moves on to which standards apply and talks about success stories. The physical process of aircraft service life extension can be difficult to understand, so Michael details what is involved.
The 18 minute interview finishes with challenges inherent in any Aircraft Service Life Extension Program and gives reasonable predictions about where the process is heading. You can listen here or read the transcript below:
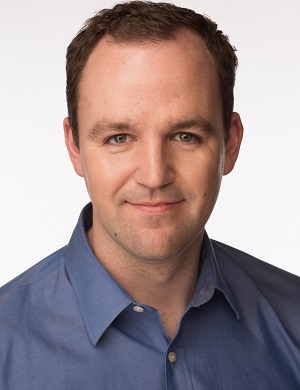
John Gilroy: Welcome to the Lectromec podcast with John Gilroy. Lectromec provides you the turn key solution for aerospace risk assesment, testing, and certification. The purpose of this podcast is to keep you informed of trends in the rapidly changing aerospace industry.
Our guest today is none other than Michael Traskos, president of Lectromec. How are you Michael?
Michael Traskos: I’m doing well John. How are you doing today?
John Gilroy: Well, being the president of Lectromec you must have some background in aerospace wire testing. Tell the listeners here what your background is please Michael.
Michael Traskos: Well, I started with Lectromec in 2004, I was brought on board by Dr. Armin Bruning the, the founder of Lectromec. And have been working on a variety of projects from FAA to NASA, to commercial, both aerospace and wire companies, manufacturing companies, since that time. When I started with Lectromec I was a … had a master’s in applied physics. And in the last year I gained a FAA EWIS DER, certification.
John Gilroy: So, I think we can assume with, ten, eleven years experience, master’s degree, and the DER certification, you can speak with authority about a wide range of topics involving aircraft wiring.
Michael Traskos: I, would hope so, I’m also the vice-chairman of one of the SAE committees on wire installation and in the leadership for the wire component specifications in the SAE meetings.
John Gilroy: My job here at Lectromec is to, take a look at the website, maybe look at analytics and see what’s popular and what isn’t. The popular phrase would be what’s hot and what’s not. And if I just look at the last two or three years, what I see the most popular topic on the website again, and again, month after month, is risk assessment and EWIS assesment for service life extension programs.
Now, if you’re not a professional that’s a that’s a mouthful. Let’s just kind of break this up a little bit. EWIS … Why don’t you define what EWIS is and talk about this topic of service life extension programs?
Michael Traskos: I’d be glad to. EWIS, the Electrical Wire Interconnect Systems, covers everything from circuit breakers down through the grounding points. So that means your rain terminals, your wire, your routing, clamps, cables, everything that carries power from the distribution down through where it’s used and really returns back to the power source.
The concept for EWIS really came around…I guess it was actually named back in the 2000’s. And before then, there was a lot of work, a lot of historical knowledge within each of the organizations and that was built up over time. And the FAA, after two major commercial incidents, went ahead and did a lot of research to the development and the advancement of the wiring into a wiring system. And that’s how we got to EWIS as a system.
With regard to service life extension Programs (SLEP), this is something that’s been around for a number of years and it’s relatively new to the wiring system. Historically, most of the maintainers will look to evaluate the engines, the structures, and do all of those other components once an aircraft has reached the end of it’s certified life. And so the idea with the service life extension is to go beyond the original certified life to extend the life of the aircraft and the usability for another five, ten, maybe twenty years.
For examining wires there are a lot of standards, a lot of recommendations for the assesment of wires before they get out into the aircraft. There’re a lot of handbooks for examining what you should look for in the wiring system once they’re installed. But there’s no real standard once they’re installed.
John Gilroy: So this was initially popularized in the military community I would assume. Is that right?
Michael Traskos: You’re typically going to find this in the military area. They have a lot of aircraft that are very similar, and there’s a lot of value in well maintaining those aircraft.
John Gilroy: So, aircraft wire service life extension is normally associated with EWIS so … That’s the whole phrase, it’s called EWIS risk assesment for service life extension … So, who needs it beside the military?
Michael Traskos: This can also be applied to the commercial sector. Obviously what you want to do is maximize the investment into all the goods, all of your capital. And by extending the life of these aircraft and making sure that they’re airworthy, that you’re not spending more maintenance than makes it profitable. You want to make sure those are reliable. And it’s just as important to the commercial sector. You need to look out to the fleets that are in operation today and they’re MD-80’s and MD-88’s that have been flying for more than 30 years and in all likelihood they’re going to be out there for eh, maybe past 40 years.
John Gilroy: And my guess is there are standards involved in examining wires uh, who provides these standards?
Michael Traskos: For examining wires there are a lot of standards, a lot of recommendations for the assesment of wires before they get out into the aircraft. There’re a lot of handbooks for examining, what you should look for in the wiring system once they’re installed. But there’s no real standard once they’re installed. You can use the military 5088 or what has become the more modern version, the 50881 from the SAE. And that defines how items should be installed, how they should be identified, and really some of the key considerations as part of the installation.
John Gilroy: And so a lot of the decisions you make in regards to wires usually are data-based decisions aren’t they?
Michael Traskos: As with any part of the maintenance of an aircraft, you want to do it not just based on anecdotal evidence or experience. You actually want to do it with a data driven approach. That way you’re not doing a cookie cutter approach across all the fleets. Because some aircraft have different problems than others.
And so the service life extension process that’s outlined for the EWIS in military handbook 525 provides a thorough evaluation of the EWIS and can be used directed towards a data driven approach. One of the benefits that you get with this process is that if you know you need your aircraft to fly for another ten, fifteen, twenty years and you use this process, you’ll know where the risks are in the aircraft. And so, because these EWIS components degrade, when replacement is necessary. And also some of the work that Lectromec has done recently, we have a better idea when increased maintenance or inspection of these harnesses in the EWIS will greatly benefit the reliability of the aircraft.
John Gilroy: It sounds like this directly impacts return on investment for an aircraft owner doesn’t it? I mean if you extend the life that’s a significant savings.
Michael Traskos: Exactly, and if you can extend the life another five, ten years, a lot of investment has been put into training the maintenance staff, building the recommended practices for maintaining that aircraft. The crews are trained on operation, so there’s a lot of investment in actually operating the aircraft. So by actually maintaining, and having these aircraft fly longer, you can better use that investment and get a better return on investment.
Did You Know? Lectromec’s EWIS component test lab is an ISO 17025:2005 certified facility. Lectromec has a wide range of wire and cable testing services.
John Gilroy: You know Michael, you’ve been around for about eleven years in this business. You must have some good success stories regarding service life extension programs.
Michael Traskos: I’ve been in the area, in this work and this field for, for eleven years, almost twelve at this point. Lectromec has been doing it for 31 years. We’ve had success on multiple military platforms, both foreign and domestic, but the one where we’ve had great success recently has been the work we’ve done on the F18’s for the U.S. Navy. Some of the research that we’ve been recently working on has helped to better understand when it is necessary and really, when this should be scheduled for inspecting the wiring system.
Historically we used to look at when harness replacement is necessary and certainly recommended. But based on our models we realized there was so much more value there when you could take the data gathered from degradation assessments, look at what the data is telling us, and then apply that to in-service conditions.
When you look at the aircraft and you say, “Okay my harness, or my wiring system is degrading.” There’s a point between when it’s starting to show age related failures and when replacement is necessary. There’s that period where improved, directed maintenance can help extend the life of those aircraft. And that’s something that we were able to apply to the F18’s and they’re just starting to implement as part of their overall service life extension program.
John Gilroy: And F18’s are all over the world aren’t they?
Michael Traskos: Those are in multiple countries and I believe they’re still being built.
John Gilroy: Great, so what is the exact process behind the service life extension program itself?
Michael Traskos: Exact process is fairly well defined as part of the military handbook 525 and if you go on to Lectromec’s website there’s also a white paper that does a pretty good job of describing the overall process. Basically it’s a seven-step process that starts with looking at the aircraft data from an engineering approach and says, “What is my severity of failure?” You need both severity and probability of failure to identify the risk to an aircraft, or to any system. So you first step is to look at that. Second task, look at the maintenance data, interview the people that have been working on the aircraft, then go onto the aircraft, do inspections, and bring some of the samples, some of the EWIS back for in-lab evaluation and degradation assessment.
Once that information is gathered you can bring this altogether and create a comprehensive risk assessment for the wiring system, for the EWIS. What that then provides is the information for a data-driven decision making … and really what can be done to mitigate problems you know, if there are replacements that are necessary, or really what you can do from a maintenance perspective to extend the reliability of your EWIS.
John Gilroy: Now, there must be many challeges just inherent in performing service life extension for aircraft wire systems. I mean we’re almost giving a textbook discussion of it. Like it’s just go out back and pull a wire and bring it all in. I mean this can be challenging, the whole process can’t it?
That’s some of the challenges and other challenges that we see as part of EWIS SLEP because the wiring system is not as glamorous as the structure or the engines. It’s near the bottom, in terms of priorities. I’ve often heard that EWIS is the Rodney Dangerfield of systems, it can’t get any respect. So that’s sometimes the difficulty for getting funds or labor allocated to extending the life of a wiring system.
Michael Traskos: The overall process can be challenging and that’s where it takes time, and it’s a methodical process. You don’t just run into the aircraft and start pulling out wires and say I got some. The process does take time. There are challenges oftentimes to find the aircraft which are a good representative aircraft for the fleet. And, really identifying when is the best time to have these aircraft out of service.
Sometimes the aircraft are already in the bone yard and it’s easy to remove the wiring harnesses or the EWIS. Sometimes they are in-service aircraft and that has to be scheduled as part of their overall maintenance. That’s some of the challenges and other challenges that we see as part of EWIS SLEP because the wiring system is not as glamorous as the structure or the engines. It’s near the bottom, in terms of priorities. I’ve often heard that EWIS is the Rodney Dangerfield of systems, it can’t get any respect. So that’s sometimes the difficulty for getting funds or labor allocated to extending the life of a wiring system.
John Gilroy: We know there’s challenges in this field, a lot of technical changes here in the last few years. What is the future of SLEP, Service Life Extension Program? What do you see happening in the next five to ten years?
Michael Traskos: There are a lot of fleets that are reaching the end of their service life and whether it’s the engineering service life that was originally established, or they’ve already gone through a service life extension and it appears as though they need to fly for another ten to fifteen years. There are a lot of fleets that are coming to this point and service life extension is going to become a larger priority overall. There’s a lot of fleets that are still quality they’re not showing significant signs of degradation and you know, there’s a lot of investments into that: into the actual maintenance of these aircraft.
John Gilroy: So you just look into the expense it takes to pull an aircraft away and do preventative maintenance on it. I mean, if you can extend its life for four or five years, I mean that’s a significant return on investment.
Michael Traskos: It is, and that’s where the service life extension—once people start to see what the benefits are, see that you can get a reliable aircraft and make it economical and get the return on investment—that’s where I see there’s definitely gonna be growth and continued opportunities there.
John Gilroy: Now, Michael with the Lectromec podcast about this time I always ask my guests what their favorite aircraft is. And I’ve gotta put that question to you. You’ve been a lot of places, all over the world … China, and Europe, and who knows where … So, what’s your favorite aircraft?
Michael Traskos: My most recent experience that’s been on an aircraft, I really had to enjoy the Boeing 787. Just a phenomenally built aircraft, really enjoyable to be on. One I’m looking forward to is you know, we’re right outside Dulles Airport here in Virginia and right around two thirty to three o’clock every day there’s a … Actually, they’re two Airbus 380’s that fly in. And that’s just an impressive piece of machinery. I look forward to having an opportunity to be on it some day.
John Gilroy: I hope you are. I’d like to thank Michael Traskos, president of Lectromec for this interview. Thanks, Mike.
Michael Traskos: Thanks John.
John Gilroy: And thank you for listening to the Lectromec podcast. If you would like to learn more about aircraft wiring please visit our website at Lectromec.com. We have free white papers, newsletters, videos, blogs, and much more.